Discover the Benefits of Using Alumina Desiccant for Efficient Moisture Control
By:Admin
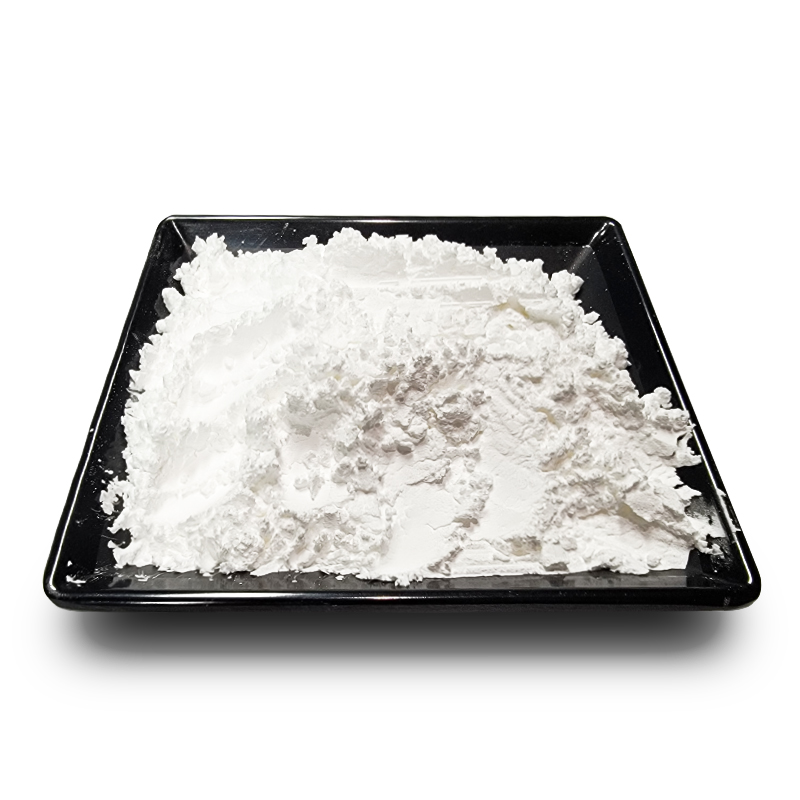
In today's fast-paced world, proper moisture control is crucial to maintaining the quality and integrity of numerous products and components. Whether it's preserving pharmaceuticals, electronics, or food items, companies across industries are constantly seeking effective solutions to combat moisture-related issues. Enter Alumina Desiccant - a game-changing product that has revolutionized the field of moisture control.
Alumina Desiccant, backed by its state-of-the-art manufacturing process and cutting-edge technology, provides unmatched moisture absorption capabilities. With its superior performance, it has quickly become an essential tool for countless businesses worldwide.
Developed by a leading company in the field, Alumina International, this highly effective desiccant is manufactured using a unique blend of additives and high-quality alumina materials. These ingredients work in perfect harmony to offer exceptional moisture absorption, ensuring that sensitive materials remain dry and moisture-free.
One of the key advantages of Alumina Desiccant is its wide range of applications. It is extensively used in the pharmaceutical industry, where moisture-controlled environments are critical in preserving the efficacy of drugs and other medical supplies. By eliminating moisture and maintaining stringent temperature conditions, Alumina Desiccant ensures that medicines remain safe and effective for patients in need.
The electronics industry has also been quick to embrace the benefits of Alumina Desiccant. Moisture can wreak havoc on sensitive electronic components, causing irreversible damage and rendering them useless. With its advanced moisture absorption capabilities, Alumina Desiccant safeguards expensive electronic equipment during storage and transportation, preventing corrosion and extending their lifespan. This allows companies to provide superior-quality products to their customers while reducing the risk of costly repairs or replacements.
Additionally, the food industry has found an invaluable ally in Alumina Desiccant. Freshness and quality are paramount in the food sector, and moisture can greatly undermine these attributes. By effectively absorbing moisture and preventing the growth of mold and other harmful microorganisms, Alumina Desiccant ensures that food products remain safe and tasty for consumers. From cereals to dried fruit, this innovative desiccant helps maintain optimal quality and extends the shelf life of various food items.
Furthermore, Alumina Desiccant also finds application in the automotive industry, where it protects important vehicle components and spare parts from moisture-induced damage. Whether it's the sensitive electronic systems that power modern cars or the metal parts susceptible to rust, Alumina Desiccant guarantees the integrity and longevity of these components, ultimately leading to enhanced vehicle performance and customer satisfaction.
Not only does Alumina Desiccant effectively combat moisture-related issues, but it is also eco-friendly. With increasing global awareness of environmental concerns, businesses are actively seeking sustainable solutions. Alumina International, the company behind this groundbreaking product, prioritizes sustainability by using environmentally friendly production techniques and materials. This commitment ensures that companies can achieve moisture control goals while reducing their ecological footprint.
In conclusion, Alumina Desiccant has revolutionized the field of moisture control solutions across various industries. Its exceptional absorption capabilities, broad range of applications, and environmentally friendly production make it an invaluable tool for countless businesses worldwide. As technology continues to advance, Alumina Desiccant remains at the forefront of combating moisture-related issues, ensuring the preservation of both product quality and customer satisfaction.
Company News & Blog
Discover the Latest Advancements in Alumina Research - Unveiling the Potential of Gamma Alumina
Gamma Alumina: Advancing Materials Science and Redefining Industrial PossibilitiesGamma Alumina is a high-performance material company that is redefining the industrial possibilities. The company takes pride in offering innovative solutions that are changing the way we look at materials science. Gamma Alumina products have diverse applications in various industries, including petrochemical, electronic, and pharmaceutical, among others. But what is Gamma Alumina, and what makes it so exceptional?Gamma Alumina is a type of alumina that exhibits unique physical and chemical properties, including high surface area, high purity, and thermal stability. This makes it an ideal material in many industrial processes. The company produces gamma alumina nanopowders using a proprietary method that combines cutting-edge technology and innovative process engineering.One of the most significant advantages of Gamma Alumina is its excellent catalytic properties. Gamma Alumina is used as a catalyst support in chemical reactions, enhancing reaction efficiency, and selectivity. The nanopowders offer a significant surface area to volume ratio, providing an optimized surface for catalytic activity. This implies that the material can catalyze a high rate of chemical reactions with minimal energy input, making it energy efficient and sustainable.Gamma Alumina is also widely used as an adsorbent material, where it can selectively adsorb specific molecules from gas or liquid streams. This has led to its use in purification processes to remove impurities from various industrial products such as natural gas, petrochemicals, and water. Its high surface area and unique pore structure make it an ideal material for selective separation processes, improving product purity and quality.Another significant application of Gamma Alumina is in the manufacture of ceramics and electronic materials. Gamma Alumina is used as a precursor for the production of advanced ceramics and glass matrices through the sol-gel process. It is also used in the production of electronic ceramics such as capacitors, insulators, and superconductors. Gamma Alumina offers a high degree of purity, thermal stability, and good dielectric properties, making it an ideal material in electronic applications.Gamma Alumina is also used in the pharmaceutical industry. It is used as a drug carrier in drug delivery systems, and as an intermediate in peptide synthesis. The material's unique adsorption properties allow it to adhere to specific drug molecules, improving the efficacy of the drug. Gamma Alumina is also used in bioceramic applications such as bone cement, where it provides mechanical stability and biocompatibility.In conclusion, Gamma Alumina is an exceptional material with diverse applications across various industries. Its unique physical and chemical properties make it an ideal material in many industrial processes. At Gamma Alumina, we are continually redefining the industrial possibilities by offering innovative solutions that enhance efficiency and sustainability in industrial processes. Our proprietary method of producing gamma alumina nanopowders allows us to deliver high-quality materials suitable for various applications. We are committed to advancing materials science, and our team of experts is always working to develop new applications of Gamma Alumina. We take pride in being at the forefront of materials science, and we look forward to expanding our footprint in different industries.
Sulfur Tolerant Shift Catalyst: Key Benefits and Uses
Sulfur Tolerant Shift Catalyst: A Breakthrough in Industrial TechnologyInnovative technology has always been at the forefront of industrial progress, driving advancements in efficiency and sustainability. One such breakthrough is the development of a Sulfur Tolerant Shift Catalyst, a game-changing catalyst that promises to revolutionize the way industrial processes are conducted.The Sulfur Tolerant Shift Catalyst, developed by a leading chemical company, is designed to address the challenges posed by sulfur-containing feedstocks in the production of hydrogen and other important industrial processes. These feedstocks often contain sulfur compounds that can poison conventional shift catalysts, leading to reduced efficiency and increased maintenance costs. The new catalyst, however, is able to withstand the detrimental effects of sulfur, offering a more reliable and cost-effective solution for industrial applications.The company behind this groundbreaking technology is a global leader in the development and manufacturing of catalysts, with a strong focus on innovation and sustainability. With a history of delivering high-performance solutions for diverse industrial processes, the company has established itself as a trusted partner for businesses seeking to enhance their operational efficiency and environmental performance.The Sulfur Tolerant Shift Catalyst represents a significant step forward for the company, showcasing its ability to develop cutting-edge solutions that address the evolving needs of the industry. By enabling the use of sulfur-containing feedstocks without compromising process efficiency, the catalyst opens up new possibilities for businesses looking to optimize their operations while reducing their environmental impact.The development of the Sulfur Tolerant Shift Catalyst is a testament to the company's commitment to research and development, as well as its dedication to providing sustainable solutions for the industry. Through ongoing investment in innovation and collaboration with partners and customers, the company continues to push the boundaries of what is possible in the field of catalysis, driving positive change in the industrial sector.Furthermore, the company's expertise in catalyst manufacturing and process optimization has allowed it to tailor the Sulfur Tolerant Shift Catalyst to meet the specific requirements of different industries and applications. This flexibility makes the catalyst a versatile and adaptable solution, suitable for a wide range of industrial processes where sulfur tolerance is a critical factor.In addition to its technical performance, the Sulfur Tolerant Shift Catalyst also offers environmental benefits by enabling the use of alternative feedstocks that might otherwise be considered unsuitable due to their sulfur content. By minimizing the need for expensive and energy-intensive sulfur removal processes, the catalyst helps to reduce the overall environmental footprint of industrial operations, supporting the transition towards more sustainable and resource-efficient practices.Looking ahead, the company is committed to further advancing the capabilities of the Sulfur Tolerant Shift Catalyst, exploring opportunities to expand its application to new industries and processes. By harnessing the power of innovation and collaboration, the company aims to drive positive change in the industry and contribute to the development of a more sustainable and efficient industrial landscape.As the Sulfur Tolerant Shift Catalyst continues to gain traction in the market, it has the potential to become a game-changer for industrial processes reliant on sulfur-containing feedstocks. By offering a reliable and cost-effective solution for overcoming the challenges of sulfur tolerance, the catalyst represents a significant advancement in industrial technology, with far-reaching implications for the future of the industry.In conclusion, the development of the Sulfur Tolerant Shift Catalyst stands as a testament to the company's commitment to innovation and sustainability, showcasing its ability to deliver high-performance solutions that address the evolving needs of the industry. With its potential to drive positive change and enable more sustainable industrial practices, the catalyst is set to make a lasting impact on the way industrial processes are conducted, creating new opportunities for businesses to enhance their performance and reduce their environmental footprint.
Highly Effective Catalyst ZSM-5 Proven to Boost Chemical Reactions
ZSM-5 Catalyst, a breakthrough technology in the field of catalysis, has recently made waves in the industry with its exceptional performance in various chemical processes. This innovative catalyst, developed by a leading chemical company, has revolutionized the way chemical reactions are carried out, paving the way for more efficient and sustainable production processes.The ZSM-5 Catalyst is a type of zeolite catalyst that is widely used in the petrochemical industry for a range of applications, including the production of gasoline, diesel, and other fuels. What sets this catalyst apart from others is its unique structure, which allows for enhanced selectivity and improved yields in various reactions. This has led to significant improvements in productivity and cost-efficiency for companies that have adopted this technology.One of the key features of the ZSM-5 Catalyst is its ability to perform shape-selective reactions. This means that it can selectively catalyze certain molecules while excluding others, leading to higher yields of desired products. Additionally, this catalyst has shown remarkable stability under harsh reaction conditions, making it a reliable and long-lasting solution for industrial processes.In addition to its applications in the petrochemical industry, the ZSM-5 Catalyst has also shown promise in the field of environmental protection. Its use in the conversion of harmful pollutants into less toxic substances has opened up new possibilities for cleaner and more sustainable industrial practices. This has significant implications for reducing the environmental impact of chemical manufacturing and lowering carbon emissions.The company behind the development of the ZSM-5 Catalyst has a strong track record of innovation and excellence in the chemical industry. With a focus on research and development, they have consistently pushed the boundaries of what is possible in catalysis, paving the way for new and improved processes that benefit both the industry and the environment. Their commitment to sustainability and continuous improvement is reflected in the performance of the ZSM-5 Catalyst, which has set a new standard for catalyst technology.The success of the ZSM-5 Catalyst can be attributed to the company's investment in cutting-edge research and development, as well as its dedication to understanding and meeting the needs of its customers. By actively engaging with industry partners and staying ahead of the curve in terms of technological advancements, the company has been able to develop a catalyst that addresses the most pressing challenges faced by the chemical industry today.Moving forward, the company is committed to further advancing the capabilities of the ZSM-5 Catalyst and exploring new applications for this groundbreaking technology. With ongoing research and development efforts, they aim to continue pushing the boundaries of catalysis and setting new benchmarks for performance and sustainability in the industry.In conclusion, the ZSM-5 Catalyst has emerged as a game-changer in the world of catalysis, offering unprecedented selectivity, stability, and sustainability in chemical processes. Its success is a testament to the innovative spirit and forward-thinking approach of the company behind its development, and it is set to have a lasting impact on the future of chemical manufacturing. As the industry continues to evolve, the ZSM-5 Catalyst stands as a shining example of what is possible through innovation and commitment to excellence.
New Catalyst Carrier Spheralite: An Innovative Solution for Chemical Processing
Catalyst Carrier Spheralite Revolutionizing the Chemical IndustryIn recent years, there has been a growing demand for innovative solutions in the chemical industry. Companies are constantly seeking new ways to improve the efficiency and sustainability of their processes. One company that is at the forefront of this movement is {Company Name}, a global leader in the development of advanced catalyst carriers. Their revolutionary product, Spheralite, is changing the game for chemical manufacturers around the world.{Company Name} was founded in 2005 with the mission of providing cutting-edge solutions for the chemical industry. With a team of dedicated experts and state-of-the-art facilities, the company has been able to develop a range of high-performance catalyst carriers that are unmatched in quality and reliability. Their flagship product, Spheralite, has quickly gained a reputation for its exceptional performance and versatility.Spheralite is a unique catalyst carrier that is designed to optimize the performance of chemical processes. Its spherical shape and uniform size distribution provide a high surface area, which allows for better mass transfer and improved reaction kinetics. This results in higher yields and lower energy consumption, leading to significant cost savings for manufacturers. Additionally, Spheralite is highly resistant to fouling and attrition, ensuring a longer lifespan and reduced maintenance requirements.One of the key advantages of Spheralite is its adaptability to a wide range of catalytic applications. It can be customized to suit specific chemical reactions, making it a versatile and reliable choice for various industries. Whether it is used in petrochemical refining, environmental remediation, or industrial gas processing, Spheralite consistently delivers exceptional performance and reliable results.{Company Name} has also made significant investments in research and development to further enhance the capabilities of Spheralite. By leveraging the latest advances in materials science and manufacturing technology, they have been able to continuously improve the product's performance and durability. This dedication to innovation has solidified {Company Name} as a trusted partner for chemical manufacturers worldwide.Moreover, Spheralite is manufactured using environmentally friendly processes and is fully recyclable, aligning with the growing emphasis on sustainability within the chemical industry. This has made it an attractive option for companies looking to reduce their environmental footprint while maintaining high levels of productivity.In addition to its technical advantages, {Company Name} has built a reputation for providing exceptional customer support and technical expertise. Their team of experienced engineers and chemists works closely with customers to optimize the use of Spheralite in their processes, ensuring maximum efficiency and performance.The impact of Spheralite in the chemical industry has been nothing short of transformative. Companies that have adopted the product have reported significant improvements in their production processes, leading to increased yields, reduced emissions, and substantial cost savings. This has not only boosted their bottom line but has also positioned them as leaders in sustainability and innovation.Looking ahead, {Company Name} is committed to further advancing the capabilities of Spheralite and developing new solutions to address the evolving needs of the chemical industry. As the demand for more efficient and sustainable processes continues to grow, Spheralite is poised to play a key role in shaping the future of chemical manufacturing.In conclusion, the innovative catalyst carrier Spheralite developed by {Company Name} is revolutionizing the chemical industry by delivering unmatched performance, sustainability, and cost savings. With its unique capabilities and proven track record, Spheralite has become a powerful tool for companies looking to stay competitive in a rapidly changing global market. As the company continues to push the boundaries of innovation, it is clear that Spheralite will continue to lead the way towards a more efficient and sustainable future for the chemical industry.
Newly Developed ZSM-48 Shows Promising Results in Latest Study
Innovative Zeolite Zsm-48 Developed by Leading Chemical CompanyA groundbreaking advancement has been made in the field of zeolite technology with the development of Zsm-48 (brand name removed), a highly efficient and versatile zeolite developed by a leading chemical company. This new development has the potential to revolutionize various industrial processes and applications, thanks to its unique properties and performance characteristics.Zeolites are a class of minerals with a porous and crystalline structure, which makes them ideal for a wide range of applications, including catalysis, adsorption, and ion exchange. The unique structure and chemical composition of zeolites allow them to selectively adsorb and catalyze various molecules, making them invaluable in numerous industrial processes.The development of Zsm-48 (brand name removed) is a significant achievement in the field of zeolite technology, as it offers unprecedented performance and versatility. The new zeolite exhibits exceptional acidity and thermal stability, making it ideal for catalytic applications in the petrochemical and chemical industries. Additionally, its unique pore structure enables highly selective adsorption of molecules, making it well-suited for gas separation and purification processes.The company behind this innovative development is a global leader in the chemical industry, with a track record of pioneering research and development in the field of zeolite technology. Leveraging their expertise in materials science and chemical engineering, the company has successfully engineered Zsm-48 (brand name removed) to meet the demanding requirements of modern industrial processes.In addition to its outstanding performance characteristics, Zsm-48 (brand name removed) is also environmentally friendly, offering a sustainable alternative to traditional catalysts and adsorbents. Its high efficiency and selectivity enable significant energy savings and reduced emissions, contributing to a more sustainable and eco-friendly industrial production.The potential applications of Zsm-48 (brand name removed) are vast and diverse, spanning various industries such as petrochemicals, fine chemicals, environmental protection, and energy. Its superior catalytic performance makes it an ideal candidate for upgrading and refining of hydrocarbon feedstocks, while its exceptional adsorption properties can be harnessed for gas separation and purification processes.The development of Zsm-48 (brand name removed) represents a major milestone in the advancement of zeolite technology, opening up new possibilities for enhancing industrial processes and addressing environmental challenges. With its exceptional performance, sustainability, and versatility, this innovative zeolite is poised to make a significant impact across various sectors, paving the way for more efficient and sustainable production processes.As the global demand for advanced materials and sustainable technologies continues to grow, the introduction of Zsm-48 (brand name removed) heralds a new era of innovation and progress in the field of zeolite technology. With its groundbreaking properties and potential applications, this new zeolite is set to become a cornerstone of modern industrial processes, offering unparalleled performance and sustainability.
Alumina production in Gama sees positive growth
Gama Alumina is a prominent player in the alumina industry, known for its high-quality products and innovative techniques. The company has been at the forefront of developing and providing alumina products for various industries, including aerospace, automotive, and electronics.Established in 1992, Gama Alumina has steadily grown and expanded its operations to become a leading alumina supplier in the global market. With a strong focus on research and development, the company has continuously strived to improve its products and processes, making it a preferred choice for many renowned companies.One of the key factors that set Gama Alumina apart from its competitors is its commitment to sustainability and environmental responsibility. The company has made significant investments in eco-friendly technologies and has taken proactive measures to reduce its carbon footprint. This dedication to sustainability has not only helped Gama Alumina to meet the increasing demand for environmentally friendly products but has also positioned it as an industry leader in sustainable practices.Gama Alumina's product range includes a wide variety of alumina grades, each specifically designed to meet the unique needs of its diverse customer base. Whether it's high-purity alumina for the semiconductor industry, or specialty alumina for advanced ceramics, the company's products are known for their exceptional quality and consistency.In addition to its core product line, Gama Alumina also offers custom solutions to cater to specific customer requirements. Its team of experienced professionals works closely with clients to understand their needs and develop tailored alumina products that meet the highest standards of performance and quality.Furthermore, the company has a strong focus on customer satisfaction, ensuring timely delivery and comprehensive technical support. This commitment to excellence has earned Gama Alumina a reputation for reliability and integrity in the industry.Gama Alumina's state-of-the-art manufacturing facilities are equipped with the latest technology and operated by a skilled workforce. This combination of advanced machinery and skilled personnel ensures that the company consistently delivers products of the highest quality, meeting and often exceeding industry standards.Looking ahead, Gama Alumina is committed to further expanding its global presence and solidifying its position as a leading alumina supplier. The company is constantly exploring new opportunities for growth and development, with a continued focus on innovation and sustainability.In conclusion, Gama Alumina has established itself as a reputable and forward-thinking company in the alumina industry. With its unwavering commitment to quality, sustainability, and customer satisfaction, the company is well-positioned to thrive in the ever-evolving global market. As it continues to innovate and expand, Gama Alumina looks set to maintain its leadership role in the industry for years to come.
Highly Effective Gamma Alumina Catalyst for Industrial Applications
Gamma Alumina Catalysts: Revolutionizing the Oil and Gas IndustryIn the world of oil and gas production, efficiency and productivity are paramount. Companies are constantly searching for ways to streamline their processes and improve their bottom line. Enter Gamma Alumina Catalyst, a cutting-edge solution that is revolutionizing the industry.Gamma Alumina Catalyst, developed by a leading chemical company, is a high-performance catalyst that is specifically designed for use in oil and gas refining processes. The catalyst offers a wide range of benefits, including improved product yields, increased process efficiency, and reduced energy consumption. This innovative solution has quickly become a game-changer for companies looking to optimize their operations and stay ahead of the competition.The use of Gamma Alumina Catalyst has had a transformative impact on the industry, allowing companies to significantly enhance their production capabilities and achieve higher levels of output. By leveraging this advanced catalyst, companies are able to improve the quality of their products, reduce waste, and ultimately increase their profitability. This has made Gamma Alumina Catalyst a highly sought-after solution for companies in the oil and gas sector.One of the key advantages of Gamma Alumina Catalyst is its versatility. The catalyst is highly effective in a wide range of refining processes, including hydroprocessing, petrochemical manufacturing, and environmental protection. This flexibility has made it an invaluable tool for companies looking to improve their refining operations and address the unique challenges they face.Furthermore, the company behind Gamma Alumina Catalyst has a proven track record of delivering high-quality, innovative solutions to the oil and gas industry. With decades of experience and a commitment to excellence, the company has established itself as a trusted partner for companies looking to enhance their operations and achieve their business goals. This reputation for excellence has made Gamma Alumina Catalyst the catalyst of choice for some of the biggest players in the industry.In addition to its technical capabilities, the company places a strong emphasis on sustainability and environmental responsibility. The development of Gamma Alumina Catalyst reflects the company's commitment to creating solutions that not only improve efficiency and productivity but also minimize the environmental impact of oil and gas production. By using Gamma Alumina Catalyst, companies are able to reduce their carbon footprint and contribute to a more sustainable future for the industry.As the demand for Gamma Alumina Catalyst continues to grow, the company remains dedicated to pushing the boundaries of innovation and delivering new, advanced solutions to the market. With ongoing research and development efforts, the company is constantly working to improve the performance and capabilities of its catalyst, ensuring that it remains at the forefront of the industry.In conclusion, the introduction of Gamma Alumina Catalyst has had a profound impact on the oil and gas industry. By offering a versatile, high-performance solution for refining processes, the catalyst has enabled companies to enhance their productivity, improve their product quality, and achieve their business objectives. With a commitment to sustainability and a proven track record of excellence, the company behind Gamma Alumina Catalyst is poised to continue leading the way in delivering innovative solutions to the industry. As companies strive to optimize their operations and stay competitive in a rapidly evolving market, Gamma Alumina Catalyst stands out as a game-changing solution that is driving the industry forward.
Effective Alumina Desiccant for Moisture Absorption: Benefits and Uses
Alumina Desiccant: The Ultimate Solution for Moisture ControlIn today’s fast-paced and interconnected world, moisture control is an essential aspect of many industries. From pharmaceuticals to electronics, the presence of moisture can lead to spoilage, degradation, and even malfunction of goods and equipment. This is where Alumina Desiccant comes in, offering a comprehensive solution to the challenges posed by excess moisture.Alumina Desiccant is a leading manufacturer and supplier of high-quality desiccant products. With a strong focus on innovation and customer satisfaction, the company has been at the forefront of the industry for over a decade. Its cutting-edge research and development facilities, coupled with a commitment to quality, have enabled Alumina Desiccant to provide superior products that meet the diverse needs of its global clientele.The company’s flagship product, Alumina Desiccant, is a highly effective moisture-absorbing material that is widely used in various industrial applications. Made from a special type of alumina, this desiccant has proven to be highly effective in controlling moisture and humidity levels in a range of environments. Whether it is used in the pharmaceutical industry to preserve the integrity of medicines, or in the electronics industry to protect sensitive equipment from moisture damage, Alumina Desiccant has emerged as the go-to solution for companies worldwide.One of the key features of Alumina Desiccant is its exceptional moisture absorption capacity. Unlike traditional desiccants, which may only be effective in specific humidity ranges, Alumina Desiccant can efficiently absorb moisture across a wide spectrum of relative humidity levels. This versatility makes it an ideal choice for industries where precise humidity control is critical.In addition to its superior performance, Alumina Desiccant also offers several other advantages over traditional desiccants. Its high chemical stability and low dust generation make it a safe and user-friendly option for a wide range of applications. Furthermore, its robust packaging ensures that the desiccant remains intact and effective, even in challenging environmental conditions.Alumina Desiccant also prides itself on its commitment to sustainability. The company’s manufacturing processes prioritize environmental responsibility, with a focus on reducing waste and energy consumption. This dedication to sustainability has not only earned Alumina Desiccant the trust of environmentally conscious customers but has also positioned the company as a leader in green desiccant solutions.As a customer-focused company, Alumina Desiccant places a strong emphasis on providing comprehensive support to its clients. From initial product selection to ongoing technical assistance, the company’s dedicated team of experts is always on hand to offer guidance and advice. With a global distribution network and a reputation for reliability, Alumina Desiccant ensures that its customers receive the highest level of service at every stage of their journey.Looking ahead, Alumina Desiccant is poised to continue its success story, further expanding its product range and reaching new markets. By leveraging its strong research and development capabilities, the company aims to innovate and develop new desiccant solutions that meet the evolving needs of its customers. With a clear vision, a commitment to excellence, and a track record of success, Alumina Desiccant is set to remain a trusted partner for businesses seeking effective moisture control solutions.In conclusion, Alumina Desiccant stands out as a driving force in the field of moisture control, providing top-quality desiccant products that deliver outstanding performance and reliability. With a strong foundation of research, innovation, and customer satisfaction, the company is well-positioned to continue leading the way in the industry. Whether it is in pharmaceuticals, electronics, or any other sector where moisture control is paramount, Alumina Desiccant’s products are the ultimate solution for businesses looking to protect their goods and equipment from the damaging effects of excess moisture.
Key Benefits of Activated Alumina Catalyst in Industrial Applications
Activated Alumina Catalyst: A Breakthrough in Industrial Chemical ProcessesActivated alumina catalysts have become a critical component in various industrial chemical processes, providing a cost-effective and efficient solution for a wide range of applications. These catalysts are widely used in the production of petrochemicals, polymers, and various other chemical compounds. One company at the forefront of this innovative technology is [Company Name].[Company Name] is a leading provider of activated alumina catalysts, offering a diverse range of products designed to meet the specific needs of industrial clients. Their catalysts are engineered to deliver exceptional performance, reliability, and cost-effectiveness, making them a preferred choice for numerous applications in the chemical industry.The unique properties of activated alumina catalysts make them highly effective in catalyzing various chemical reactions, including hydrocarbon processing, hydrogenation, and dehydration. These catalysts are capable of enhancing reaction rates and selectivity, leading to improved yields and higher product quality. Additionally, activated alumina catalysts are known for their thermal stability, mechanical strength, and resistance to poisons, making them ideal for demanding industrial environments.One of the key advantages of [Company Name]'s activated alumina catalysts is their customizable nature. The company works closely with clients to develop tailored catalyst solutions that meet their specific process requirements. This level of customization ensures that clients can achieve optimal performance and efficiency in their chemical processes, ultimately leading to cost savings and improved production outcomes.In addition to their exceptional product offerings, [Company Name] is committed to research and development to continuously improve their catalyst technology. The company invests in cutting-edge R&D facilities and a team of experienced chemists and engineers, enabling them to stay at the forefront of technological advancements in the industry. As a result, [Company Name] is able to bring new and innovative catalyst solutions to market, providing clients with access to the latest advancements in chemical process technology.Furthermore, [Company Name] places a strong emphasis on sustainability and environmental responsibility in their operations. Their activated alumina catalysts are designed to minimize environmental impact while delivering superior performance. By enabling more efficient and sustainable chemical processes, [Company Name] contributes to the reduction of greenhouse gas emissions and the overall environmental footprint of the chemical industry.[Company Name] also offers technical support and consultation services to assist clients in the implementation and optimization of their activated alumina catalysts. The company's team of experts works closely with clients to provide guidance on catalyst selection, process design, and operational best practices. This level of support ensures that clients can maximize the value of [Company Name]'s catalysts and achieve their production objectives.In conclusion, activated alumina catalysts play a crucial role in the chemical industry, enabling efficient and cost-effective production processes for a wide range of chemical compounds. With [Company Name] leading the way in catalyst innovation and customization, industrial clients have access to high-performance catalyst solutions that meet their specific process needs. By combining advanced technology, customization, and sustainability, [Company Name] is shaping the future of industrial chemical processes through its activated alumina catalysts.
New Study Finds Surprising Benefits of ZSM-5 Catalyst in Industrial Processes
ZSM-5 is a type of zeolite material that has been extensively used in various industrial applications. It is a highly crystalline material with a specific pore structure and acidity, making it a versatile catalyst in chemical and petrochemical industries. Recently, there have been significant advancements in the development and application of ZSM-5, particularly in catalyst and adsorbent technologies. This has been made possible through the collaborative efforts of researchers and engineers at the forefront of material science and chemical engineering. One of the companies leading the way in this field is {}. {} is a global leader in the development and production of advanced materials, including zeolites and catalysts. The company has a strong track record of innovation and has been at the forefront of developing new and improved materials for a wide range of industrial applications. In recent years, {} has been focusing on the development of ZSM-5-based catalysts and adsorbents with enhanced performance and stability. These efforts have resulted in the creation of novel materials with improved selectivity and activity, making them highly desirable for a wide range of applications, including the production of fuels, chemicals, and environmental remediation.One of the key areas of focus for {} has been the improvement of ZSM-5 catalysts for the conversion of methanol to olefins (MTO) and other hydrocarbon products. The development of highly active and selective catalysts for this process has the potential to revolutionize the production of light olefins, which are crucial building blocks for various plastics and polymers. By optimizing the pore structure and acidity of ZSM-5, {} has been able to develop catalysts that exhibit exceptional performance and durability, making them highly sought after in the industry.In addition to catalysts, {} has also made significant strides in the development of ZSM-5-based adsorbents for the removal of harmful contaminants from gas and liquid streams. By tailoring the pore size and surface chemistry of ZSM-5, the company has been able to create adsorbents with high capacity and selectivity for a wide range of pollutants, including volatile organic compounds (VOCs) and sulfur compounds. These adsorbents have the potential to significantly improve the efficiency of industrial processes and reduce the environmental impact of various chemical and petrochemical operations.Through its dedication to research and development, {} has been able to establish itself as a key player in the field of ZSM-5-based materials. The company's commitment to innovation and its extensive expertise in the design and production of advanced materials have positioned it as a leading provider of ZSM-5 catalysts and adsorbents for industrial applications worldwide.As the demand for high-performance catalysts and adsorbents continues to grow, {} remains at the forefront of developing new and improved ZSM-5-based materials to meet the evolving needs of the industry. With its focus on innovation and collaboration, the company is well-positioned to drive the advancement of ZSM-5 technology and its widespread adoption in various industrial processes.