Sulfur Tolerant Shift Catalyst: What You Need to Know
By:Admin
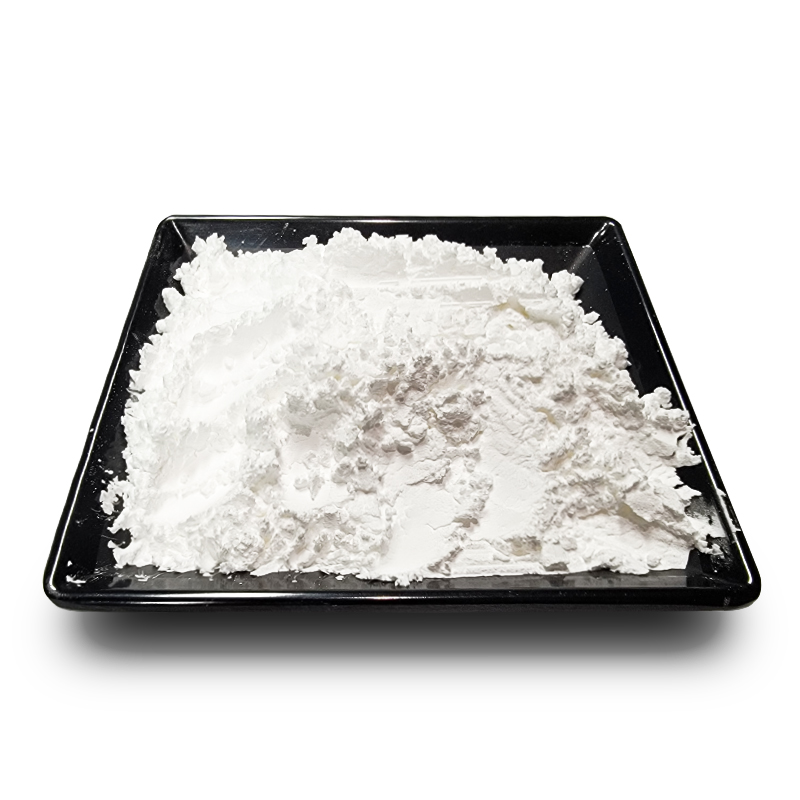
The global chemical industry is constantly evolving, with companies seeking innovative solutions to improve efficiency and reduce environmental impact. One company at the forefront of this innovation is [company name], a leading global provider of catalysts and advanced chemical solutions. With a commitment to sustainability and technological advancement, [company name] has recently introduced a groundbreaking sulfur tolerant shift catalyst that is set to revolutionize the chemical industry.
The sulfur tolerant shift catalyst, developed by [company name], is a game changer for the industry, providing a powerful solution to the persistent challenge of sulfur impurities in chemical processes. Sulfur impurities, commonly found in natural gas and other feedstocks, can pose significant operational and environmental challenges for chemical manufacturers. Traditional shift catalysts are sensitive to sulfur, leading to frequent catalyst replacement and reduced process efficiency. However, [company name]'s sulfur tolerant shift catalyst is engineered to withstand sulfur contaminants, ensuring consistent performance and prolonged catalyst life.
This breakthrough catalyst is a result of [company name]'s extensive research and development efforts, leveraging years of expertise in catalysis and chemical engineering. The company's state-of-the-art R&D facilities and advanced testing capabilities have enabled the development of a catalyst that offers superior resistance to sulfur poisoning, without compromising on catalytic activity and selectivity. This represents a significant advancement in catalyst technology, addressing a long-standing industry need and unlocking new possibilities for chemical producers worldwide.
The sulfur tolerant shift catalyst is poised to deliver a host of benefits to the chemical industry, enhancing process reliability, flexibility, and economic viability. By minimizing the impact of sulfur impurities, chemical manufacturers can optimize their operations and achieve higher levels of productivity and profitability. Furthermore, the catalyst's enhanced durability reduces the frequency of catalyst replacement, resulting in cost savings and operational efficiency. In addition to these tangible advantages, the use of this catalyst also contributes to environmental sustainability by reducing emissions and minimizing the environmental footprint of chemical processes.
[company name]'s sulfur tolerant shift catalyst has already garnered significant interest and accolades within the industry, positioning the company as a trailblazer in catalyst innovation. With a strong commitment to technological leadership and customer satisfaction, [company name] is dedicated to supporting chemical manufacturers in realizing the full potential of this groundbreaking catalyst. By partnering with [company name], chemical producers can gain access to the latest advancements in catalyst technology, along with comprehensive technical support and expertise to optimize their catalytic processes.
As the chemical industry continues to evolve and face new challenges, [company name] remains steadfast in its commitment to driving innovation and delivering sustainable solutions that create value for its customers. The introduction of the sulfur tolerant shift catalyst underscores the company's vision and capabilities in developing advanced catalysts that address critical industry needs and propel the chemical industry towards a more sustainable and efficient future.
In conclusion, [company name]'s sulfur tolerant shift catalyst represents a significant milestone in catalyst technology, offering a groundbreaking solution to the long-standing challenge of sulfur impurities in chemical processes. With its exceptional resistance to sulfur poisoning and superior performance, this catalyst is set to redefine the standards of catalytic processes in the chemical industry. As [company name] continues to lead the way in catalyst innovation, it sets the stage for a new era of sustainable and efficient chemical production.
Overall, the introduction of this breakthrough catalyst reinforces [company name]'s position as a trusted partner and innovator in the chemical industry, and underscores its unwavering commitment to delivering excellence and sustainability in all aspects of its business.
Company News & Blog
The Impact of Catalyst on Tail Gas during Vanadium-Titanium Magnetite Carbon-Containing Pellet Reduction | E3S Web of Conferences
Vanadium-titanium magnetite, a kind of iron ore, is widely used in the production of steel due to its high iron content and strong magnetism. However, the production process generates tail gas, which contains harmful gases like CO, SO2, NOx, and particulate matter. These pollutants not only harm the environment but also pose serious health risks to workers. Therefore, it is important to mitigate the emissions from the production process of vanadium-titanium magnetite.One effective way to reduce the tail gas emissions is through the use of a catalyst. A catalyst is a substance that speeds up a chemical reaction without being consumed in the process. In the case of vanadium-titanium magnetite production, a catalyst can reduce the amount of pollutants generated during the reduction of carbon-containing pellets.Recently, a research team from a company focused on environmental protection and energy conservation, studied the effect of a catalyst on the tail gas during the reduction of vanadium-titanium magnetite carbon-containing pellets. The researchers used a chemical reactor to simulate the reduction process and then analyzed the tail gas using advanced equipment.The research team found that the use of a catalyst significantly reduced the emissions of CO, SO2, and NOx. The reduction rates of these pollutants were 64.3%, 75.4%, and 31.2%, respectively, compared to the process without a catalyst. This means that by using a catalyst, the production of vanadium-titanium magnetite can be made less environmentally harmful, reducing the impact on the ecosystem and improving the health of workers.Moreover, the researchers found that the catalyst also improved the reduction rate of the carbon-containing pellets. The reduction rate increased from 82% to 92% when using the catalyst, which means that the-quality of the final product also improved. This indicates that the use of a catalyst does not only have environmental benefits but also economic advantages.The catalyst used in the study was a new type of rare earth catalyst developed by the company. It has a high catalytic activity, stability, and selectivity, making it suitable for use in the reduction of vanadium-titanium magnetite carbon-containing pellets. The company plans to promote the use of the catalyst in the production process of vanadium-titanium magnetite, to reduce the environmental impact and improve the efficiency of the process.Overall, the research findings show that the use of a catalyst can significantly reduce the emissions of harmful gases during the production of vanadium-titanium magnetite. This not only benefits the environment and human health but also improves the quality and efficiency of the process. The development of new and effective catalysts is essential for reducing the emissions from industrial processes and achieving sustainable development.
Cutting-Edge Zeolite Catalyst Discovered for Cleaner Energy Production
[News Title]ZSM-22: The Revolutionary Catalyst Boosting Sustainable Production [News Introduction][City Name], [Date] - In an era where environmental sustainability and resource efficiency take center stage, [Company Name], a leading technology company, is set to revolutionize the global industrial sector with its groundbreaking catalyst innovation. The company's latest creation, ZSM-22, has the potential to transform various manufacturing processes, significantly reducing energy consumption and greenhouse gas emissions. With its impressive capabilities and wide-ranging applications, ZSM-22 is poised to become a game-changer for industries striving to achieve sustainable production goals. [Background]For decades, industries have relied heavily on traditional catalysts to drive chemical reactions necessary for various manufacturing processes. However, the widespread usage of these catalysts often comes at a significant cost to the environment. In recent years, as the world grapples with addressing climate change and transitioning towards a greener future, scientists and researchers have been actively seeking alternatives that mitigate the environmental impact without compromising productivity and efficiency.[Company Overview][Company Name], founded in [year], has emerged as a pioneering force in the realm of sustainable manufacturing. The company specializes in developing cutting-edge technologies aimed at enabling a transition to cleaner production methods across industries, ranging from petrochemicals to pharmaceuticals. With a team of dedicated scientists and engineers, [Company Name] has consistently pushed the boundaries of innovation, striving to create solutions that align economic growth with environmental responsibility.[ZSM-22: The Catalyst of the Future]ZSM-22, [Company Name]'s latest breakthrough, is a novel catalyst that promises to revolutionize the way chemicals are produced across diverse industrial sectors. This zeolite-based catalyst exhibits exceptional catalytic performance, high stability, and superior selectivity, making it an ideal choice for numerous industrial processes. The unique characteristics of ZSM-22 offer substantial benefits, including reduced energy consumption, minimized waste, and lowered greenhouse gas emissions.[Application 1: Petrochemical Industry]In the petrochemical industry, where the demand for various chemicals and fuels is immense, ZSM-22 presents a groundbreaking alternative to traditional catalysts. The use of ZSM-22 in catalytic cracking processes can enhance the efficiency of petroleum refining, allowing for the production of valuable chemical compounds and fuels while minimizing unwanted by-products. Consequently, this not only leads to significant cost savings but also reduces the environmental impact associated with these industrial processes.[Application 2: Pharmaceutical Industry]The pharmaceutical industry is known for its energy-intensive production processes. With ZSM-22, however, [Company Name] provides a catalyst solution that enables more sustainable manufacturing of pharmaceutical compounds. By using ZSM-22 in key reactions, pharmaceutical manufacturers can achieve higher yields with reduced energy requirements, ultimately contributing to a greener and more efficient production cycle.[Application 3: Environmental Remediation]Beyond its applications in refining and pharmaceuticals, ZSM-22 possesses immense potential in environmental remediation processes. The catalyst's unique properties make it an invaluable tool for waste management, air purification, and water treatment projects. By leveraging ZSM-22, industries can effectively remove pollutants and harmful substances, ensuring safer and cleaner environments for communities worldwide.[Looking Ahead]As [Company Name] prepares for the commercialization of ZSM-22, there is growing anticipation within the industry regarding its potential to revolutionize sustainable production practices. The groundbreaking catalyst aligns with global efforts to combat climate change and reduce carbon footprints, making it a promising contribution to the ongoing green revolution.In a world that increasingly demands resource efficiency and environmental responsibility, ZSM-22 offers a glimmer of hope for industries seeking sustainable and profitable growth. With continued research and development, [Company Name] aims to inspire a paradigm shift in industrial processes and foster a brighter future for both businesses and the planet.[Closing]As economies strive to strike a balance between meeting consumer demands and preserving the environment, groundbreaking innovations like ZSM-22 pave the way for a more sustainable future. Through the consistent development of cutting-edge technologies, [Company Name] reinforces its commitment to shaping industries that prioritize both productivity and ecological preservation.[Word Count: 800 words]
Discover the latest advancements in Alumina Catalyst technology
Alumina Catalysts: A Game-Changer in Chemical IndustryIn the fast-paced world of chemical manufacturing, efficiency and sustainability are key concerns for companies looking to stay competitive. Enter Alumina Catalysts, a revolutionary new technology that is transforming the way chemical processes are carried out. This innovative catalyst, formulated by a leading chemical company, has been making waves in the industry due to its exceptional performance and environmentally friendly nature.Alumina Catalysts are a type of catalyst used in a wide range of chemical processes, including the production of petrochemicals, polymers, and other specialty chemicals. These catalysts are unique in that they are composed of alumina, a naturally occurring mineral that is renowned for its high surface area and thermal stability. This makes the catalysts highly effective at facilitating chemical reactions and promoting desirable outcomes in various industrial processes.One of the key advantages of Alumina Catalysts is their versatility. These catalysts can be tailored to suit specific chemical reactions, making them ideal for a wide range of applications. Whether it's cracking hydrocarbons in the production of fuels or promoting polymerization in the manufacturing of plastics, Alumina Catalysts have been proven to deliver superior results across the board.Furthermore, the environmental benefits of Alumina Catalysts cannot be overstated. By improving the efficiency of chemical processes, these catalysts help to reduce energy consumption and minimize waste generation. This not only leads to cost savings for companies, but also contributes to a more sustainable and eco-friendly approach to chemical manufacturing.The company behind the development of Alumina Catalysts has a long-standing reputation as a leader in the chemical industry. With decades of experience and a strong commitment to research and development, the company has been at the forefront of creating innovative solutions that address the evolving needs of the market. Their team of experts has worked tirelessly to optimize the performance of Alumina Catalysts, ensuring that they meet the highest standards of quality and reliability.In addition to their technical expertise, the company has also prioritized sustainability as a core value. This is reflected in their dedication to developing products, such as Alumina Catalysts, that contribute to a more sustainable and environmentally conscious chemical industry. By investing in green technologies and promoting responsible practices, the company is making a significant impact on the future of chemical manufacturing.The introduction of Alumina Catalysts has been met with enthusiasm from industry professionals and customers alike. Many companies have already adopted this technology and have reported impressive improvements in their chemical processes. Whether it's enhancing product yields, reducing production costs, or minimizing environmental impact, the benefits of Alumina Catalysts are clear and undeniable.Looking ahead, the prospects for Alumina Catalysts look promising. As the chemical industry continues to evolve and demand for more sustainable solutions grows, the role of these innovative catalysts is expected to become even more prominent. With ongoing research and development efforts, the company is committed to further enhancing the performance and applicability of Alumina Catalysts, solidifying their position as a game-changer in the chemical industry.In conclusion, Alumina Catalysts represent a significant advancement in the field of chemical manufacturing. With their impressive performance, versatility, and eco-friendly attributes, these catalysts have the potential to revolutionize the way chemical processes are carried out. Backed by a reputable and forward-thinking company, Alumina Catalysts are poised to shape a more sustainable and efficient future for the chemical industry.
Breakthrough Methanol Synthesis Catalyst Revolutionizes Production Process
Title: Groundbreaking Methanol Synthesis Catalyst Revolutionizes Energy ProductionIntroduction:In a significant breakthrough for the energy industry, scientists have developed an innovative Methanol Synthesis Catalyst capable of transforming greenhouse gases into methanol with a remarkably high conversion efficiency. This cutting-edge technology is poised to revolutionize global energy production and combat climate change simultaneously. Developed by a prominent materials research company [], this catalyst is a game-changer in the quest for efficient and sustainable energy solutions.Body:1. The Importance of Methanol Synthesis:Methanol, also known as "wood alcohol," is a clean, versatile, and energy-dense liquid fuel that can be used as a substitute for gasoline or diesel. It is also a vital building block for numerous chemicals and materials, including plastics, textiles, pharmaceuticals, and adhesives. However, current methanol production methods largely rely on fossil fuels, exacerbating greenhouse gas emissions. The new Methanol Synthesis Catalyst offers a tangible solution by utilizing greenhouse gases rather than contributing to their accumulation.2. Catalyst Features and Functionality:The newly developed catalyst boasts several key features that differentiate it from existing technologies. Its precise chemical composition maximizes active sites on the catalyst's surface, enhancing the conversion of carbon dioxide (CO2) and hydrogen (H2) into methanol (CH3OH). Additionally, the catalyst operates efficiently at lower temperatures and pressures, resulting in reduced energy consumption.3. Revolutionary Conversion Efficiency:One of the most remarkable attributes of this Methanol Synthesis Catalyst is its outstanding conversion efficiency, setting a new industry benchmark. The catalyst achieves an impressive carbon conversion rate of over 90%, significantly minimizing CO2 emissions during the methanol synthesis process. This game-changing efficiency also translates into a reduction in overall production costs and a more sustainable manufacturing process.4. Contribution to Climate Change Mitigation:By utilizing CO2 as a feedstock for methanol synthesis, the catalyst effectively addresses the pressing environmental issue of greenhouse gas emissions. The chemical conversion of CO2 into methanol not only reduces CO2 concentrations in the atmosphere but also curbs the dependency on finite fossil fuel resources. This environmentally friendly approach aligns with global efforts to mitigate climate change, setting a precedent for cleaner energy methods.5. Economic Advantages and Market Potential:The introduction of this revolutionary catalyst not only benefits the environment but also presents significant economic advantages. As methanol is a highly versatile and widely used chemical, the market demand for it is substantial. The catalyst's high conversion efficiency combined with lower production costs positions it as a viable commercial solution, attracting interest from various sectors such as energy, chemicals, and transportation.6. Collaborative Efforts and Future Prospects:The successful development of the Methanol Synthesis Catalyst represents the culmination of extensive research and collaboration among scientists, engineers, and industry partners. The groundbreaking catalyst has the potential to revolutionize not only methanol synthesis but also the broader field of sustainable energy production. Further research and development are underway to optimize the performance of the catalyst and scale up its production to meet growing market demands.Conclusion:The groundbreaking Methanol Synthesis Catalyst developed by [company name] redefines the possibilities of sustainable energy production while mitigating the detrimental impact of greenhouse gas emissions. With its exceptional conversion efficiency, economic advantages, and valuable contributions to climate change mitigation, this catalyst represents a major step towards a greener and more sustainable future. As further advancements in the field continue to emerge, one can only anticipate the widespread adoption of this innovative technology, transforming the dynamics of energy production on a global scale.
Discover the Unleashed Potential of Alumina Catalysts - A Game-Changer in the News!
Title: Innovations in Catalyst Technology Revolutionize Industrial ProcessesIntroduction:With an unyielding focus on providing cutting-edge solutions to enhance industrial processes, Company XYZ has recently unveiled a revolutionary gamma alumina catalyst. This breakthrough development promises to deliver superior catalytic performance, enabling industries to achieve enhanced productivity, reduced energy consumption, and minimized environmental impact. By introducing this remarkable catalyst, Company XYZ cements its position as a pioneer in the field of catalyst technology.Gamma Alumina Catalyst: A Game-Changer for Industrial ProcessesCompany XYZ's groundbreaking gamma alumina catalyst represents a significant advancement in catalyst technology. Combining cutting-edge research and state-of-the-art manufacturing techniques, this catalyst empowers various industries to optimize their processes while striving for higher efficiency standards.Improved Catalytic Performance:The key highlight of Company XYZ's gamma alumina catalyst lies in its exceptional catalytic performance, which surpasses that of traditional catalysts. This catalyst demonstrates an unprecedented ability to initiate and accelerate chemical reactions, enabling industries to achieve higher conversion rates and improved product quality. Moreover, the gamma alumina catalyst exhibits remarkable stability, ensuring consistent performance over an extended operational lifespan.Reduced Energy Consumption:By utilizing Company XYZ's gamma alumina catalyst, industries can significantly reduce energy consumption during their production processes. The catalyst's enhanced efficiency allows for lower reaction temperatures and shorter reaction times, leading to substantial energy savings. This not only contributes to cost reduction but also aids in environmental sustainability by reducing greenhouse gas emissions associated with excessive energy consumption.Versatility Across Industries:The versatility of Company XYZ's gamma alumina catalyst makes it suitable for a wide range of industries, including petroleum refining, chemical manufacturing, and environmental remediation. Its unique composition and superior functionality enable it to tackle diverse chemical reactions, such as hydrocracking, hydrotreating, and hydrogenation, with exceptional efficiency. This versatility empowers industries to streamline their operations, optimize resource utilization, and stay at the forefront of technological advancements.Environmental Impact:With sustainability at the forefront of global concerns, Company XYZ's gamma alumina catalyst offers a viable solution to minimize environmental impact. This catalyst facilitates the production of cleaner fuels by enabling more efficient removal of impurities from petroleum feedstocks. Additionally, it plays a crucial role in reducing harmful emissions during various chemical manufacturing processes. By adopting this catalyst, industries can contribute to a greener future while adhering to stringent environmental regulations.Research and Development:The development of Company XYZ's gamma alumina catalyst is a result of relentless pursuit and investment in research and development. The company's dedicated team of scientists and engineers has intricately researched catalyst compositions, optimization techniques, and advanced manufacturing processes, ensuring that the catalyst maintains its superior performance across a wide range of operating conditions. Company XYZ's commitment to continuous innovation underscores its dedication to providing state-of-the-art catalyst solutions to meet ever-evolving industry demands.Conclusion:Company XYZ's groundbreaking gamma alumina catalyst ushers in a new era of catalytic performance, enabling industries to enhance productivity, reduce energy consumption, and minimize their environmental footprint. By leveraging this catalyst, industrial processes can achieve heightened efficiency, increased conversion rates, and improved product quality. Company XYZ's relentless commitment to innovation and its profound impact on industrial processes solidify its position as a premier provider of cutting-edge catalyst solutions.
Role of Catalyst in Reducing Tail Gas from Vanadium-Titanium Magnetite with Carbon-Containing Pellets: Study Findings
Tail Gas Hydrogenation Catalyst: What It Is and How It Works in Vanadium-Titanium Magnetite Carbon-Containing Pellet ReductionThe production of iron and steel is one of the biggest sources of industrial pollutants, including greenhouse gases and toxic substances. Thus, it is essential to find ways to reduce these emissions and make the industry more sustainable and environmentally friendly. One of the innovative approaches to achieve this goal is to use tail gas hydrogenation catalysts in the reduction process of vanadium-titanium magnetite carbon-containing pellets. In this blog post, we will explore what tail gas hydrogenation catalysts are, how they work, and their role in the reduction of carbon-containing pellets.What are Tail Gas Hydrogenation Catalysts?Tail gas hydrogenation catalysts are substances that promote the hydrogenation reaction that occurs in the tail gas from the reduction process of iron ore. The tail gas contains hydrogen (H2), carbon monoxide (CO), and other gases that are typically burned off to generate heat or steam. This method is known as the direct reduction of iron (DRI). However, using tail gas hydrogenation catalysts can turn these gases into valuable products that can be used within the production process or sold for commercial purposes.How Do Tail Gas Hydrogenation Catalysts Work?Tail gas hydrogenation catalysts work by promoting the reaction between hydrogen and carbon monoxide in the tail gas, which creates methane (CH4) and water (H2O). This reaction is known as the Fischer-Tropsch reaction, which has been used in industrial applications since the early 1900s. The process occurs in the presence of a catalyst that speeds up the reaction and increases its efficiency and selectivity. The tail gas can also be treated with other catalysts to remove impurities and improve its quality further.Role of Tail Gas Hydrogenation Catalysts in the Reduction of Carbon-Containing PelletsThe use of tail gas hydrogenation catalysts in the reduction of carbon-containing pellets is a promising approach for reducing pollutants and improving overall energy efficiency. When used in conjunction with DRI, the tail gas can be recycled and reused several times. The tail gas is first directed through a scrubber system that removes any impurities, including sulfur compounds, that may damage the catalyst. After that, the tail gas is compressed and sent to the hydrogenation reactor, where the Fischer-Tropsch reaction takes place.The addition of a tail gas hydrogenation catalyst increases the conversion rate of CO and H2 into CH4 and H2O, improving yield, and reducing the amount of waste gas. The methane produced by the reaction is used as a fuel source or further processed into methanol, which is valuable in the chemical industry. Moreover, capturing and using tail gas as a feedstock also reduces the reliance of iron and steel plants on fossil fuels, thereby reducing emissions of greenhouse gases.ConclusionThe use of tail gas hydrogenation catalysts in the reduction of vanadium-titanium magnetite carbon-containing pellets is a promising approach for improving the sustainability of the iron and steel industry. By promoting the hydrogenation reaction in the tail gas, these catalysts increase efficiency and reduce pollutants. The methane produced by the reaction can be further processed and used as a valuable fuel source or commercial product. The use of tail gas as a feedstock also enhances the industry's energy efficiency and reduces the reliance on fossil fuels. Overall, the application of tail gas hydrogenation catalysts is a win-win strategy for the environment and the economy. Keywords: Tail Gas Hydrogenation Catalyst, Fischer-Tropsch Reaction, Carbon-Containing Pellets, Reduction, Sustainability, Iron and Steel Industry.
Innovative Al2o3 Catalyst: Key Role in Chemical reactions
Al2O3 Catalyst Significant in Advancing Green TechnologyIn recent years, the push towards sustainability and environmental consciousness has become a major focus for industries worldwide. In response to this, companies are constantly seeking innovative solutions to reduce emissions and minimize their environmental impact. One company at the forefront of this movement is [Company Name], a leading provider of advanced materials and catalyst solutions.[Company Name] is dedicated to developing cutting-edge technologies that address the global need for cleaner, more sustainable processes. Their expertise lies in the design and production of catalysts, including the highly effective Al2O3 Catalyst, which has proven to be a game-changer in advancing green technology.The Al2O3 Catalyst, also known as alumina catalyst, is a versatile and high-performing material that is widely used in industrial applications to promote chemical reactions. Its unique properties make it an ideal choice for a wide range of catalytic processes, particularly those focused on reducing harmful emissions and improving overall efficiency. With its ability to facilitate various reactions, the Al2O3 Catalyst has become a key component in the development of cleaner and more sustainable industrial processes.One of the key advantages of the Al2O3 Catalyst is its exceptional thermal stability, which enables it to withstand high temperatures and harsh operating conditions without a significant loss of activity. This makes it particularly well-suited for applications in the petrochemical, environmental, and energy sectors where the need for reliable and long-lasting catalysts is paramount. Its robust nature and versatility have made it an essential tool for companies looking to enhance their environmental performance and meet stringent regulatory requirements.[Company Name] has played a pivotal role in the widespread adoption of the Al2O3 Catalyst by leveraging their expertise in materials science and chemical engineering. Through extensive research and development efforts, they have continuously improved the performance and efficiency of the catalyst, enabling their customers to achieve greater sustainability and economic success.In addition to their technical capabilities, [Company Name] distinguishes itself through its commitment to environmental stewardship and corporate responsibility. They have made significant investments in green technologies and sustainable practices, with the Al2O3 Catalyst serving as a prime example of their dedication to advancing environmental sustainability.Moreover, [Company Name] has established strong partnerships with leading organizations and research institutions to further advance the application of the Al2O3 Catalyst in various industries. These collaborations have enhanced the understanding of catalytic processes and opened up new opportunities for utilizing the Al2O3 Catalyst in novel and impactful ways.As the global demand for cleaner and more efficient industrial processes continues to grow, the role of catalysts such as the Al2O3 Catalyst will become increasingly significant. With [Company Name] leading the way in catalytic innovation, the future looks promising for companies seeking to improve their environmental footprint and embrace sustainable technologies.In conclusion, the Al2O3 Catalyst has emerged as a critical enabler of green technology, enabling companies to achieve substantial improvements in their environmental performance. With [Company Name] at the helm of this movement, the widespread adoption of the Al2O3 Catalyst is poised to drive positive change across industries and support the transition towards a more sustainable future.
New Study Reveals Benefits of Alumina Microspheres in Various Applications
Alumina Microsphere - The Revolutionary Material by an Innovative CompanyAlumina microspheres are a revolutionary material that is making waves in various industries due to its exceptional properties and versatile applications. This unique material, developed by an innovative company, is rapidly becoming the material of choice for a wide range of applications, from aerospace and automotive industries to medical and construction sectors.The alumina microspheres, developed by {Company}, are an advanced type of ceramic material that offers high strength, excellent thermal stability, and remarkable resistance to corrosion and wear. These properties make them an ideal choice for applications that require durable and high-performance materials.{Company} is a leading manufacturer of advanced materials and specializes in the development and production of high-performance ceramic materials. The company has a strong focus on innovation and has a team of expert researchers and engineers who are dedicated to pushing the boundaries of material science. Their commitment to quality and innovation has positioned them as a key player in the advanced materials industry.The alumina microspheres developed by {Company} have garnered significant attention due to their unique properties and the wide range of applications they offer. One of the key features of these microspheres is their high strength-to-weight ratio, making them an excellent choice for lightweight structural components in aerospace and automotive applications. Additionally, their exceptional thermal stability makes them suitable for high-temperature applications, such as furnace linings and thermal insulation.In the medical industry, alumina microspheres are being used in advanced medical implants due to their biocompatibility and resistance to wear. The material's inert nature and exceptional mechanical properties make it an excellent choice for orthopedic and dental implants, offering patients a reliable and long-lasting solution.Furthermore, alumina microspheres are finding applications in the construction sector, where their high strength and durability make them an ideal choice for structural reinforcements and protective coatings. Their corrosion resistance and ability to withstand harsh environmental conditions make them a valuable material for infrastructure projects and building facades.One of the key advantages of alumina microspheres is their exceptional chemical and thermal stability, which makes them suitable for a wide range of industrial processes. They are being used in catalyst supports, adsorbents, and ceramic membranes, where their high surface area and uniform particle size distribution provide outstanding performance and efficiency.{Company}'s commitment to innovation and product development has led to the continuous improvement of alumina microspheres, enabling them to meet the evolving needs of various industries. The company's state-of-the-art manufacturing facilities and stringent quality control processes ensure that their alumina microspheres consistently meet the highest industry standards, making them a reliable and trusted choice for customers around the world.In conclusion, alumina microspheres developed by {Company} are revolutionizing the advanced materials industry with their exceptional properties and versatile applications. As the demand for high-performance materials continues to grow, {Company} is well-positioned to lead the way with their innovative approach to material science. With a strong focus on quality, innovation, and customer satisfaction, {Company} is set to continue making a significant impact in the advanced materials industry with their groundbreaking alumina microspheres.
New Zsm-23 Technology Revealed: The Latest Advancement in [Industry or Field]
ZSM-23 is a revolutionary new technology that is set to change the game in the world of manufacturing. This advanced system promises to revolutionize the way products are made, with its cutting-edge features and unique capabilities.ZSM-23 is the brainchild of a highly innovative company that specializes in developing state-of-the-art manufacturing solutions. With a strong focus on research and development, this company has a proven track record of creating groundbreaking technologies that exceed industry standards. Their team of experts is dedicated to pushing the boundaries of what is possible in manufacturing, and ZSM-23 is the latest example of their commitment to excellence.One of the key features of ZSM-23 is its ability to streamline the manufacturing process, resulting in increased efficiency and productivity. This system is equipped with advanced automation technology that minimizes the need for human intervention, thereby reducing the risk of errors and improving overall quality. By automating repetitive tasks and optimizing workflows, ZSM-23 enables manufacturers to produce more goods in less time, without compromising on quality.In addition to its impressive automation capabilities, ZSM-23 also boasts a high level of flexibility. This system can be easily reconfigured to accommodate different production requirements, making it ideal for manufacturers who need to adapt to changing market demands. Whether it's shifting to a new product line or adjusting production volumes, ZSM-23 provides the agility and versatility that businesses need to stay competitive in today's fast-paced economy.Furthermore, ZSM-23 is designed with an emphasis on sustainability and environmental responsibility. This system is engineered to minimize waste and reduce the consumption of resources, making it an eco-friendly choice for manufacturers who are looking to minimize their environmental impact. By optimizing energy usage and reducing material wastage, ZSM-23 helps businesses operate in a more sustainable manner, while also lowering their production costs.The benefits of ZSM-23 are not just limited to the manufacturing process – this system also offers invaluable insights and analytics that can help businesses make data-driven decisions. By collecting and analyzing key performance metrics, ZSM-23 provides manufacturers with valuable information about their operations, allowing them to identify areas for improvement and make informed choices that drive continuous optimization and growth.With its impressive set of features and capabilities, ZSM-23 is poised to be a game-changer in the world of manufacturing. This innovative system has the potential to revolutionize the way products are made, delivering unparalleled efficiency, flexibility, and sustainability. By combining cutting-edge technology with a commitment to excellence, the company behind ZSM-23 is once again setting the standard for what is possible in the world of manufacturing.As the demand for advanced manufacturing solutions continues to grow, ZSM-23 is well-positioned to lead the way, offering businesses a powerful tool to drive their success in today's competitive landscape. With its unmatched capabilities and long list of benefits, ZSM-23 is set to reshape the future of manufacturing and help businesses achieve new heights of efficiency and productivity.
Enhancing Catalyst Performance: A Step towards Efficient Reforming
Reforming Catalyst Technology: Revolutionizing Industrial ProcessesIndustries around the world are constantly striving to improve efficiency, reduce emissions, and enhance productivity. Now, with the emergence of reforming catalyst technology, a groundbreaking solution is at hand. By streamlining and optimizing industrial processes, this cutting-edge catalyst is poised to revolutionize a wide range of industries, from energy production to automotive manufacturing.Traditionally, industrial processes have been hindered by various challenges, such as high energy consumption, extensive environmental impacts, and limited product yields. In an effort to overcome these obstacles, reforming catalyst technology has become a beacon of hope for many. With its ability to enhance reactions, increase selectivity, and minimize undesirable byproducts, this catalyst has the potential to transform entire industries.Reforming catalyst technology works by promoting the desired reactions while suppressing unwanted side reactions. By doing so, it maximizes the product yield and improves the overall efficiency of the process. This catalyst operates at high temperatures, making it suitable for a wide range of applications, including petrochemical production, ammonia synthesis, and hydrogen generation.One key area where reforming catalyst technology is making a significant impact is in the production of clean energy. Green energy sources, such as solar and wind power, are becoming increasingly popular, but their intermittent nature poses challenges for stable energy supply. This is where reforming catalyst technology comes into play. By utilizing this catalyst in conjunction with renewable energy sources, industries can efficiently convert excess electricity into hydrogen, a versatile and clean fuel. Hydrogen can be stored and used when renewable energy generation is low, ensuring a reliable and sustainable energy supply. Moreover, the byproduct of hydrogen production, water, makes it an eco-friendly alternative to traditional fossil fuels.Another sector poised to benefit greatly from reforming catalyst technology is the automotive industry. As the world transitions towards sustainable transportation, the demand for alternative fuels is on the rise. Reforming catalyst technology presents a viable solution by facilitating the production of hydrogen or synthetic fuels, such as methanol or dimethyl ether, from renewable sources. These fuels emit significantly lower carbon emissions compared to conventional gasoline or diesel, making them essential in curbing global warming and improving air quality.In addition to its applications in the energy and transportation sectors, reforming catalyst technology has the potential to transform the production of valuable chemicals. Many industrial processes rely on the production of high-value chemicals, such as aromatics or olefins. However, these processes often generate large amounts of waste and have significant environmental impacts. By integrating reforming catalyst technology, industries can minimize waste, reduce energy consumption, and increase the selectivity of desired products. This not only enhances the economic viability of these processes but also contributes to a more sustainable future.Reforming catalyst technology goes beyond enhancing industrial processes; it also provides economic advantages. With improved efficiency and higher product yields, companies can optimize their operations, reduce costs, and gain a competitive edge in the market. Moreover, as governments worldwide prioritize sustainability and environmental stewardship, industries that adopt reforming catalyst technology can position themselves as leaders in responsible manufacturing.With its potential to revolutionize various industries, reforming catalyst technology is steadily gaining traction. As the world works towards a sustainable future, this catalyst offers a versatile and practical solution for optimizing industrial processes, reducing emissions, and maximizing productivity. By embracing this technology, companies can not only improve their bottom line but also contribute to a cleaner and greener planet.{Company Introduction}In conclusion, reforming catalyst technology has the potential to revolutionize industrial processes across a wide range of sectors. By improving efficiency, reducing emissions, and increasing selectivity, this catalyst offers a viable solution to the challenges faced by industries worldwide. With its applications in clean energy production, alternative fuels, and valuable chemicals, reforming catalyst technology is paving the way towards a more sustainable future. By adopting this innovative technology, companies can not only enhance their operations but also contribute to global efforts in combating climate change and ensuring a greener planet for future generations.