Latest Developments in Catalyst Technology: Key Insights and Updates
By:Admin
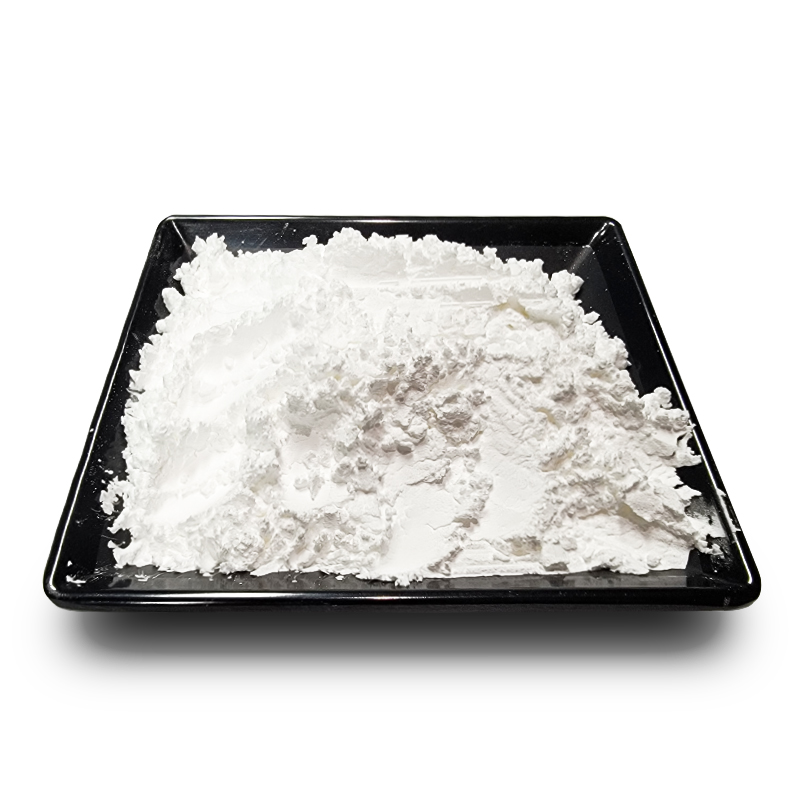
The global fuel landscape is rapidly transforming, with an increasing demand for cleaner and sustainable energy. Biogas, which is produced from organic waste and renewable resources, has been identified as a promising source of renewable energy.
However, the biogas needs to be upgraded before it can be used as a transportation fuel or injected into the natural gas grid, to remove impurities like carbon dioxide, water vapor, and hydrogen sulfide. Currently, the most common method of upgrading biogas is cryogenic separation, which is costly, energy-intensive, and requires specialized equipment.
Enter Clariant Catalyst, a pioneering company that develops catalysts and processes that enable the efficient and sustainable production of chemicals and fuels from renewable resources. The company has just announced the development of a new method to upgrade biogas to renewable natural gas (RNG), which is poised to revolutionize the biogas upgrading industry.
Clariant's new method is a catalytic thermal treatment process, which operates at high temperatures and transforms the biogas into RNG by converting carbon dioxide into methane. This approach has several advantages over the conventional cryogenic separation method. Firstly, it does not require any external energy input, as the process heat is generated by the exothermic reactions that occur during the catalytic conversion. This reduces the overall energy consumption of the process, making it more cost-effective and sustainable.
Secondly, the catalytic thermal treatment process is highly selective, meaning that it only converts carbon dioxide to methane, leaving other impurities like water vapor and hydrogen sulfide behind. This simplifies the downstream purification process, as the impurities are concentrated in a smaller volume and can be removed more efficiently.
Thirdly, the catalytic thermal treatment process can be easily integrated into existing biogas plants, as it does not require any major modifications or investments in new equipment. This makes it a scalable and adaptable solution that can be customized to different feedstocks and processing capacities.
According to Clariant, the new method has already been successfully tested at a pilot plant in Germany, which used biogas from food waste as a feedstock. The results showed that the process achieved a methane yield of over 98%, with a carbon dioxide reduction rate of over 90%.
Furthermore, the RNG produced by Clariant's method meets the strict quality standards required for injection into the natural gas grid, making it a valuable commodity that can be sold on the market. This creates a new revenue stream for biogas producers, who can now upgrade their biogas to a higher-value product and enhance the profitability of their operations.
In conclusion, Clariant Catalyst's innovative method of upgrading biogas to renewable natural gas represents a significant breakthrough in the quest for sustainable and affordable energy sources. By using a catalytic thermal treatment process that is energy-efficient, selective, and adaptable, Clariant has opened up new possibilities for biogas upgrading, and paved the way for a cleaner, greener, and more prosperous future.
Company News & Blog
Diverse Applications of Microspheres: Lightweight, High Strength Ceramic Spheres Enhancing Rheology and Thermal Insulation
Title: Alumina Microspheres: Revolutionizing Various IndustriesIntroduction to Alumina MicrospheresAlumina microspheres, also known as cenospheres, are lightweight and hollow ceramic spheres with a wide range of applications. Composed primarily of silica and alumina and sized below 300 microns, these microscopic spheres possess unique properties that make them highly versatile in several industries.Applications of Alumina Microspheres1. Construction Industry: A. Cementitious Systems: Alumina microspheres are used in cementitious systems to modify rheology, reduce weight and shrinkage, and enhance thermal insulation. They improve the overall performance of cement-based products such as sealants, putties, dry-mix adhesives, mortars, jointing compounds, and oil-well cements. B. Refractories: Specialized grades of alumina microspheres are employed in refractory applications. They enhance the thermal insulation properties of refractory materials utilized in high-temperature environments, such as furnaces, kilns, and reactors. C. Surface Coatings: Alumina microspheres find their usage in surface coatings, where they improve the durability, strength, and impact resistance of the coatings.2. Polymer Industry: Alumina microspheres are incorporated into various polymer applications to enhance their mechanical properties and reduce resin demand. A. Plastics and Gel-coats: They are extensively used in the plastics and gel-coats industry, including polyurethane, latex emulsions, PVC, epoxy resins, and unsaturated polyester resins. The addition of alumina microspheres not only strengthens the materials but also improves their impact resistance. B. Composite Materials: Alumina microspheres aid in reducing the amount of resin required in composite materials. This results in lighter and more cost-effective composites without compromising the strength and impact resistance of the final product.Advantages and Properties of Alumina Microspheres1. Low Bulk Density: Alumina microspheres possess low bulk density, which makes them ideal for applications where weight reduction is a requirement. This property is highly advantageous in the construction industry, where lightweight materials are desired without compromising structural integrity.2. High Strength: Despite their lightweight nature, alumina microspheres exhibit high strength. This property enhances the overall durability and impact resistance of the materials they are incorporated into, making them an excellent choice for various industries.3. Uniform Sphericity: The uniform sphericity of alumina microspheres ensures consistent performance and ease of incorporation into different applications. Their spherical shape facilitates even distribution within matrices, resulting in enhanced mechanical properties and consistent end products.4. Thermal Insulation: Alumina microspheres improve thermal insulation due to their hollow structure, which reduces heat transfer. This property finds significant use in refractories and cementitious systems, where thermal insulation is crucial for energy efficiency.ConclusionAlumina microspheres have revolutionized the construction and polymer industries with their unique properties and diverse range of applications. With their low bulk density, high strength, uniform sphericity, and thermal insulation capabilities, these microscopic spheres have proven to be essential additives in cementitious systems, refractories, surface coatings, and polymer applications.Whether it is modifying rheology, reducing weight and shrinkage, improving impact resistance, enhancing thermal insulation, or reducing resin demand, alumina microspheres offer tangible benefits to various industries. As innovation continues to drive the development of new materials and technologies, the use of alumina microspheres is expected to grow further, enabling the creation of lighter, stronger, and more efficient products.
Versatile Applications of Microspheres in Cementitious Systems, Composites and Polymer Materials
What Are Alumina Microspheres and Their Importance in Various Industries?Alumina Microspheres, also known as Cenospheres, are lightweight, thin-walled, hollow ceramic spheres composed mainly of alumina and silica, and are typically below 300 microns in size. These unique characteristics make them highly effective in a range of industrial applications across multiple industries.The low bulk density and high strength of alumina microspheres are crucial to their success in the manufacturing industry. They are an essential component of cementitious systems, putties, and sealants. In these products, they modify rheology, reduce weight and shrinkage, and improve thermal insulation properties. Because of these benefits, they are also used in composites and other polymer applications, where they reduce resin demand and improve impact resistance and strength.Specialized alumina microsphere grades are used in industries that require rigorous application conditions. For example, refractories and surface coatings utilize industrial-grade microspheres for coating applications. These coatings provide superior heat resistance, making them ideal for use in high-temperature conditions.Several end-user industries use Alumina Microspheres due to their unique properties. The plastics and gel-coats industry uses these microspheres in polyurethane, latex emulsions, PVC, and Epoxy resins. They are also frequently used in oil-well cements, dry-mix adhesives, and mortars.One major advantage of Alumina Microspheres is their ability to reduce weight and shrinkage in cementitious products. This crucial factor allows manufacturers to create lighter, stronger, and more durable products while saving on production costs.In composites, the incorporation of Alumina Microspheres improves the mechanical performance of the final product, and reduces weight and cost. Additionally, they can be used in high-temperature applications because of their superior resistance to heat.In surface coatings, Alumina Microspheres help improve the wear and tear resistance of the final product. Additionally, thermal insulation properties of the coating prevent heat loss from the surface.In summary, Alumina Microspheres offer several unique advantages to manufacturers across numerous industries. Their low bulk density and high strength make them ideal for enhancing the performance of cementitious, composite, and coating products. Their versatility and applicability in various industries make them a valuable resource for manufacturers and end-users alike.
and hydrocarbon isomerization reactions.ZSM-5: The Revolutionary Catalyst for Hydrocarbon Isomerization ReactionsZSM-5, also known as Zeolite Socony Mobil5, is a remarkable aluminosilicate zeolite that has revolutionized the petroleum industry. Patented by Mobil Oil Company in 1975, it has become one of the most widely used heterogeneous catalysts for hydrocarbon isomerization reactions. Its unique pore structure and acidity make it ideal for transforming straight-chain hydrocarbons into their branched counterparts, which have higher octane numbers and are therefore more valuable as gasoline components. In this blog, we will explore the fascinating properties of ZSM-5 and how it works as a catalyst for hydrocarbon isomerization reactions.ZSM-5 belongs to the pentasil family of zeolites, which are characterized by their five-membered rings of silicon and aluminum atoms. Its framework structure is based on the MFI type topology, which consists of intersecting channels with pore sizes of about 0.5-0.6 nm. These channels are lined with acidic sites, which can selectively adsorb and catalyze the isomerization of straight-chain hydrocarbons. The chemical formula of ZSM-5 is NaAlSiO16HO (0
New Honeycomb Catalyst Discovered for Efficient Conversion of Biomass
Title: Groundbreaking ZSM-5 Catalyst: Revolutionizing Industrial ProcessesIntroduction:In a groundbreaking development, researchers have harnessed the extraordinary potential of ZSM-5 catalyst to revolutionize various industrial processes. ZSM-5, an exceptional zeolite material known for its unique properties, has now been combined with cutting-edge advancements by the industry-leading company [Company Name]. This groundbreaking partnership aims to enhance efficiency, sustainability, and cost-effectiveness across several sectors, positioning itself as a key player in transforming industrial processes worldwide.[Company Name] – Pioneering Innovation:[Company Name] has established itself as a trailblazer in developing and implementing innovative solutions across a wide range of industries. With a strong commitment to research and development, the company has harnessed its expertise to optimize the applications of ZSM-5 catalyst, positioning itself as an industry leader.The company's core philosophy revolves around sustainability, environmental consciousness, and maximizing efficiency. By developing eco-friendly technologies and fostering responsible manufacturing processes, [Company Name] aims to create a better world by significantly reducing environmental footprints and ensuring a sustainable future for generations to come.ZSM-5 Catalyst: Unleashing the Potential:ZSM-5 catalyst, a highly crystalline and versatile zeolite material, is known for its unique pore structure and acidic properties. Its exceptional attributes make it the ideal catalyst for various industrial processes such as petrochemical refining, biofuel production, and environmental conservation.1. Petrochemical Refining:ZSM-5 catalyst plays a pivotal role in petrochemical refining, significantly improving the efficiency of key processes. By optimizing the catalyst's structure and composition, [Company Name] has successfully enhanced the selectivity and yields of valuable petrochemical products. This not only leads to higher production rates but also reduces waste and minimizes the environmental impact of the refining process.2. Biofuel Production:In the pursuit of sustainable energy sources, ZSM-5 catalyst has emerged as a game-changer in biofuel production. By catalyzing the conversion of biomass into biofuels, it offers a viable alternative to traditional fossil fuels. Through intensive research and development, in collaboration with leading institutions, [Company Name] has successfully bolstered the performance of ZSM-5 catalyst, making it more efficient and economically viable for large-scale biofuel production. This breakthrough promises to reduce reliance on non-renewable resources and combat climate change.3. Environmental Conservation:ZSM-5 catalyst has also been instrumental in environmental conservation efforts. With its high selectivity, the catalyst aids in the removal of harmful pollutants from industrial emissions, contributing to improved air quality and reduced pollution levels. [Company Name] has leveraged its expertise to optimize ZSM-5 catalyst for specific applications, ensuring maximum efficiency and minimized environmental impact.Future Implications:The collaboration between [Company Name] and ZSM-5 catalyst is poised to transform multiple industries, offering immense potential for sustainable development and innovation. As environmental concerns continue to grow, the enhanced capabilities of ZSM-5 catalyst hold the key to meeting global demands while reducing carbon footprints and preserving the planet's resources.By leveraging its research and development capabilities, [Company Name] remains dedicated to further advancements in ZSM-5 catalyst, exploring new applications, and pushing the boundaries of possibility. The company's commitment to sustainability and responsible manufacturing practices guarantees a brighter and more efficient future for industries and communities worldwide.Conclusion:The groundbreaking combination of ZSM-5 catalyst and [Company Name]'s cutting-edge expertise marks a revolutionary shift in various industrial processes, promising enhanced efficiency, sustainability, and cost-effectiveness. With its unique attributes and endless potential, ZSM-5 catalyst has become a catalyst for change, steering industries towards a greener and more prosperous future.As the research and development journey continues, [Company Name]'s commitment to innovation and sustainability will undoubtedly unlock new horizons, contributing to a more sustainable world and setting new standards for industrial processes globally.
New Technology Could Revolutionize the Reforming Catalyst Industry
Reforming Catalyst is a key component in the refining industry that plays a critical role in converting heavy naphtha into high-octane gasoline. In a move towards sustainability and energy efficiency, the industry is constantly searching for innovative and advanced reforming catalysts that can improve the refining process and reduce environmental impact. Recent developments in refining technology have led to the introduction of a new reforming catalyst that promises to deliver superior performance and efficiency.This new catalyst, which is yet to be officially named, has been designed by a leading chemical manufacturer with extensive experience in developing innovative solutions for the refining industry. The company specializes in creating catalysts that can withstand high temperatures and harsh operating conditions, maximizing the yield and quality of refined products. The new reforming catalyst is no exception as it has been tested extensively to ensure superior performance and reliability.According to industry experts, the new reforming catalyst has several advantages over existing catalysts. The most notable of these advantages is increased octane yield, which can significantly improve the quality of gasoline produced in refineries. The catalyst is also highly selective, ensuring that only the desired chemical reactions take place during the refining process. This selectivity reduces the amount of by-products produced by the refinery, which is beneficial for the environment, as it reduces emissions and waste.Another advantage of the new reforming catalyst is its durability. The catalyst has a longer lifespan than existing catalysts, which means that it can operate efficiently for longer periods without requiring replacement. This is particularly important for refineries, as it reduces the downtime associated with catalyst replacement, which can be costly and time-consuming.The company behind the new reforming catalyst is committed to sustainability and has a track record of creating innovative solutions that reduce environmental impact. The new catalyst has been designed to reduce emissions during the refining process, which is beneficial for the environment and the community. The company is also committed to using sustainable materials and processes in production, further reducing the ecological footprint of the catalyst.The development of the new reforming catalyst comes at a time when the refining industry is facing increasing pressure to reduce its environmental impact. Governments around the world are implementing stricter regulations on emissions and waste, which means that refineries need to find innovative solutions to stay competitive and compliant. The introduction of the new reforming catalyst is a step towards a cleaner, more sustainable refining industry.The new catalyst is expected to be widely adopted by refineries around the world, as it offers significant performance and efficiency gains compared to existing catalysts. The chemical manufacturer has already received significant interest from industry players, who are eager to incorporate the new catalyst into their refining operations. The company is currently working on scaling up production to meet demand and expects to see widespread adoption of the new catalyst in the coming years.In conclusion, the introduction of the new reforming catalyst represents a significant step forward for the refining industry. The new catalyst promises to deliver superior performance, efficiency and sustainability and is set to become an essential component in the refining process. With its increased octane yield, selectivity, durability and reduced environmental impact, the new reforming catalyst is a game-changer for the industry. As the world moves towards a more sustainable future, the introduction of this innovative solution is a positive development that promises to benefit both the industry and the environment.
New Methanation Catalyst Could Revolutionize Renewable Energy Production
Methanation Catalyst, a revolutionary new product in the field of chemical production, has been introduced by a leading chemical company. This innovative solution is designed to help industries address the challenges of producing clean energy by utilizing carbon dioxide and renewable hydrogen to produce methane. The new catalyst is a game-changer for industries looking for sustainable ways to produce clean fuels, and it is set to transform the way we produce energy.The Methanation Catalyst is a high-performance catalyst that significantly improves the efficiency of the methanation process, where carbon dioxide and renewable hydrogen are chemically transformed into methane. The catalyst is formulated to have a high activation energy, which enables it to speed up the methanation reaction significantly. This breakthrough product has already been integrated into several industrial processes, such as ammonia production and gas-to-liquid processes.The Methanation Catalyst is composed of several key ingredients that enable it to perform efficiently. These ingredients include a unique support structure that helps to facilitate the carbon dioxide reduction reaction. The catalyst also contains active metal sites that promote the hydrogenation of carbon dioxide, which is critical to the methanation process.According to leading industry experts, the Methanation Catalyst is an important solution to the challenges that industries face with conventional methanation processes. This new catalyst provides industries with a sustainable method of producing clean energy by harnessing renewable hydrogen and carbon dioxide. The catalyst is also cost-effective, which is a significant advantage for companies operating in competitive markets.The Methanation Catalyst has already been tested in several industrial processes and has demonstrated exceptional results. In large-scale ammonia production, the catalyst increased the conversion rate of carbon dioxide to methane while reducing the energy required for the methanation process. The performance of the catalyst in these tests has demonstrated that Methanation Catalyst is a reliable and efficient solution for industries.Methanation Catalyst is also playing an important role in the transition to green energy. The demand for cleaner energy sources continues to increase globally, and this product provides a solution. The catalyst allows industries to produce a clean, renewable, and sustainable source of energy, ultimately contributing to the goal of creating a more sustainable future.The supply of hydrogen is critical for the methanation process, and industries require a reliable and sustainable source of hydrogen to produce high-quality methane. The Methanation Catalyst enables industries to utilize renewable hydrogen produced from various sources such as solar and wind power. This is an important step towards achieving net-zero carbon emissions, and the Methanation Catalyst is a crucial technology that will support this transition.The Methanation Catalyst is just one of the many innovative solutions developed by leading chemical companies to help reduce carbon emissions and support the transition to clean energy. The company that has introduced Methanation Catalyst is a world-renowned leader in the development and production of high-quality catalysts and has a long-standing track record of delivering excellent products and services to the chemical industry.The introduction of Methanation Catalyst is a significant milestone for the industry, and it is poised to transform the way we produce energy. The product represents a new era in sustainable energy production, and it is one of the innovative solutions that industries can utilize to reduce their carbon footprint. The Methanation Catalyst is not only a solution for energy production; it is also an example of how innovative technology can be utilized to create a more sustainable and cleaner future for everyone.In conclusion, the introduction of Methanation Catalyst is a significant achievement for the chemical industry, and it is set to revolutionize the way we produce energy. The product offers a sustainable and reliable solution to the challenges of methanation and provides a path towards a sustainable and carbon-neutral future. With Methanation Catalyst, industries have a tool to produce clean energy sustainably while addressing the challenges of climate change.
Tail Gas Hydrogenation Catalyst: The Solution to Carbon Emission
Tail Gas Hydrogenation Catalyst: Revolutionizing the Petroleum Refining IndustryTail gas is commonly produced during various refining processes in the petroleum industry. It consists of the unreacted hydrogen and sulfur compounds that are typically found in fuel gas and light gas oil. These compounds are harmful to the environment and need to be removed before the gas can be utilized or released safely. To address this issue, a groundbreaking catalyst has emerged - the Tail Gas Hydrogenation Catalyst, which has revolutionized the petroleum refining industry. This catalyst, developed by a leading chemical company, has proven to be highly efficient in removing sulfur compounds and other harmful impurities from tail gas. Its effectiveness lies in its ability to promote the hydrogenation reactions responsible for converting sulfur compounds into hydrogen sulfide, a less harmful compound. The catalyst provides a surface for the reactions to occur, thus increasing their rate and efficiency.The Tail Gas Hydrogenation Catalyst is composed of various active components, such as metal oxides and promoters, which play a vital role in the catalytic process. The careful selection and combination of these components ensure that the catalyst is both highly reactive and long-lasting. Additionally, the company has implemented proprietary manufacturing techniques to ensure consistent catalyst quality and performance.What sets this catalyst apart from previous iterations in the market is its high selectivity towards sulfur compounds, leading to a remarkable reduction in sulfur content in tail gas. This selectivity ensures that only the harmful impurities are removed, while other valuable components of the gas are left intact. The result is cleaner gas that can be utilized more efficiently or released with significantly reduced environmental impact.Furthermore, the Tail Gas Hydrogenation Catalyst boasts exceptional thermal stability, enabling it to operate at high temperatures encountered in petroleum refining processes. This characteristic is crucial in maintaining catalyst activity and prolonging its lifespan. By withstanding these extreme conditions, the catalyst can continue to deliver exceptional performance, reducing the frequency of catalyst replacement and consequently decreasing overall operational costs.The company behind this innovative catalyst has a long-standing reputation in the chemical industry for its commitment to research and development. It employs a team of renowned scientists and engineers who continuously strive to improve their products and develop cutting-edge solutions for various industries. Their expertise and dedication have led to the development of groundbreaking catalysts like the Tail Gas Hydrogenation Catalyst.In addition to its technical excellence, the company values sustainability and seeks to implement environmentally friendly practices throughout its operations. This commitment is reflected in the design and manufacturing of the catalyst, which focuses on reducing emissions and minimizing waste generation. By incorporating sustainability into their core principles, the company aims to contribute to a cleaner, greener future for the refining industry.The introduction of the Tail Gas Hydrogenation Catalyst marks a significant milestone in the petroleum refining industry. Its unmatched selectivity, thermal stability, and sustainability features have positioned it as a game-changer in the field. By effectively removing harmful sulfur compounds from tail gas, the catalyst improves overall efficiency, reduces environmental impact, and ensures compliance with stringent regulations.As the petroleum industry continues to evolve and face growing sustainability demands, the Tail Gas Hydrogenation Catalyst serves as a shining example of how innovative technologies can pave the way for a cleaner, more efficient future. With its exceptional performance and the company's commitment to continuous improvement, the catalyst is set to revolutionize the refining industry, driving it towards a greener tomorrow.
Get Quality Activated Alumina for Catalyst Carriers at Low Prices from Professional Manufacturers
Breaking News: Enhanced Catalyst by Leading Provider Revolutionizes Industry
Clariant Catalyst, a leading innovator in the production of high-performance catalysts, has announced a major breakthrough in the field of catalysis. Their latest product has been developed to deliver greater efficiency, improved sustainability, and enhanced performance to the petrochemical industry.Catalysts are integral components in a variety of chemical reactions and are used to speed up the rate of a reaction or lower the amount of energy required. Clariant Catalysts has been pioneering the field of catalysts for over 70 years and has gained a reputation as a reliable and innovative provider of catalyst solutions.With the petrochemical industry being one of the largest consumers of catalysts, there has been a growing demand for catalysts that can help reduce costs, increase efficiency, and minimize environmental impact. This is where Clariant Catalysts' latest solution comes in.Clariant Catalysts' latest product represents a new class of catalysts that combines two key technologies: high-performance catalysts and sustainability. By incorporating these two technologies, the company has developed a solution that can help petrochemical companies increase efficiency, reduce waste, and ultimately, improve their bottom line.The new catalyst product has been designed to address some of the most pressing problems faced by the petrochemical industry. For instance, the catalyst is capable of converting different types of feedstocks into high-quality products. This is particularly important in the current period when there is an increasing demand for more advanced fuels and other petrochemical products. Furthermore, the new catalyst product can help reduce costs by reducing the amount of energy required to transform feedstocks into products. The result is a more efficient production process that leads to enhanced profitability.Another critical area that the new catalyst product addresses is sustainability. As the world focuses on reducing carbon emissions and transitioning to a greener economy, the petrochemical industry has come under scrutiny for its heavy reliance on fossil fuels. Clariant Catalysts' latest solution is designed to help petrochemical companies reduce their carbon footprint by using renewable feedstocks and reducing energy requirements. By doing so, the new catalyst product can help petrochemical companies meet sustainability goals and comply with regulatory requirements.Clariant Catalysts has always been committed to developing innovative and sustainable catalyst solutions. The company has invested heavily in research and development and has attracted some of the brightest minds in the field of catalysis. Their latest breakthrough represents a significant milestone in the company's history and is a testament to their dedication to sustainability and innovation.The new catalyst product has already generated significant interest from industry players, and its potential impact has been recognized by experts in the field. Andrew Sinclair, Head of Business Unit Catalysts at Clariant said, "We see a growing demand for catalysts that can help the petrochemical industry incorporate sustainability into their production processes. Our latest product is a game-changer in this regard, and we are thrilled to be able to offer it to our customers."The development of the new catalyst product has been a collaborative effort, involving experts from different fields. This multidisciplinary approach has resulted in a product that is truly unique and represents the cutting edge of catalysis.In conclusion, Clariant Catalysts' latest breakthrough represents a major step forward in the field of catalysis. Their new catalyst product offers petrochemical companies a pathway to more sustainable and efficient production processes. With an increasing focus on reducing carbon emissions and transitioning to a greener economy, solutions like Clariant Catalysts' latest product will become increasingly important. The company's commitment to sustainability and innovation is a model for others in the industry to follow.
Discover the Latest Advancements in Alumina Research - Unveiling the Potential of Gamma Alumina
Gamma Alumina: Advancing Materials Science and Redefining Industrial PossibilitiesGamma Alumina is a high-performance material company that is redefining the industrial possibilities. The company takes pride in offering innovative solutions that are changing the way we look at materials science. Gamma Alumina products have diverse applications in various industries, including petrochemical, electronic, and pharmaceutical, among others. But what is Gamma Alumina, and what makes it so exceptional?Gamma Alumina is a type of alumina that exhibits unique physical and chemical properties, including high surface area, high purity, and thermal stability. This makes it an ideal material in many industrial processes. The company produces gamma alumina nanopowders using a proprietary method that combines cutting-edge technology and innovative process engineering.One of the most significant advantages of Gamma Alumina is its excellent catalytic properties. Gamma Alumina is used as a catalyst support in chemical reactions, enhancing reaction efficiency, and selectivity. The nanopowders offer a significant surface area to volume ratio, providing an optimized surface for catalytic activity. This implies that the material can catalyze a high rate of chemical reactions with minimal energy input, making it energy efficient and sustainable.Gamma Alumina is also widely used as an adsorbent material, where it can selectively adsorb specific molecules from gas or liquid streams. This has led to its use in purification processes to remove impurities from various industrial products such as natural gas, petrochemicals, and water. Its high surface area and unique pore structure make it an ideal material for selective separation processes, improving product purity and quality.Another significant application of Gamma Alumina is in the manufacture of ceramics and electronic materials. Gamma Alumina is used as a precursor for the production of advanced ceramics and glass matrices through the sol-gel process. It is also used in the production of electronic ceramics such as capacitors, insulators, and superconductors. Gamma Alumina offers a high degree of purity, thermal stability, and good dielectric properties, making it an ideal material in electronic applications.Gamma Alumina is also used in the pharmaceutical industry. It is used as a drug carrier in drug delivery systems, and as an intermediate in peptide synthesis. The material's unique adsorption properties allow it to adhere to specific drug molecules, improving the efficacy of the drug. Gamma Alumina is also used in bioceramic applications such as bone cement, where it provides mechanical stability and biocompatibility.In conclusion, Gamma Alumina is an exceptional material with diverse applications across various industries. Its unique physical and chemical properties make it an ideal material in many industrial processes. At Gamma Alumina, we are continually redefining the industrial possibilities by offering innovative solutions that enhance efficiency and sustainability in industrial processes. Our proprietary method of producing gamma alumina nanopowders allows us to deliver high-quality materials suitable for various applications. We are committed to advancing materials science, and our team of experts is always working to develop new applications of Gamma Alumina. We take pride in being at the forefront of materials science, and we look forward to expanding our footprint in different industries.