The Latest Breakthrough in Alumina Production Unveiled by Researchers
By:Admin
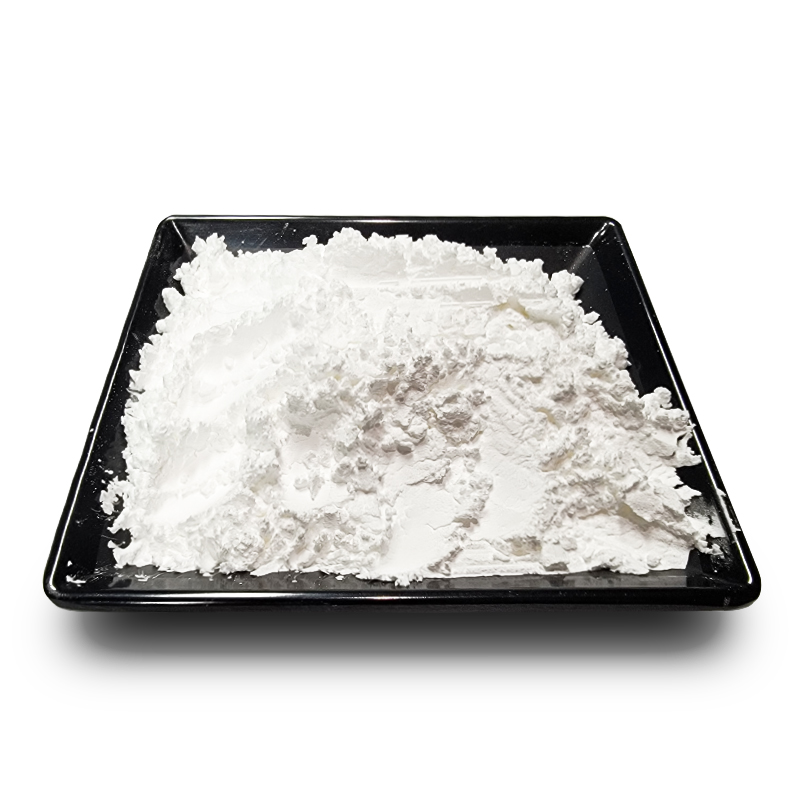
Introduction:
In a breakthrough development, a leading materials research company has successfully engineered a novel alumina-based catalyst called Gamma Alumina. This exceptional catalyst possesses unparalleled chemical and physical properties, making it a game-changer across various industrial applications. Developed with cutting-edge innovation and extensive research, Gamma Alumina offers improved catalytic performance, longevity, and versatility, revolutionizing processes and driving operational efficiency.
Structure and Properties:
Gamma Alumina boasts a remarkable crystalline structure that sets it apart from conventional catalysts. With a high surface area, exceptional porosity, and well-defined pores, it maximizes its catalytic potential by optimizing reactant adsorption and diffusion. This unique structure makes Gamma Alumina highly adaptable for diverse catalytic reactions, ensuring superior performance and selectivity across a wide range of industrial processes.
Applications:
1. Petrochemical Industry:
The petrochemical industry can benefit significantly from the introduction of Gamma Alumina as a catalyst. Its exceptional properties make it an ideal choice for catalytic cracking, which plays a crucial role in the conversion of heavy hydrocarbons into valuable lighter fractions. The catalyst's high thermal stability and superior resistance to coke deposition ensure prolonged usage, reducing downtime and maintenance costs for refineries worldwide.
2. Pharmaceutical Manufacturing:
Gamma Alumina finds extensive application in pharmaceutical manufacturing processes. Its unique structure and surface properties enable it to act as a highly efficient catalyst in several crucial reactions, such as the production of active pharmaceutical ingredients (APIs) and the synthesis of fine chemicals. The catalyst's remarkable performance, coupled with its excellent control over selectivity, enables pharmaceutical manufacturers to enhance reaction yields while reducing waste and increasing purity.
3. Environmental Sector:
The environmental sector greatly benefits from the implementation of Gamma Alumina as a catalyst. It finds applications in catalytic converters, the vital components of vehicle exhaust systems. By increasing the conversion efficiency of harmful gases, such as nitrogen oxides (NOx), Gamma Alumina helps minimize their impact on the environment. Additionally, its stable and long-lasting catalytic performance in volatile environments makes it an excellent choice for air purification systems and wastewater treatment processes.
4. Energy Sector:
In the energy sector, Gamma Alumina plays a pivotal role in enhancing the efficiency of energy storage and conversion systems. This catalyst finds extensive use in fuel cells and electrolyzers, enhancing their performance by facilitating faster and more selective reactions. Gamma Alumina's exceptional stability ensures the longevity and durability of these energy conversion devices, reducing operating costs while promoting sustainable energy usage.
Future Prospects:
The successful development of Gamma Alumina opens doors for further research and applications in various industries. With ongoing advancements in catalyst engineering and material science, it is anticipated that Gamma Alumina will continue to evolve, providing even greater efficiency, selectivity, and durability. The catalyst's potential application in emerging technologies like carbon capture and utilization demonstrates its adaptability and versatility.
Conclusion:
The introduction of Gamma Alumina as an alumina-based catalyst is a significant advancement in industrial catalysis. Its exceptional properties and unique structure position it as a catalyst of choice across multiple industries, including petrochemicals, pharmaceutical manufacturing, environmental protection, and the energy sector. As research and development in catalyst innovation continues, Gamma Alumina sets the foundation for a more sustainable and efficient future in industrial processes.
Company News & Blog
Innovative catalyst technology for sustainable industrial processes
Clariant Catalyst, a leading global company in the field of catalysts and specialty chemicals, has recently made significant advancements in the development of innovative catalytic solutions for a wide range of industrial processes. With a focus on sustainability and efficiency, the company is dedicated to providing high-quality catalysts that enable its customers to achieve their production goals while reducing environmental impact.Founded in [year], Clariant Catalyst has built a strong reputation for delivering cutting-edge solutions that address the evolving needs of various industries, including petrochemicals, refining, and chemical manufacturing. The company's extensive portfolio of catalysts encompasses a diverse array of applications, from hydroprocessing and emissions control to renewable fuel production and polymerization.In recent years, Clariant Catalyst has made substantial investments in research and development to expand its product offerings and enhance the performance of its existing catalysts. Leveraging its state-of-the-art laboratories and technical expertise, the company has continuously pushed the boundaries of innovation, resulting in the introduction of several breakthrough catalyst technologies that deliver superior efficiency and cost-effectiveness.One of Clariant Catalyst's notable achievements is the successful development of a novel catalyst designed to improve the production of renewable fuels from biomass and waste materials. This advancement is aligned with the company's commitment to sustainable solutions, as it enables the conversion of non-traditional feedstocks into high-quality biofuels that can reduce greenhouse gas emissions and contribute to the transition to a low-carbon economy.Additionally, Clariant Catalyst has made significant progress in the optimization of catalysts for emissions control, particularly in the reduction of harmful pollutants from industrial processes and vehicle exhaust systems. By utilizing advanced chemical formulations and engineering techniques, the company has been able to achieve remarkable results in minimizing the environmental impact of various combustion processes, thus supporting global efforts to improve air quality and public health.Furthermore, Clariant Catalyst has expanded its expertise in the area of catalytic technologies for sustainable chemical manufacturing, with a focus on enabling the production of key building blocks for the synthesis of specialty chemicals and polymers. Through the development of highly selective and durable catalysts, the company has empowered its customers to streamline their production processes and enhance the overall efficiency of their operations.In line with its dedication to sustainability, Clariant Catalyst has also been proactive in addressing the challenges associated with the circular economy, offering catalyst solutions that facilitate the recycling and upcycling of plastics and other materials. By enabling the conversion of waste streams into valuable chemical intermediates, the company is actively contributing to the reduction of waste and the promotion of a more circular and sustainable approach to resource utilization.With a global presence and a strong commitment to customer partnerships, Clariant Catalyst has established itself as a trusted and reliable provider of catalyst solutions, serving a diverse customer base that spans across the Americas, Europe, and Asia. The company's collaborative approach and customized technical support have positioned it as a preferred collaborator for businesses seeking to enhance the performance and sustainability of their operations.Looking ahead, Clariant Catalyst remains dedicated to driving innovation and advancing the frontiers of catalytic technology, with a continued focus on delivering value-added solutions that enable its customers to achieve their strategic objectives while minimizing their environmental footprint. By blending its technical expertise with a forward-thinking mindset, the company is poised to play a pivotal role in shaping the future of sustainable catalysis and chemical processing.In conclusion, Clariant Catalyst's relentless pursuit of excellence and sustainability in catalytic solutions has positioned it as a leading force in the industry, driving positive change and value creation for its customers and society as a whole. As the company continues to push the boundaries of innovation and expand its global footprint, it remains committed to making a lasting impact through its cutting-edge catalyst offerings.
Get Quality Activated Alumina for Catalyst Carriers at Low Prices from Professional Manufacturers
New Arsenic Removal Agent - The Solution for Clean Water
Arsenic Removal Agent Successfully Removes Arsenic from Water Supply(Arsenic Removal Agent), a breakthrough technology in removing arsenic from water, has successfully removed dangerous levels of arsenic from a community water supply in a recent trial. This achievement marks a significant step forward in addressing the global issue of arsenic contamination in water sources.The trial was conducted by (company name), a leading provider of innovative water treatment solutions. (Company name) has been at the forefront of developing cutting-edge technologies to address water quality issues, and the success of the arsenic removal trial demonstrates the company’s commitment to providing safe and clean water for communities around the world.Arsenic contamination in water sources is a major public health concern, especially in regions where natural geological factors contribute to high levels of arsenic in the groundwater. Long-term exposure to arsenic can lead to various health problems, including skin lesions, cancer, and cardiovascular diseases. Therefore, the development of effective arsenic removal technologies is crucial for protecting public health.(Arsenic Removal Agent) works by selectively removing arsenic from water, leaving behind clean and safe drinking water. The technology is based on a proprietary adsorption process that captures and immobilizes arsenic particles, effectively reducing their concentration to safe levels. This innovative approach has shown promising results in various water treatment applications, and the recent trial further validates its effectiveness in real-world settings.The successful removal of arsenic from the community water supply is a testament to the capabilities of (Company name) and its commitment to developing sustainable and efficient water treatment solutions. The company’s expertise in water quality management, combined with its dedication to innovation and environmental responsibility, has positioned it as a trusted partner for communities, industries, and governments seeking to address water quality challenges.In addition to its arsenic removal technology, (Company name) offers a comprehensive range of water treatment solutions, including filtration systems, disinfection technologies, and wastewater treatment processes. The company’s holistic approach to water management encompasses the entire water cycle, from source water protection to wastewater recovery, and is guided by the principles of sustainability, efficiency, and social responsibility.(Spokesperson name), (title) of (Company name), commented on the successful trial, stating, “We are thrilled to see our arsenic removal technology deliver positive results in the field. This achievement is a testament to our team’s dedication and expertise in developing innovative solutions to address water quality challenges. We are proud to contribute to the well-being of communities by providing access to clean and safe drinking water.”The next steps for (Company name) include scaling up the deployment of (Arsenic Removal Agent) to address arsenic contamination in water sources globally. The company is actively collaborating with partners and stakeholders to bring this technology to communities that are affected by arsenic contamination, with the goal of making safe drinking water accessible to all.In conclusion, the successful removal of arsenic from the community water supply using (Arsenic Removal Agent) represents a significant milestone in the ongoing effort to ensure access to clean and safe drinking water for all. (Company name)'s dedication to developing innovative water treatment solutions underscores its commitment to environmental stewardship and public health, positioning the company as a leader in the global water quality management industry.
Sulfur Tolerant Shift Catalyst: Key Benefits and Uses
Sulfur Tolerant Shift Catalyst: A Breakthrough in Industrial TechnologyInnovative technology has always been at the forefront of industrial progress, driving advancements in efficiency and sustainability. One such breakthrough is the development of a Sulfur Tolerant Shift Catalyst, a game-changing catalyst that promises to revolutionize the way industrial processes are conducted.The Sulfur Tolerant Shift Catalyst, developed by a leading chemical company, is designed to address the challenges posed by sulfur-containing feedstocks in the production of hydrogen and other important industrial processes. These feedstocks often contain sulfur compounds that can poison conventional shift catalysts, leading to reduced efficiency and increased maintenance costs. The new catalyst, however, is able to withstand the detrimental effects of sulfur, offering a more reliable and cost-effective solution for industrial applications.The company behind this groundbreaking technology is a global leader in the development and manufacturing of catalysts, with a strong focus on innovation and sustainability. With a history of delivering high-performance solutions for diverse industrial processes, the company has established itself as a trusted partner for businesses seeking to enhance their operational efficiency and environmental performance.The Sulfur Tolerant Shift Catalyst represents a significant step forward for the company, showcasing its ability to develop cutting-edge solutions that address the evolving needs of the industry. By enabling the use of sulfur-containing feedstocks without compromising process efficiency, the catalyst opens up new possibilities for businesses looking to optimize their operations while reducing their environmental impact.The development of the Sulfur Tolerant Shift Catalyst is a testament to the company's commitment to research and development, as well as its dedication to providing sustainable solutions for the industry. Through ongoing investment in innovation and collaboration with partners and customers, the company continues to push the boundaries of what is possible in the field of catalysis, driving positive change in the industrial sector.Furthermore, the company's expertise in catalyst manufacturing and process optimization has allowed it to tailor the Sulfur Tolerant Shift Catalyst to meet the specific requirements of different industries and applications. This flexibility makes the catalyst a versatile and adaptable solution, suitable for a wide range of industrial processes where sulfur tolerance is a critical factor.In addition to its technical performance, the Sulfur Tolerant Shift Catalyst also offers environmental benefits by enabling the use of alternative feedstocks that might otherwise be considered unsuitable due to their sulfur content. By minimizing the need for expensive and energy-intensive sulfur removal processes, the catalyst helps to reduce the overall environmental footprint of industrial operations, supporting the transition towards more sustainable and resource-efficient practices.Looking ahead, the company is committed to further advancing the capabilities of the Sulfur Tolerant Shift Catalyst, exploring opportunities to expand its application to new industries and processes. By harnessing the power of innovation and collaboration, the company aims to drive positive change in the industry and contribute to the development of a more sustainable and efficient industrial landscape.As the Sulfur Tolerant Shift Catalyst continues to gain traction in the market, it has the potential to become a game-changer for industrial processes reliant on sulfur-containing feedstocks. By offering a reliable and cost-effective solution for overcoming the challenges of sulfur tolerance, the catalyst represents a significant advancement in industrial technology, with far-reaching implications for the future of the industry.In conclusion, the development of the Sulfur Tolerant Shift Catalyst stands as a testament to the company's commitment to innovation and sustainability, showcasing its ability to deliver high-performance solutions that address the evolving needs of the industry. With its potential to drive positive change and enable more sustainable industrial practices, the catalyst is set to make a lasting impact on the way industrial processes are conducted, creating new opportunities for businesses to enhance their performance and reduce their environmental footprint.
Industry News: Catalyst Company Develops Innovative Environmental Solution
Clariant Catalyst, a leading provider of catalyst solutions for various industries, has recently made significant advancements in the field of catalyst technology. The company has a rich history of innovation and expertise in developing catalysts that help improve the efficiency and sustainability of industrial processes.With a global presence and a strong commitment to research and development, Clariant Catalyst has established itself as a trusted partner for businesses looking to enhance their catalytic processes. The company's broad portfolio of catalysts encompasses a wide range of applications, including environmental protection, energy production, and chemical manufacturing.One of the key areas of focus for Clariant Catalyst is environmental sustainability. The company's catalyst solutions are designed to help reduce emissions and minimize the environmental impact of industrial operations. By optimizing chemical reactions and improving process efficiency, Clariant Catalyst enables its customers to meet stringent environmental regulations and achieve their sustainability goals.In addition to its environmental efforts, Clariant Catalyst also offers catalyst solutions that support the production of clean and renewable energy. The company's expertise in catalytic technology has been instrumental in the development of advanced processes for producing biofuels, hydrogen, and other sustainable energy sources.Moreover, Clariant Catalyst has a strong track record of collaboration with industry partners to develop tailor-made catalyst solutions that address specific challenges and requirements. The company's collaborative approach allows it to gain a deep understanding of its customers' needs and deliver innovative catalyst solutions that drive tangible business value.Furthermore, Clariant Catalyst's commitment to sustainability extends to its own operations. The company continually strives to minimize its environmental footprint and promote sustainable practices throughout its value chain. By investing in environmentally friendly technologies and promoting resource efficiency, Clariant Catalyst is dedicated to being a responsible and sustainable business partner.In line with its dedication to innovation and sustainability, Clariant Catalyst has recently introduced a breakthrough catalyst technology that promises to revolutionize the industry. This new catalyst offers unprecedented performance and efficiency, enabling businesses to achieve significant improvements in their catalytic processes. With its advanced capabilities, the new catalyst is poised to help companies enhance their operational efficiency, reduce costs, and minimize their environmental impact.Clariant Catalyst's latest innovation is a testament to the company's unwavering commitment to pushing the boundaries of catalytic technology. By consistently investing in research and development, Clariant Catalyst remains at the forefront of catalyst innovation, driving positive change across industries and helping businesses navigate the challenges of an ever-evolving market.As Clariant Catalyst continues to lead the way in catalytic technology, the company is well positioned to empower its customers to achieve their sustainability and business objectives. With a proven track record of delivering high-performance catalyst solutions and a strong focus on collaboration and sustainability, Clariant Catalyst stands out as a trusted partner for businesses seeking to enhance their catalytic processes and drive lasting positive change.In conclusion, Clariant Catalyst's ongoing commitment to innovation and sustainability underscores its status as a leading provider of catalyst solutions. With its latest breakthrough in catalyst technology and its dedication to environmental responsibility, Clariant Catalyst is well positioned to continue driving positive change and delivering value to its customers and the broader industry.
Newly Developed Zsm-5 Shows Promising Results for Advanced Materials
ZSM-5 is a zeolite material used in the catalytic cracking of petroleum for the production of gasoline. It is a highly-effective catalyst due to its uniform pore structure, high surface area, and strong acidity. The use of ZSM-5 has enabled the petroleum industry to produce gasoline with higher octane numbers and better fuel efficiency.In recent years, the demand for ZSM-5 has been steadily increasing as the automotive industry continues to grow. As a result, the production and supply of ZSM-5 have become vital for the petrochemical industry. This has led to the development of new and more efficient methods for producing ZSM-5, such as the innovative process developed by {company name}.{Company name} is a leading manufacturer of zeolite materials and has been at the forefront of ZSM-5 production for many years. The company has developed a proprietary method for producing ZSM-5 that is more cost-effective and environmentally friendly than traditional methods. This has allowed {company name} to become a key supplier of ZSM-5 to the petrochemical industry.The unique production method developed by {company name} involves the use of advanced catalyst synthesis technology and precise control of reaction conditions. This results in the production of ZSM-5 with higher purity and improved performance compared to traditional methods. Furthermore, the process developed by {company name} has significantly reduced energy consumption and waste generation, making it a more sustainable option for ZSM-5 production.The success of {company name} in the production of ZSM-5 has not gone unnoticed. The company has received accolades for its innovative production process and has become a trusted supplier to major petrochemical companies around the world. This has helped {company name} to expand its market share and establish itself as a leader in the zeolite materials industry.In addition to ZSM-5, {company name} also manufactures a wide range of other zeolite materials for various applications, including catalytic cracking, adsorption, and ion exchange. The company's expertise in zeolite materials has allowed it to provide tailored solutions to its customers, addressing their specific needs and requirements.Looking ahead, {company name} is committed to further advancing its production technology and expanding its product offerings. The company continues to invest in research and development to improve the performance and cost-effectiveness of its zeolite materials. Additionally, {company name} is exploring new applications for its zeolite materials, seeking to diversify its product portfolio and capture new market opportunities.As the global demand for gasoline and petrochemical products continues to grow, the need for high-quality zeolite materials such as ZSM-5 will remain crucial. With its innovative production methods and extensive expertise, {company name} is well-positioned to meet this demand and continue to be a leading supplier to the petrochemical industry.In conclusion, ZSM-5 is an essential catalyst for the production of high-quality gasoline, and {company name} is at the forefront of its production. With its innovative production methods and commitment to excellence, {company name} is a trusted supplier of zeolite materials to the petrochemical industry, and is poised for continued success in the years to come.
Innovative Catalyst Carrier Spheralite Revolutionizing the Industry
Spheralite, a leading global player in the chemical industry, has recently introduced a groundbreaking catalyst carrier that has the potential to revolutionize the way chemical processes are carried out. The new catalyst carrier, which has been developed after years of dedicated research and development, is expected to significantly enhance the efficiency and effectiveness of various industrial processes.The catalyst carrier, which has been named as SpheraCarrier, is a unique and innovative product that has been designed to improve the performance of catalysts in a wide range of chemical processes. The company has utilized its extensive experience and expertise in the field of chemical engineering to develop this advanced catalyst carrier, which is expected to deliver superior results compared to conventional catalyst carriers.SpheraCarrier is based on a proprietary technology developed by Spheralite, which enables it to offer several key advantages over traditional catalyst carriers. One of the most notable features of SpheraCarrier is its high surface area, which allows it to provide better support to the catalyst and facilitate enhanced catalytic activity. This is expected to result in higher conversion rates and improved selectivity in various chemical processes, leading to greater productivity and cost savings for industrial users.In addition to its high surface area, SpheraCarrier also offers excellent thermal stability and mechanical strength, which makes it suitable for use in various demanding industrial applications. The superior physical and chemical properties of SpheraCarrier have been demonstrated through rigorous testing and validation, which has confirmed its ability to deliver exceptional performance under a wide range of operating conditions.The introduction of SpheraCarrier is expected to have a significant impact on the chemical industry, as it has the potential to improve the efficiency and sustainability of numerous chemical processes. By enhancing the performance of catalysts, SpheraCarrier can help companies optimize their production processes, reduce energy consumption, and minimize waste generation. This can not only lead to cost savings for industrial users, but also contribute to a more environmentally friendly and sustainable approach to chemical manufacturing.SpheraCarrier is suitable for use in a variety of chemical processes, including hydrogenation, oxidation, isomerization, and hydrocracking, among others. Its versatility and superior performance make it a valuable addition to the toolkit of chemical engineers and industrial operators, who are constantly seeking ways to optimize their processes and improve their competitive position in the market.The development and launch of SpheraCarrier is a testament to Spheralite's commitment to innovation and excellence in the field of chemical engineering. The company has a long-standing reputation for delivering high-quality products and solutions to its customers, and the introduction of SpheraCarrier further solidifies its position as a leading provider of advanced chemical technologies.Spheralite has expressed confidence that SpheraCarrier will be well-received by the market, as it addresses a critical need for improved catalyst carriers in the chemical industry. The company is already in the process of engaging with potential customers and partners to demonstrate the capabilities of SpheraCarrier and explore opportunities for collaboration and commercialization.The launch of SpheraCarrier represents a significant milestone for Spheralite and is expected to open up new growth opportunities for the company in the global chemical market. With its advanced technology and proven performance, SpheraCarrier is poised to make a meaningful impact on the industry and drive the next wave of innovation in chemical processing.In conclusion, the introduction of SpheraCarrier by Spheralite marks a major advancement in the field of chemical engineering and is expected to bring about positive changes in the way chemical processes are carried out. With its advanced technology and superior performance, SpheraCarrier is set to become a key enabler of efficiency and sustainability in the chemical industry, helping companies enhance their competitiveness and achieve their business objectives. Spheralite's continued commitment to innovation and excellence ensures that SpheraCarrier will play a pivotal role in shaping the future of chemical manufacturing.
Highly Effective Al2o3 Catalyst for Industrial Applications
Al2o3 Catalyst: A Catalyst Powering Innovation in Chemical ProcessesIn the ever-evolving world of chemical processes and industrial applications, the role of catalysts is crucial. They serve as a catalyst that speeds up chemical reactions without being consumed in the process, leading to increased efficiency and improved production outcomes. Amongst the myriad of catalysts available, Al2o3 catalyst has emerged as a powerhouse, driving innovation in diverse industrial sectors.The Al2o3 catalyst, comprising aluminum oxide as the active component, has become a staple in the chemical and petrochemical industries. Its exceptional catalytic properties make it a go-to choice for various reactions such as catalytic cracking, reforming, and hydroprocessing. With its high surface area, thermal stability, and resistance to harsh operating conditions, the Al2o3 catalyst has proven its mettle in enhancing process performance and product quality.One company that has been at the forefront of harnessing the potential of Al2o3 catalyst is {}. {} is a leading provider of catalyst solutions to the global chemical and refining industries. With a strong emphasis on research and development, the company has been able to leverage the power of Al2o3 catalyst to develop innovative solutions that address the evolving needs of its clients.Established over two decades ago, {} has continually pushed the boundaries of catalyst technology, consistently delivering high-performance catalysts tailored to specific industrial applications. The company's state-of-the-art manufacturing facilities and a dedicated team of researchers and engineers have enabled it to stay ahead of the curve in the highly competitive catalyst market.One of the key strengths of {} lies in its ability to customize Al2o3 catalyst formulations to suit the unique requirements of its clients. Whether it is improving selectivity, enhancing activity, or achieving optimal yields, the company has demonstrated a remarkable track record in developing tailored catalyst solutions that translate into tangible operational and economic benefits for its customers.In addition to its prowess in catalyst development, {} is also committed to sustainability and environmental responsibility. The company has been proactive in developing catalysts that facilitate cleaner and more sustainable industrial processes. By optimizing reaction pathways and minimizing energy consumption, the Al2o3 catalysts from {} are contributing to the industry's efforts to reduce carbon footprint and improve overall environmental performance.The application of Al2o3 catalyst extends across a wide spectrum of industrial processes, from the production of fuels and chemicals to environmental remediation. In the refining industry, the catalyst plays a pivotal role in facilitating the conversion of crude oil into valuable products such as gasoline, diesel, and jet fuel. Its ability to enhance the efficiency of refining processes has made it an indispensable tool for refiners looking to maximize their margins in a competitive market.The chemical industry also benefits significantly from the use of Al2o3 catalyst in various processes such as the production of olefins, aromatics, and specialty chemicals. The catalyst's versatility and reliability have made it a preferred choice for chemical manufacturers aiming to achieve greater process efficiency and product quality.Looking ahead, the future of Al2o3 catalyst seems promising, with continued advancements in catalyst technology and increasing demand for sustainable and high-performance catalyst solutions. As a pioneer in the field, {} is poised to lead the charge in driving innovation and shaping the trajectory of catalyst development.In conclusion, the Al2o3 catalyst has emerged as a game-changer in the realm of chemical processes, offering unparalleled performance and versatility. With {} at the helm of harnessing its potential, the catalyst is set to play a pivotal role in powering the next wave of innovation and progress in the chemical and refining industries.
Discover the Benefits of Residue Hydrogenation Catalysts for Chemical Processing
Residue Hydrogenation Catalyst Catalyst Technology Inc. (CTI) is a leading provider of advanced catalysts and process technologies for a range of industries, including oil and gas, petrochemical, and environmental industries. With a strong focus on innovation and sustainability, CTI has developed a wide range of catalysts that are designed to improve process efficiency, reduce emissions, and lower overall operating costs for its customers.In its latest breakthrough, CTI has developed a highly effective Residue Hydrogenation Catalyst that is set to revolutionize the refining industry. This new catalyst offers superior performance in residue hydroprocessing applications, enabling refiners to produce higher quality products while significantly reducing operating costs.Residue hydroprocessing is a critical step in the refining process, where heavy, high-sulfur residues are converted into lighter, lower-sulfur products. This process is essential for meeting environmental regulations and producing high-quality fuels and petrochemicals. However, traditional catalysts used in residue hydroprocessing often suffer from deactivation and require frequent regeneration, leading to increased downtime and operational expenses.The new Residue Hydrogenation Catalyst from CTI addresses these challenges by delivering outstanding activity, selectivity, and stability. This innovative catalyst is specifically engineered to withstand the harsh operating conditions of residue hydroprocessing, resulting in longer catalyst life and reduced maintenance requirements. As a result, refiners can achieve higher run lengths, lower catalyst consumption, and improved product yields.CTI’s Residue Hydrogenation Catalyst also offers superior sulfur and nitrogen removal capabilities, resulting in cleaner products and compliance with stringent environmental regulations. Additionally, the catalyst’s high conversion efficiency allows refiners to maximize their process yields and optimize their production economics."We are excited to introduce our latest Residue Hydrogenation Catalyst to the market," said Dr. Michael Chen, Chief Technology Officer at CTI. "This innovative catalyst represents a significant advancement in residue hydroprocessing technology, and we believe it will make a substantial impact on our customers' bottom line."In addition to its exceptional performance, CTI’s Residue Hydrogenation Catalyst is also designed to be compatible with existing process equipment, making it easy for refiners to adopt the new catalyst without major modifications to their facilities. This seamless integration ensures a smooth transition and minimizes downtime during catalyst replacement.CTI’s dedication to sustainability is evident in the development of this new catalyst, which is engineered to maximize resource utilization and minimize waste generation. By enabling refiners to produce higher quality, cleaner products with fewer resources, CTI’s Residue Hydrogenation Catalyst contributes to the industry’s efforts to reduce environmental impact and promote sustainable practices.With its proven track record of delivering innovative, high-performance catalysts, CTI is well-positioned to lead the market in residue hydroprocessing technology. The company’s extensive expertise in catalyst design, testing, and optimization, combined with its strong commitment to customer satisfaction, makes CTI a trusted partner for refiners seeking to improve their operations and stay ahead of the competition.As the demand for cleaner, higher-quality fuels and petrochemicals continues to grow, CTI’s Residue Hydrogenation Catalyst offers a compelling solution for refiners looking to enhance their performance and achieve their sustainability goals. With its unmatched performance, stability, and environmental benefits, this new catalyst is set to become a game-changer in the refining industry, solidifying CTI’s position as a leader in advanced catalyst technologies.
Mechanistic Insights into DME Conversion over ZSM-5 Catalysts
and Dimethyl Ether (DME)ZSM-5 catalysts play a significant role in the conversion of dimethyl ether (DME) to olefins. This reaction is an important step in the production of valuable chemical compounds. However, the mechanism of this transformation has been elusive due to the complex nature of the reaction. In a recent study, researchers used temperature-programmed surface reaction experiments and microkinetic modelling to decouple the rates of adsorption, desorption, and surface reaction of DME over fresh and working ZSM-5 catalysts with different Si/Al ratios.The study yielded important insights into the reaction mechanism. The researchers discovered that propylene is the major olefin formed during the transformation of DME. They also observed site-specific scaling relations between the activation energies of DME desorption and barriers to the formation of methoxymethyl and methyl propenyl ether. Six ensembles of sites were observed, with a maximum of three adsorption/desorption sites and three adsorption/desorption/reaction sites.Interestingly, the researchers found that barriers were generally higher for working catalysts than fresh catalysts. This could have implications for industrial processes that use ZSM-5 catalysts.The study’s results were obtained by simulating transient reactor performance through the solving of coupled 1D nonlinear partial differential equations. This accounted for elementary steps during the induction period, based on the methoxymethyl mechanism on the zeolite catalyst, and axial dispersion and convection in the reactor. The activation energies of propylene formation were found to be approximately 200 kJ mol1, which corroborated direct mechanistic proposals.Overall, this study provides valuable mechanistic insights into the conversion of DME over ZSM-5 catalysts. The researchers’ use of temperature-programmed surface reaction experiments and microkinetic modelling allowed for decoupling the complex rates of the reaction, providing important information about site-specific mechanisms. This information may prove useful for developing more efficient and effective industrial processes that utilize ZSM-5 catalysts.In conclusion, the study underscores the importance of understanding the mechanistic details of catalytic reactions. By using advanced experimental and modelling techniques, we can gain insights that will allow for the development of more efficient and sustainable industrial processes.