Discover the benefits of using a residue hydrogenation catalyst
By:Admin
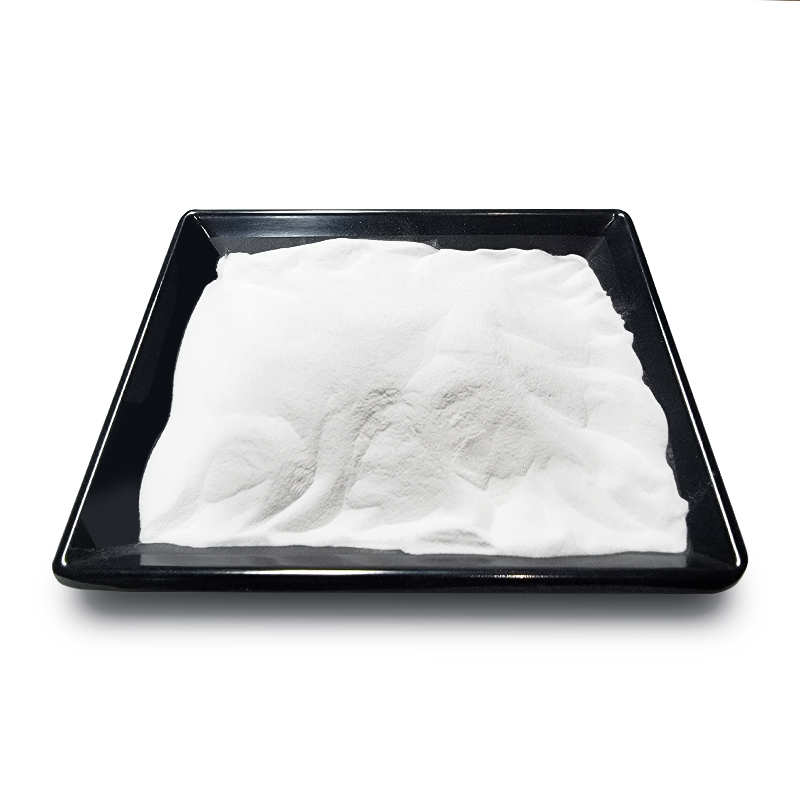
Leading Chemical Company Unveils Groundbreaking Solution for Oil Refineries
[City], [State] - Chemical Giant, a renowned global leader in the field of catalysts and chemical solutions, has introduced a groundbreaking Residue Hydrogenation Catalyst. This cutting-edge catalyst, developed after years of research and innovation, promises to revolutionize the oil refining process, allowing for enhanced efficiency and improved product quality.
With an ever-growing global demand for high-quality petroleum products, oil refineries are constantly seeking innovative solutions to maximize production while minimizing costs. Traditional refining processes struggle with the challenge of converting residues, particularly heavy ones produced during crude oil distillation, into valuable products. Residue Hydrogenation Catalysts have proven to be a game-changer in this regard.
Chemical Giant's newly launched catalyst offers a versatile and efficient solution that converts challenging residues into high-value products such as gasoline, diesel, and other petrochemicals. This breakthrough development holds the potential to transform oil refining operations by increasing profitability and reducing the environmental impact of the refining process.
The Residue Hydrogenation Catalyst is specifically designed to tackle the challenges associated with heavy residues, eliminating impurities and enhancing the quality of the end product. It enables refineries to extract maximum value from their crude oil while complying with stringent environmental regulations.
"Our team of dedicated scientists and engineers has worked tirelessly to create this remarkable catalyst that addresses the longstanding issues faced by oil refineries. We are excited to unveil this breakthrough innovation that will reshape the industry," said [Spokesperson], Chief Technology Officer at Chemical Giant.
The newly introduced catalyst combines advanced technology with sustainable practices, aligning with the company's commitment to environmental stewardship. It allows refineries to achieve significant reductions in carbon dioxide emissions and other harmful pollutants, fostering a cleaner and greener future for the industry.
Chemical Giant has built a solid reputation over the years for its cutting-edge catalyst solutions, serving a wide range of industries. The company's extensive portfolio includes catalysts for various applications, including refining, petrochemicals, and environmental solutions. Their expertise in catalysis, combined with a customer-centric approach, positions them as the catalyst provider of choice for many global oil refineries.
"We believe that by introducing this Residue Hydrogenation Catalyst, we are not only enabling refineries to optimize their operations but also contributing to the global transition towards a more sustainable future. Our commitment to innovation and sustainability continues to drive us forward," added [Spokesperson].
Before the introduction of Chemical Giant's revolutionary catalyst, refineries faced challenges in converting heavy residues, often leading to production bottlenecks and inefficiencies. The Residue Hydrogenation Catalyst resolves these issues, enabling refineries to unlock the full potential of their feedstocks, enhance yields, and boost profitability.
Chemical Giant's Residue Hydrogenation Catalyst has already garnered significant attention from oil refineries worldwide, with several pilot projects underway. The catalyst's impressive performance in laboratory tests and initial trials has generated excitement within the industry, with expectations high for its widespread adoption.
As the global demand for petroleum products continues to rise, the oil refining industry must adapt to evolving market needs. With Chemical Giant's Residue Hydrogenation Catalyst, refineries gain a powerful tool to enhance their operations, maximize profitability, and contribute to a sustainable and cleaner energy future.
About Chemical Giant:
Chemical Giant is a global leader in catalyst solutions and chemical technologies. With a rich history spanning several decades, the company has consistently delivered innovative solutions to various industries, including oil refining, petrochemicals, and environmental solutions. Chemical Giant's commitment to sustainability and customer satisfaction has established them as a trusted and preferred partner for clients worldwide.
For media inquiries, please contact:
[Media Contact]
[Email]
[Phone number]
Company News & Blog
Sulfur Tolerant Shift Catalyst: The Key to Improved Air Quality
Sulfur Tolerant Shift Catalyst Technology: A Game-changer in the Petroleum IndustryThe petroleum industry plays a critical role in meeting the growing energy needs of the world. As the global demand for petroleum products continues to rise, the industry is constantly seeking innovative technologies to enhance the efficiency of production processes and reduce environmental impact. One such groundbreaking technology is the Sulfur Tolerant Shift Catalyst, developed by a leading chemical engineering company.The Sulfur Tolerant Shift Catalyst is a catalyst used in the production of hydrogen through the water-gas shift reaction. This reaction is a key step in the production of hydrogen from natural gas or other hydrocarbons. Traditionally, catalysts used in this process are highly sensitive to sulfur compounds, which can deactivate the catalyst and reduce its efficiency over time. However, the Sulfur Tolerant Shift Catalyst has been engineered to withstand the presence of sulfur, thereby offering significant advantages in terms of longevity and performance.This innovative catalyst technology has the potential to revolutionize the way hydrogen is produced, offering a more robust and cost-effective solution for the petroleum industry. The company behind this groundbreaking technology has a strong track record of developing high-performance catalysts and chemical products for various industrial applications. With a team of experienced chemists, engineers, and researchers, the company is dedicated to pushing the boundaries of chemical innovation and addressing the evolving needs of the industry.The Sulfur Tolerant Shift Catalyst has undergone rigorous testing and validation to demonstrate its superior performance in real-world operating conditions. The catalyst has shown remarkable resistance to sulfur poisoning, maintaining its activity and selectivity over extended periods of operation. This breakthrough technology not only offers operational benefits such as increased catalyst life and reduced maintenance costs, but also contributes to a more sustainable and environmentally friendly production process.In addition to its technical prowess, the company is committed to providing exceptional customer support and value-added services. With a global network of technical experts and customer service professionals, the company offers comprehensive support to ensure the successful implementation and ongoing optimization of its catalyst products. This customer-centric approach has earned the company a reputation for reliability and excellence, further solidifying its position as a trusted partner in the petroleum industry.The Sulfur Tolerant Shift Catalyst technology is set to have a profound impact on the petroleum industry, offering a game-changing solution to the challenges associated with hydrogen production. As the industry continues to prioritize efficiency, cost-effectiveness, and environmental responsibility, this innovative catalyst technology presents a compelling value proposition for producers and refiners around the world. With its cutting-edge capabilities and unwavering commitment to customer satisfaction, the company is poised to lead the way in shaping the future of hydrogen production and advancing the global energy landscape.In conclusion, the Sulfur Tolerant Shift Catalyst technology represents a significant advancement in catalyst innovation, with the potential to revolutionize the petroleum industry. Backed by a company with a strong legacy of excellence and a customer-centric approach, this groundbreaking technology is poised to set new standards for performance, sustainability, and operational efficiency. As the industry embraces the need for cleaner and more efficient energy solutions, the Sulfur Tolerant Shift Catalyst stands out as a true game-changer that will shape the future of hydrogen production and propel the industry towards a more sustainable and prosperous future.
How Alumina Carriers Revolutionize the Transport Industry
[Company Name] Revolutionizes Aluminum Transportation with Game-Changing Alumina Carrier[City], [Date] - In a groundbreaking development, [Company Name], a leading innovator in the transportation industry, unveiled its latest creation - the game-changing Alumina Carrier. This state-of-the-art transportation solution is set to redefine the aluminum logistics landscape, offering unmatched efficiency, sustainability, and reliability.With the global demand for aluminum surging, traditional transportation methods have struggled to keep up. The inefficiencies in current supply chain processes have resulted in increased costs, prolonged delivery times, and environmental concerns. Recognizing these challenges, [Company Name] has invested significant resources in research and development to develop a sustainable and streamlined transportation solution.The Alumina Carrier, designed to optimize the transportation of alumina - the primary component of aluminum production - promises to revolutionize the industry. By integrating cutting-edge technology and innovative design, [Company Name] has developed a transport vessel that addresses the key pain points faced by the industry.One of the primary advantages of the Alumina Carrier is its increased load capacity. By leveraging advanced engineering techniques, [Company Name] has managed to design a vessel that can carry significantly larger quantities of alumina. This not only translates into reduced transportation costs for manufacturers but also results in fewer trips required for delivery, thereby minimizing the carbon footprint associated with transportation.Moreover, the Alumina Carrier is equipped with state-of-the-art tracking and monitoring systems. This real-time data collection enables manufacturers to have complete visibility over their shipments, ensuring optimal control and management of their inventory. By leveraging this technology, [Company Name] aims to enhance supply chain efficiency and empower manufacturers to make informed decisions by accessing critical shipment information.Furthermore, [Company Name] has prioritized sustainability in the design and construction of the Alumina Carrier. In an industry that has long faced criticism for its environmental impact, [Company Name] has taken proactive steps to ensure the vessel adheres to strict eco-friendly standards. The Alumina Carrier boasts an energy-efficient propulsion system, reducing fuel consumption and emissions. Additionally, the vessel is equipped with advanced waste treatment systems to minimize its impact on marine ecosystems.To ensure the successful deployment and scalability of the Alumina Carrier, [Company Name] has collaborated with leading shipping companies and aluminum manufacturers around the world. Preliminary tests and trials have already demonstrated the immense potential of this groundbreaking transportation solution, with manufacturers reporting significant cost savings and improved efficiency.Industry experts have praised [Company Name] for its bold innovation and commitment to revolutionizing the aluminum transportation landscape. The Alumina Carrier's potential to streamline supply chain processes, reduce costs, and minimize environmental impact positions it as a game-changer in the industry.Looking ahead, [Company Name] plans to continue expanding its reach by partnering with additional manufacturers and shipping companies to integrate the Alumina Carrier into their operations. By doing so, the company aims to establish a global network of sustainable aluminum transportation, ensuring a more efficient and environmentally conscious future for the industry.In conclusion, [Company Name]'s Alumina Carrier is set to transform the aluminum transportation industry. With its increased load capacity, real-time tracking capabilities, and dedication to sustainability, this innovation represents a new era in efficient and eco-friendly supply chain management. As aluminum demand continues to rise, the Alumina Carrier offers a solution that not only meets the growing needs of the industry but also sets a new standard for transportation efficiency and sustainability.
Newly Discovered ZSM-22: What You Need to Know
ZSM-22 Zeolite Revolutionizes the Energy IndustryZeolites are crystalline aluminosilicate minerals that are widely used for their unique properties in many industrial applications. One particular type of zeolite, ZSM-22, has been making waves in the energy industry due to its superior catalytic properties. This breakthrough has the potential to revolutionize the production of biofuels and petrochemicals, leading to more sustainable and efficient energy solutions.ZSM-22 zeolite is a highly porous material with a unique structure that allows it to act as a catalyst in chemical reactions. Its large surface area and uniform pore structure make it an excellent candidate for catalyzing the conversion of biomass and other renewable feedstocks into valuable fuels and chemicals. This includes the production of biofuels such as ethanol and biodiesel, as well as the synthesis of high-value intermediates for the petrochemical industry.In recent years, the demand for sustainable energy sources has been on the rise, driven by concerns over climate change and the depletion of fossil fuel reserves. As a result, there has been a growing interest in the development of alternative, renewable energy solutions. ZSM-22 zeolite offers a promising avenue for addressing these challenges by enabling more efficient and environmentally friendly processes for the production of biofuels and other renewable products.The unique properties of ZSM-22 zeolite have been leveraged by a leading company in the zeolite industry, {Company Name}, to develop innovative catalytic solutions for the energy sector. With a strong focus on research and development, {Company Name} has been at the forefront of advancing the application of zeolites in various industrial processes. The company's expertise in zeolite synthesis and characterization has played a crucial role in unlocking the potential of ZSM-22 for energy-related applications.Through extensive research and collaboration with academic institutions and industry partners, {Company Name} has successfully developed novel catalytic materials based on ZSM-22 zeolite that have shown remarkable performance in the conversion of renewable feedstocks into biofuels and petrochemicals. These advancements have the potential to significantly impact the energy industry by enabling more sustainable and cost-effective production processes.The benefits of ZSM-22 zeolite in the energy industry are far-reaching. By improving the efficiency of biofuel production, this innovative technology can help reduce the reliance on fossil fuels and mitigate greenhouse gas emissions. Furthermore, the use of renewable feedstocks in conjunction with ZSM-22 catalysts can contribute to the development of a more circular and sustainable economy.In addition to biofuels, ZSM-22 zeolite can also be used in the production of high-value chemicals and intermediates that are essential for the petrochemical industry. By facilitating the conversion of renewable feedstocks into these valuable products, ZSM-22 zeolite offers a versatile and environmentally friendly solution for meeting the growing demand for sustainable chemicals.The impact of ZSM-22 zeolite on the energy industry is poised to be significant, and {Company Name} is committed to driving the adoption of this breakthrough technology. Through ongoing research and innovation, the company aims to further optimize the performance of ZSM-22 catalysts and expand their application in energy-related processes. With a strong track record in developing cutting-edge zeolite materials, {Company Name} is well-positioned to lead the way in bringing ZSM-22 zeolite to the forefront of the energy industry.As the world continues to seek more sustainable and efficient energy solutions, the emergence of ZSM-22 zeolite as a catalyst for biofuel and petrochemical production represents a major milestone in the quest for a greener future. With the expertise and dedication of companies like {Company Name}, the potential of ZSM-22 zeolite to transform the energy industry is within reach, offering a promising path towards a more sustainable and prosperous tomorrow.
Innovative Catalyst Carrier Spheralite Revolutionizing the Industry
Spheralite, a leading global player in the chemical industry, has recently introduced a groundbreaking catalyst carrier that has the potential to revolutionize the way chemical processes are carried out. The new catalyst carrier, which has been developed after years of dedicated research and development, is expected to significantly enhance the efficiency and effectiveness of various industrial processes.The catalyst carrier, which has been named as SpheraCarrier, is a unique and innovative product that has been designed to improve the performance of catalysts in a wide range of chemical processes. The company has utilized its extensive experience and expertise in the field of chemical engineering to develop this advanced catalyst carrier, which is expected to deliver superior results compared to conventional catalyst carriers.SpheraCarrier is based on a proprietary technology developed by Spheralite, which enables it to offer several key advantages over traditional catalyst carriers. One of the most notable features of SpheraCarrier is its high surface area, which allows it to provide better support to the catalyst and facilitate enhanced catalytic activity. This is expected to result in higher conversion rates and improved selectivity in various chemical processes, leading to greater productivity and cost savings for industrial users.In addition to its high surface area, SpheraCarrier also offers excellent thermal stability and mechanical strength, which makes it suitable for use in various demanding industrial applications. The superior physical and chemical properties of SpheraCarrier have been demonstrated through rigorous testing and validation, which has confirmed its ability to deliver exceptional performance under a wide range of operating conditions.The introduction of SpheraCarrier is expected to have a significant impact on the chemical industry, as it has the potential to improve the efficiency and sustainability of numerous chemical processes. By enhancing the performance of catalysts, SpheraCarrier can help companies optimize their production processes, reduce energy consumption, and minimize waste generation. This can not only lead to cost savings for industrial users, but also contribute to a more environmentally friendly and sustainable approach to chemical manufacturing.SpheraCarrier is suitable for use in a variety of chemical processes, including hydrogenation, oxidation, isomerization, and hydrocracking, among others. Its versatility and superior performance make it a valuable addition to the toolkit of chemical engineers and industrial operators, who are constantly seeking ways to optimize their processes and improve their competitive position in the market.The development and launch of SpheraCarrier is a testament to Spheralite's commitment to innovation and excellence in the field of chemical engineering. The company has a long-standing reputation for delivering high-quality products and solutions to its customers, and the introduction of SpheraCarrier further solidifies its position as a leading provider of advanced chemical technologies.Spheralite has expressed confidence that SpheraCarrier will be well-received by the market, as it addresses a critical need for improved catalyst carriers in the chemical industry. The company is already in the process of engaging with potential customers and partners to demonstrate the capabilities of SpheraCarrier and explore opportunities for collaboration and commercialization.The launch of SpheraCarrier represents a significant milestone for Spheralite and is expected to open up new growth opportunities for the company in the global chemical market. With its advanced technology and proven performance, SpheraCarrier is poised to make a meaningful impact on the industry and drive the next wave of innovation in chemical processing.In conclusion, the introduction of SpheraCarrier by Spheralite marks a major advancement in the field of chemical engineering and is expected to bring about positive changes in the way chemical processes are carried out. With its advanced technology and superior performance, SpheraCarrier is set to become a key enabler of efficiency and sustainability in the chemical industry, helping companies enhance their competitiveness and achieve their business objectives. Spheralite's continued commitment to innovation and excellence ensures that SpheraCarrier will play a pivotal role in shaping the future of chemical manufacturing.
Unlocking the Future of Hydrofining Catalysts: A Comprehensive Overview
article about the benefits and impact of hydrofining catalyst in the oil refining industry.Hydrofining Catalyst: Enhancing the Efficiency of Oil RefiningIn the field of oil refining, hydrofining catalysts have played a significant role in enhancing process efficiency and the quality of refined products. These catalysts are known for their ability to remove undesirable contaminants and impurities from crude oil, making it suitable for further processing into a range of refined products. While there are several types of hydrofining catalysts available in the market, one brand that has gained considerable recognition for its superior quality and performance is [Brand Name].Established in [Year] with a vision to provide innovative and sustainable solutions to the oil and gas industry, [Brand Name] has become a leading name in the field of hydrofining catalysts and related technologies. With a highly skilled team of scientists and engineers, the company is focused on developing proprietary catalyst formulations that can meet the evolving needs of the industry and offer consistent and reliable performance.One of the major benefits of [Brand Name] hydrofining catalyst is its ability to effectively remove sulfur and nitrogen compounds from crude oil. These compounds are known to have adverse environmental impacts and can also lead to corrosion and fouling of equipment in the refining process. By using [Brand Name] catalysts, refineries can comply with increasingly stringent environmental regulations and also reduce maintenance costs.Another notable feature of [Brand Name] catalysts is their high activity and selectivity, which enables faster and more efficient processing of crude oil. This translates into higher throughput and reduced operating costs for refineries. In addition, [Brand Name] catalysts have also demonstrated superior stability and longevity compared to traditional catalysts, which translates into longer cycle times and reduced catalyst replacement costs.Moreover, [Brand Name] hydrofining catalysts are designed to offer superior performance in a range of process conditions, including high hydrogen partial pressures and high temperatures. This makes them suitable for a variety of refinery applications, including hydrotreating, hydrocracking, and other downstream processes.The impact of [Brand Name] catalysts can be seen in several refineries worldwide, where their use has resulted in significant improvements in process efficiency and product quality. One such example is the case of a large refinery in Asia, where [Brand Name] catalysts were used for the first time in a hydrocracking unit. The results were remarkable, with a 20% increase in diesel yield, a 35% reduction in sulfur content, and a 28% reduction in nitrogen content. Additionally, the plant also achieved a 45% reduction in catalyst consumption, leading to substantial cost savings.Another notable example is the case of a European refinery, where [Brand Name] catalysts were used in a hydrotreating unit. The results showed a 25% reduction in sulfur content, 18% improvement in diesel yield, and 12% improvement in liquid yield. Furthermore, the plant also achieved a 10% reduction in energy consumption, leading to substantial savings in operating costs.Overall, [Brand Name] hydrofining catalysts have become a preferred choice among refineries worldwide, thanks to their exceptional performance and proven results. With the world's energy demand projected to grow in the coming years, the role of catalysts in enhancing the efficiency and sustainability of oil refining will become even more critical. As a leading provider of hydrofining catalysts, [Brand Name] is well-positioned to meet this demand and continue driving innovation and performance in the industry.
Significant Discovery Made in Research on Gamma Alumina
Gamma Alumina, a key material in the production of catalysts, has become a major player in the chemical industry. With its high surface area and pore volume, Gamma Alumina is well-suited for various applications such as oil refining, petrochemicals, and environmental protection. The material’s superior properties make it an indispensable component for catalytic converters and other crucial processes in the chemical industry.To meet the increasing demand for Gamma Alumina, leading chemical company {Company Name} has positioned itself as a reliable supplier and manufacturer of this essential material. The company has established itself as a trusted partner to numerous industries, offering a wide range of high-quality products and solutions tailored to meet their specific needs.{Company Name} prides itself on its state-of-the-art production facilities and cutting-edge technology, allowing for the efficient and cost-effective manufacturing of Gamma Alumina. With a focus on innovation and sustainability, the company is committed to providing environmentally-friendly solutions that adhere to the highest industry standards.In addition to its manufacturing capabilities, {Company Name} boasts an experienced team of experts who are dedicated to delivering exceptional customer service and technical support. The company’s commitment to excellence has earned it a sterling reputation in the industry, attracting a loyal customer base and establishing long-term partnerships with leading players in the chemical sector.One of the key reasons for the increasing demand for Gamma Alumina is its pivotal role in environmental protection. The material is widely used in catalytic converters, which are instrumental in reducing harmful emissions from vehicles and industrial processes. As environmental regulations continue to tighten around the world, the importance of Gamma Alumina in mitigating pollution and improving air quality cannot be overstated.{Company Name}’s Gamma Alumina products have been specifically designed to meet the stringent requirements of environmental protection applications. The material’s high surface area and pore volume enable it to effectively catalyze chemical reactions that convert harmful pollutants into less harmful substances, thereby contributing to a cleaner and healthier environment.Moreover, Gamma Alumina’s versatility extends to the oil refining and petrochemical industries, where it plays a crucial role in catalyzing various processes such as hydrocracking, isomerization, and reforming. Its exceptional thermal stability, mechanical strength, and resistance to abrasion make it an ideal choice for these demanding applications, ensuring optimal performance and efficiency in chemical processes.{Company Name}’s commitment to quality, reliability, and sustainability has positioned it as a leading supplier of Gamma Alumina for a wide range of industries. The company’s dedication to continuous improvement and innovation has enabled it to stay at the forefront of the market, offering cutting-edge solutions that meet the evolving needs of its customers.As the demand for Gamma Alumina continues to grow, {Company Name} remains steadfast in its mission to provide superior products and services that drive the success of its customers and contribute to a more sustainable future. With a strong focus on quality, innovation, and customer satisfaction, the company is well-equipped to lead the way in the production and supply of Gamma Alumina for the global chemical industry.
Sulfur Recovery Catalyst: Latest Developments and News
Claus Sulfur Recovery Catalyst is a crucial component in the oil and gas industry, as it plays a significant role in the process of recovering sulfur from hydrogen sulfide gas. This catalyst is essential for ensuring environmental compliance and maintaining operational efficiency in gas processing facilities. The company {} is a leading manufacturer and supplier of Claus Sulfur Recovery Catalyst, with a strong reputation for providing high-quality products and excellent customer service.With a focus on innovation and sustainability, {} has been at the forefront of developing advanced catalyst technologies for sulfur recovery applications. The company's Claus Sulfur Recovery Catalyst is designed to maximize sulfur recovery efficiency while minimizing operating costs and environmental impact. {}'s catalysts are tailored to meet the specific requirements of each customer, ensuring optimal performance and reliability in a wide range of operating conditions.In addition to its cutting-edge catalyst solutions, {} offers technical support and consulting services to help customers optimize their sulfur recovery processes. The company's team of experienced professionals works closely with clients to understand their unique challenges and develop customized solutions that address their specific needs. With a commitment to innovation and continuous improvement, {} is dedicated to helping its customers achieve long-term success and sustainability in their operations.As environmental regulations continue to tighten, sulfur recovery efficiency has become a top priority for gas processing facilities around the world. {}'s Claus Sulfur Recovery Catalyst is designed to help customers meet and exceed regulatory requirements, ensuring compliance with emissions standards and minimizing environmental impact. By utilizing {}'s advanced catalyst technology, customers can achieve higher sulfur recovery rates, reduce sulfur dioxide emissions, and operate their facilities in an environmentally responsible manner.With a global presence and a strong commitment to customer satisfaction, {} has established itself as a trusted partner for sulfur recovery catalyst solutions. The company's extensive network of sales and technical support professionals enables it to deliver exceptional service and support to customers in every corner of the world. Whether it's providing on-site troubleshooting and optimization support or delivering catalyst products in a timely manner, {} is dedicated to meeting the needs of its customers and helping them succeed in their operations.In conclusion, {} is a leading provider of Claus Sulfur Recovery Catalyst, offering innovative solutions and exceptional customer service to the oil and gas industry. With a focus on sustainability and environmental compliance, the company is helping customers around the world optimize their sulfur recovery processes and achieve long-term success. As the demand for sulfur recovery efficiency continues to grow, {} remains committed to driving innovation and delivering value to its customers in the global market.
High Quality Alumina for Various Industrial Applications
Gamma Alumina, a key product in the company’s portfolio, has established itself as a leading material in the industry. With its exceptional properties and wide range of applications, Gamma Alumina continues to be a vital component in various industrial processes.The company, a global leader in material science, has been at the forefront of innovation and development in the field of alumina products. With a strong focus on research and development, the company has continuously pushed the boundaries of what is possible with this versatile material. The result is a range of high-quality products that cater to diverse industries and applications.Gamma Alumina, in particular, has garnered attention for its impressive performance characteristics. Its high surface area, uniform particle size, and excellent thermal stability make it an ideal choice for many applications. From catalyst supports to adsorbents, Gamma Alumina has proven to be an essential material for numerous chemical processes.One of the key features of Gamma Alumina is its exceptional surface area. This property is particularly important in catalysis, where a high surface area can greatly enhance the efficiency of a catalyst. The company’s Gamma Alumina products have been widely used as catalyst supports in various chemical reactions, enabling faster reaction rates and higher yields.Furthermore, the uniform particle size of Gamma Alumina ensures consistent performance in applications such as chromatography and adsorption. This level of consistency is crucial in many industrial processes, where the slightest variation in material properties can have significant impacts on the final product.In addition to its physical properties, Gamma Alumina also boasts impressive thermal stability. This makes it suitable for use in high-temperature applications, where many other materials would not be able to withstand the extreme conditions. As a result, Gamma Alumina has found its way into a wide range of industries, from petrochemicals to environmental protection.The company has leveraged its extensive expertise in material science to develop a comprehensive range of Gamma Alumina products, each tailored to specific applications and requirements. This level of customization has enabled the company to cater to a diverse customer base, providing solutions for a wide range of challenges in various industries.One notable area where Gamma Alumina has made a significant impact is in environmental technology. With its exceptional adsorption properties, Gamma Alumina has been used in numerous air and water purification systems. Its ability to effectively capture and remove impurities has made it an essential component in the fight against pollution and contamination.In summary, Gamma Alumina has solidified its position as a key product in the company’s portfolio, offering exceptional performance and versatility for a wide range of applications. With a strong focus on innovation and development, the company continues to drive forward the boundaries of what is possible with this remarkable material. As industries continue to evolve and new challenges arise, Gamma Alumina is poised to play a crucial role in shaping the future of material science and industrial processes.
Sulfur Recovery Catalyst: Key Player in Chemical Industry
Claus Sulfur Recovery Catalyst is a breakthrough technology that has been developed by an innovative company in the chemical industry. This catalyst has the potential to revolutionize the way sulfur is recovered from various industrial processes, making it more efficient and cost-effective.The company behind this groundbreaking technology is a global leader in providing advanced solutions for the chemical industry. With decades of experience and a team of highly skilled engineers and scientists, they are dedicated to creating innovative products that address the challenges faced by the industry.The Claus Sulfur Recovery Catalyst is a prime example of their commitment to innovation and sustainability. Sulfur recovery is a critical process in many industries, particularly in oil and gas refining, where sulfur is removed from hydrocarbons to meet increasingly stringent environmental regulations. The traditional method of sulfur recovery involves the use of a Claus unit, which relies on a series of chemical reactions to convert hydrogen sulfide into elemental sulfur.However, this process is not without its drawbacks. The Claus process is known for its high operating costs, as well as the need for frequent catalyst replacement, which can result in downtime and production losses. Additionally, the traditional Claus process often requires high temperatures and pressures, which can pose safety and operational challenges.The Claus Sulfur Recovery Catalyst aims to address these issues by offering a more efficient and reliable alternative to traditional sulfur recovery methods. This innovative catalyst is designed to enhance the conversion of hydrogen sulfide to elemental sulfur, while also extending the life of the catalyst and reducing the frequency of replacement.One of the key advantages of the Claus Sulfur Recovery Catalyst is its ability to operate at lower temperatures and pressures compared to traditional methods. This not only reduces operational costs but also makes the process safer and more manageable for plant operators. Furthermore, the improved performance and longevity of the catalyst result in fewer shutdowns for maintenance, leading to increased production efficiency and profitability.In addition to these benefits, the Claus Sulfur Recovery Catalyst also contributes to environmental sustainability. By enabling more efficient sulfur recovery, this technology helps to minimize the release of sulfur dioxide emissions, which can have detrimental effects on air quality and public health. As environmental regulations continue to tighten around the world, the demand for innovative solutions like this catalyst is only expected to grow.The company's commitment to sustainability extends beyond the products they offer. They are dedicated to minimizing their environmental footprint throughout the entire product lifecycle, from raw material sourcing to manufacturing and distribution. This includes efforts to reduce energy consumption, emissions, and waste generation, as well as the responsible disposal of end-of-life products.Furthermore, the company places a strong emphasis on research and development to continuously improve their products and develop new, cutting-edge solutions for the chemical industry. Their state-of-the-art research facilities and collaboration with leading academic institutions and industry partners position them at the forefront of innovation in the field.In conclusion, the Claus Sulfur Recovery Catalyst represents a significant advancement in sulfur recovery technology, offering a more efficient, reliable, and sustainable solution for the chemical industry. With the support of a forward-thinking and environmentally conscious company, this innovative catalyst is poised to make a positive impact on the industry and contribute to a greener, more sustainable future.
Newly Discovered Zeolite ZSM-22 Shows Promise in a Variety of Applications
ZSM-22, a breakthrough material in the world of advanced ceramics, has recently made waves in the industry with its unparalleled performance and versatility. This cutting-edge material, developed by a renowned research and development team at a leading technology company, is set to revolutionize a wide range of applications, including high-performance catalysts, efficient energy storage, and durable industrial coatings.Since its discovery, ZSM-22 has attracted significant attention from various industries due to its exceptional properties and potential for numerous practical applications. The material possesses a unique combination of high thermal stability, excellent mechanical strength, and superior chemical resistance, making it an ideal choice for tackling some of the most challenging tasks in modern engineering and manufacturing.One of the key advantages of ZSM-22 lies in its ability to act as a highly efficient catalyst for chemical reactions. With its intricate pore structure and tailored surface properties, ZSM-22 exhibits remarkable catalytic activity and selectivity, enabling the production of valuable chemicals and fuels with enhanced efficiency and reduced environmental impact. This makes ZSM-22 an attractive option for a wide range of industries, including petrochemicals, pharmaceuticals, and fine chemicals manufacturing.In addition to its catalytic performance, ZSM-22 has also shown great promise in energy storage and conversion applications. The material's unique electronic and ionic conductivity properties make it a promising candidate for next-generation batteries and supercapacitors, offering the potential to deliver higher energy density, faster charging rates, and longer cycle life compared to conventional energy storage technologies. Furthermore, ZSM-22's exceptional chemical stability and thermal insulation properties make it an excellent candidate for high-temperature fuel cell applications, where it can help improve overall performance and durability.Moreover, ZSM-22's remarkable mechanical strength and wear resistance make it an ideal choice for industrial coatings and protective layers. Its ability to withstand harsh operating conditions, such as high temperatures, corrosive environments, and abrasive wear, makes it a valuable asset for extending the lifespan and performance of critical components in various industrial settings, including automotive, aerospace, and machinery manufacturing.The company responsible for the development of ZSM-22 has been at the forefront of advanced materials research and innovation for several decades. With a strong focus on developing high-performance materials that address the evolving needs of modern industry, the company has consistently delivered groundbreaking solutions that push the boundaries of what is possible in the world of materials science and engineering.Through its state-of-the-art research facilities and multidisciplinary team of experts, the company has been able to bring to market a wide variety of innovative materials that have had a significant impact on the industry. ZSM-22 is the latest addition to the company's impressive portfolio of advanced ceramics, and it is poised to make a lasting impression on the global market with its exceptional performance and versatility.As the demand for high-performance materials continues to grow across various industries, ZSM-22 is expected to play a vital role in enabling new technologies and solutions that address the complex challenges of today's world. With its unique combination of properties and potential for diverse applications, ZSM-22 is set to redefine the standards for advanced ceramics and create new opportunities for innovation across a wide range of industries. The company behind ZSM-22 is committed to further advancing the material's capabilities and exploring its full potential, ensuring that it continues to drive progress and shape the future of material science and engineering.