Enhancing Catalyst Performance: A Step towards Efficient Reforming
By:Admin
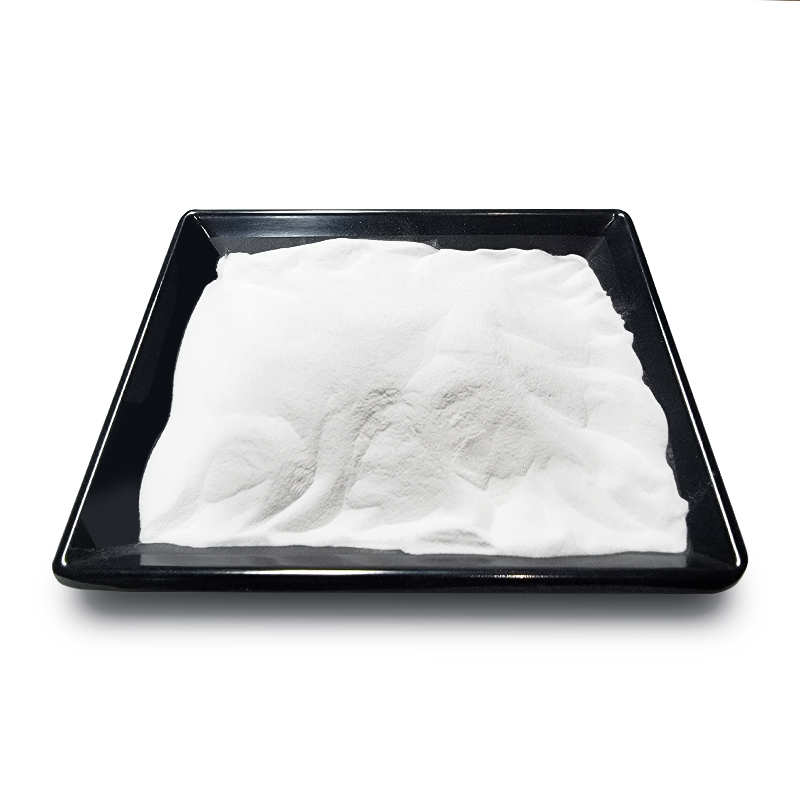
Industries around the world are constantly striving to improve efficiency, reduce emissions, and enhance productivity. Now, with the emergence of reforming catalyst technology, a groundbreaking solution is at hand. By streamlining and optimizing industrial processes, this cutting-edge catalyst is poised to revolutionize a wide range of industries, from energy production to automotive manufacturing.
Traditionally, industrial processes have been hindered by various challenges, such as high energy consumption, extensive environmental impacts, and limited product yields. In an effort to overcome these obstacles, reforming catalyst technology has become a beacon of hope for many. With its ability to enhance reactions, increase selectivity, and minimize undesirable byproducts, this catalyst has the potential to transform entire industries.
Reforming catalyst technology works by promoting the desired reactions while suppressing unwanted side reactions. By doing so, it maximizes the product yield and improves the overall efficiency of the process. This catalyst operates at high temperatures, making it suitable for a wide range of applications, including petrochemical production, ammonia synthesis, and hydrogen generation.
One key area where reforming catalyst technology is making a significant impact is in the production of clean energy. Green energy sources, such as solar and wind power, are becoming increasingly popular, but their intermittent nature poses challenges for stable energy supply. This is where reforming catalyst technology comes into play. By utilizing this catalyst in conjunction with renewable energy sources, industries can efficiently convert excess electricity into hydrogen, a versatile and clean fuel. Hydrogen can be stored and used when renewable energy generation is low, ensuring a reliable and sustainable energy supply. Moreover, the byproduct of hydrogen production, water, makes it an eco-friendly alternative to traditional fossil fuels.
Another sector poised to benefit greatly from reforming catalyst technology is the automotive industry. As the world transitions towards sustainable transportation, the demand for alternative fuels is on the rise. Reforming catalyst technology presents a viable solution by facilitating the production of hydrogen or synthetic fuels, such as methanol or dimethyl ether, from renewable sources. These fuels emit significantly lower carbon emissions compared to conventional gasoline or diesel, making them essential in curbing global warming and improving air quality.
In addition to its applications in the energy and transportation sectors, reforming catalyst technology has the potential to transform the production of valuable chemicals. Many industrial processes rely on the production of high-value chemicals, such as aromatics or olefins. However, these processes often generate large amounts of waste and have significant environmental impacts. By integrating reforming catalyst technology, industries can minimize waste, reduce energy consumption, and increase the selectivity of desired products. This not only enhances the economic viability of these processes but also contributes to a more sustainable future.
Reforming catalyst technology goes beyond enhancing industrial processes; it also provides economic advantages. With improved efficiency and higher product yields, companies can optimize their operations, reduce costs, and gain a competitive edge in the market. Moreover, as governments worldwide prioritize sustainability and environmental stewardship, industries that adopt reforming catalyst technology can position themselves as leaders in responsible manufacturing.
With its potential to revolutionize various industries, reforming catalyst technology is steadily gaining traction. As the world works towards a sustainable future, this catalyst offers a versatile and practical solution for optimizing industrial processes, reducing emissions, and maximizing productivity. By embracing this technology, companies can not only improve their bottom line but also contribute to a cleaner and greener planet.
{Company Introduction}
In conclusion, reforming catalyst technology has the potential to revolutionize industrial processes across a wide range of sectors. By improving efficiency, reducing emissions, and increasing selectivity, this catalyst offers a viable solution to the challenges faced by industries worldwide. With its applications in clean energy production, alternative fuels, and valuable chemicals, reforming catalyst technology is paving the way towards a more sustainable future. By adopting this innovative technology, companies can not only enhance their operations but also contribute to global efforts in combating climate change and ensuring a greener planet for future generations.
Company News & Blog
Discover the Potential of Alumina Desiccant for Effective Moisture Control
Headline: Innovative Alumina Desiccant Revolutionizes Moisture Control SolutionsSubtitle: Company X Raises the Bar in Moisture Management with Cutting-Edge Alumina Desiccant Technology[City, Date] – Moisture and high humidity levels can spell disaster for industries ranging from electronics to pharmaceuticals, causing corrosion, mold growth, and product degradation. To counter this pervasive issue, Company X, a renowned pioneer in moisture control solutions, has unveiled its game-changing Alumina Desiccant. Offering superior moisture absorption capabilities, the product is set to revolutionize the market with its innovative features.Company X has been the driving force behind the development of advanced desiccant solutions, consistently providing efficient moisture management products for various industrial applications. By harnessing state-of-the-art technology along with cutting-edge research, the company has introduced its latest breakthrough, a high-performance Alumina Desiccant, which boasts unparalleled levels of moisture absorption and long-term usage capabilities.The Alumina Desiccant is engineered to combat even the most challenging moisture-related issues. Its unique formulation, including high-quality activated alumina, ensures superior moisture absorption, effectively reducing humidity levels in various environments. This game-changing solution provides industries worldwide with an efficient and reliable tool to combat mold, mildew, corrosion, and product degradation caused by excess moisture.With a commitment to quality and product excellence, Company X ensures that its Alumina Desiccant meets and exceeds industry standards. Rigorous testing procedures and strict quality control measures have been implemented to guarantee the highest performance and reliability levels. The desiccant is available in various sizes and packaging options, catering to the diverse needs of different industries.Apart from its exceptional moisture absorption capabilities, the Alumina Desiccant offers several key features that set it apart from traditional desiccant solutions. The product's low-dusting formula minimizes the risk of contamination, making it suitable for applications within sensitive industries such as pharmaceuticals and food processing. Additionally, the desiccant's wide operating temperature range, from extreme cold to high heat, ensures its effectiveness across diverse climates and environments.Company X's dedication to environmental sustainability is reflected in its Alumina Desiccant as well. The product is entirely recyclable, reducing waste and promoting eco-conscious practices within industries. By providing an environmentally friendly solution, the company aims to contribute to a greener and more sustainable future.Company X understands that every industry faces unique moisture challenges. Thus, the company's professional team of engineers and technical experts is committed to providing comprehensive customer support. These experts work closely with clients to analyze their specific moisture-related issues and recommend the most appropriate solutions, guaranteeing optimal results and customer satisfaction.Industries across the globe have already begun recognizing the value of Company X's Alumina Desiccant. Customer testimonials praise the desiccant's outstanding performance, cost-effectiveness, and the reduction of product loss caused by moisture-related problems. With its innovative product range and commitment to surpassing customer expectations, Company X has firmly established itself as a leading provider of moisture control solutions.In conclusion, Company X's groundbreaking Alumina Desiccant is transforming the moisture control landscape by offering unmatched moisture absorption capabilities and innovative features. Through its tireless dedication to research and development, the company has once again raised the bar in moisture management. Ultimately, industries worldwide can rely on Company X's Alumina Desiccant to combat moisture-related challenges more effectively, ensuring product integrity and enhancing overall productivity.Contact:Company XPhone: XXX-XXXXXEmail: [email protected]: www.companyx.com
Newly Discovered ZSM-22: What You Need to Know
ZSM-22 Zeolite Revolutionizes the Energy IndustryZeolites are crystalline aluminosilicate minerals that are widely used for their unique properties in many industrial applications. One particular type of zeolite, ZSM-22, has been making waves in the energy industry due to its superior catalytic properties. This breakthrough has the potential to revolutionize the production of biofuels and petrochemicals, leading to more sustainable and efficient energy solutions.ZSM-22 zeolite is a highly porous material with a unique structure that allows it to act as a catalyst in chemical reactions. Its large surface area and uniform pore structure make it an excellent candidate for catalyzing the conversion of biomass and other renewable feedstocks into valuable fuels and chemicals. This includes the production of biofuels such as ethanol and biodiesel, as well as the synthesis of high-value intermediates for the petrochemical industry.In recent years, the demand for sustainable energy sources has been on the rise, driven by concerns over climate change and the depletion of fossil fuel reserves. As a result, there has been a growing interest in the development of alternative, renewable energy solutions. ZSM-22 zeolite offers a promising avenue for addressing these challenges by enabling more efficient and environmentally friendly processes for the production of biofuels and other renewable products.The unique properties of ZSM-22 zeolite have been leveraged by a leading company in the zeolite industry, {Company Name}, to develop innovative catalytic solutions for the energy sector. With a strong focus on research and development, {Company Name} has been at the forefront of advancing the application of zeolites in various industrial processes. The company's expertise in zeolite synthesis and characterization has played a crucial role in unlocking the potential of ZSM-22 for energy-related applications.Through extensive research and collaboration with academic institutions and industry partners, {Company Name} has successfully developed novel catalytic materials based on ZSM-22 zeolite that have shown remarkable performance in the conversion of renewable feedstocks into biofuels and petrochemicals. These advancements have the potential to significantly impact the energy industry by enabling more sustainable and cost-effective production processes.The benefits of ZSM-22 zeolite in the energy industry are far-reaching. By improving the efficiency of biofuel production, this innovative technology can help reduce the reliance on fossil fuels and mitigate greenhouse gas emissions. Furthermore, the use of renewable feedstocks in conjunction with ZSM-22 catalysts can contribute to the development of a more circular and sustainable economy.In addition to biofuels, ZSM-22 zeolite can also be used in the production of high-value chemicals and intermediates that are essential for the petrochemical industry. By facilitating the conversion of renewable feedstocks into these valuable products, ZSM-22 zeolite offers a versatile and environmentally friendly solution for meeting the growing demand for sustainable chemicals.The impact of ZSM-22 zeolite on the energy industry is poised to be significant, and {Company Name} is committed to driving the adoption of this breakthrough technology. Through ongoing research and innovation, the company aims to further optimize the performance of ZSM-22 catalysts and expand their application in energy-related processes. With a strong track record in developing cutting-edge zeolite materials, {Company Name} is well-positioned to lead the way in bringing ZSM-22 zeolite to the forefront of the energy industry.As the world continues to seek more sustainable and efficient energy solutions, the emergence of ZSM-22 zeolite as a catalyst for biofuel and petrochemical production represents a major milestone in the quest for a greener future. With the expertise and dedication of companies like {Company Name}, the potential of ZSM-22 zeolite to transform the energy industry is within reach, offering a promising path towards a more sustainable and prosperous tomorrow.
High Purity Alumina: A New Material with Endless Applications
Extraordinary Materials Inc., a leading provider of advanced materials and technologies, has recently introduced a new product in their already impressive lineup. The new product, Gamma Alumina, has been developed to meet the growing demands for high-quality, high-purity alumina in various industries including electronics, ceramics, and catalyst manufacturing. This new addition further solidifies Extraordinary Materials Inc.'s position as a key player in the advanced materials market.Gamma Alumina is a versatile material known for its exceptional properties and wide range of applications. It is a high-purity form of alumina that exhibits superior thermal stability, excellent surface area, and exceptional mechanical strength. These attributes make Gamma Alumina a sought-after material for a variety of applications in the industry.One of the key markets for Gamma Alumina is in the production of catalysts. The high surface area and stability of Gamma Alumina make it an ideal choice for catalyst support materials in the petrochemical and refining industries. Its use in catalyst manufacturing leads to improved performance and longevity of catalysts, ultimately resulting in higher efficiency and cost savings for plant operators.Another industry that benefits from the unique properties of Gamma Alumina is the electronics industry. The material's thermal stability and mechanical strength make it an excellent choice for various electronic applications, including as a filler material in electronic components and as a substrate for microelectronics. With the increasing demand for high-performance electronic devices, Gamma Alumina has the potential to play a significant role in advancing the next generation of electronic products.In addition to catalysts and electronics, Gamma Alumina also finds applications in the ceramics industry. Its exceptional mechanical strength and high purity make it an ideal material for ceramic manufacturing, where it is used to enhance the properties of ceramic products such as abrasives, refractories, and insulating materials.The introduction of Gamma Alumina underscores Extraordinary Materials Inc.'s commitment to innovation and cutting-edge technology. The company has a proven track record of developing and commercializing advanced materials that meet the evolving needs of various industries. With Gamma Alumina, Extraordinary Materials Inc. is once again at the forefront of delivering high-performance materials to its customers, positioning itself as a reliable partner for advanced material solutions."Gamma Alumina is a testament to our dedication to developing materials that push the boundaries of what is possible," said the CEO of Extraordinary Materials Inc. "We are excited to bring this exceptional material to the market and provide our customers with a high-quality solution that meets their specific needs. With Gamma Alumina, we are confident that we can continue to drive innovation and create value for our customers across different industries."Extraordinary Materials Inc. has built a strong reputation for its commitment to quality, innovation, and customer satisfaction. The company's state-of-the-art manufacturing facilities and R&D capabilities enable it to develop and produce a wide range of advanced materials with superior performance and reliability. By consistently investing in research and development, Extraordinary Materials Inc. is able to stay ahead of the curve and deliver materials that exceed industry standards.The introduction of Gamma Alumina is a testament to Extraordinary Materials Inc.'s dedication to pushing the boundaries of material science and technology. As the demand for high-performance materials continues to grow, Extraordinary Materials Inc. is well-positioned to lead the way in providing innovative solutions to meet the needs of various industries. With a strong focus on quality, innovation, and customer satisfaction, the company is set to continue its success in delivering advanced materials that drive progress and change in the industry.Overall, the introduction of Gamma Alumina underscores Extraordinary Materials Inc.'s commitment to staying at the forefront of the advanced materials market and providing its customers with the highest quality solutions. With its exceptional properties and versatile applications, Gamma Alumina is poised to make a significant impact in the catalyst, electronics, and ceramics industries, further solidifying Extraordinary Materials Inc.'s position as a key player in the advanced materials market.
Top Alumina Carrier Options for Your Needs
Alumina Carrier, an industry leader in the manufacturing and distribution of high-quality alumina products, has recently announced a new line of carriers designed to meet the growing demand for advanced materials in various industries. With their cutting-edge technology and commitment to excellence, Alumina Carrier is set to revolutionize the way businesses handle and transport materials.Founded in 1995, Alumina Carrier has grown to become a trusted name in the alumina industry. The company prides itself on its dedication to innovation and its unwavering commitment to delivering top-notch products and services to its customers. With a focus on research and development, Alumina Carrier has continuously pushed the boundaries of what is possible in the industry, setting new standards for performance, quality, and reliability.The new line of carriers from Alumina Carrier is the latest testament to the company's dedication to innovation. These carriers are designed to provide businesses with a cost-effective and efficient solution for transporting materials of various types and sizes. Whether it's in the pharmaceutical, food and beverage, or chemical industries, Alumina Carrier's carriers can be customized to meet the specific needs of each business, ensuring a seamless and reliable transport solution.One of the key features of the new carriers is their durability and resistance to corrosion and wear. Made from the finest materials using advanced manufacturing processes, these carriers are built to withstand the rigors of transportation, ensuring that the materials they carry remain in pristine condition throughout the journey. In addition, Alumina Carrier's carriers are designed to be lightweight and easy to handle, making them an ideal choice for businesses looking to streamline their operations and reduce costs.Furthermore, Alumina Carrier is committed to sustainability and environmental responsibility. The company's carriers are designed with eco-friendly materials and manufacturing processes, ensuring that businesses can transport their materials in an environmentally conscious manner. As the business world continues to prioritize sustainability, Alumina Carrier's carriers offer a responsible and forward-thinking solution for companies looking to reduce their environmental footprint.In addition to their innovative products, Alumina Carrier is also known for its exceptional customer service. With a team of experienced professionals, the company provides comprehensive support to businesses looking to integrate their carriers into their operations. From initial consultation to installation and maintenance, Alumina Carrier is dedicated to ensuring that their customers receive the highest level of service and support.The release of the new line of carriers from Alumina Carrier is a testament to the company's ongoing commitment to excellence and innovation. With their advanced technology, commitment to sustainability, and dedication to customer service, Alumina Carrier is poised to set new benchmarks in the industry. Businesses looking for a reliable and efficient solution for transporting materials need look no further than Alumina Carrier's carriers. As the industry continues to evolve, Alumina Carrier remains at the forefront, continuously pushing the boundaries of what is possible and setting new standards for performance and quality.
New Study Finds Alumina Effective for Industrial Applications
Title: Advanced Alumina Catalyst Unveiled: Enhancing Industrial Processes and SustainabilityIntroduction:In a bid to revolutionize industrial processes and promote sustainability, a leading materials science company (brand name removed) has recently introduced a groundbreaking alumina catalyst, known as Gamma Alumina. With its unique properties and versatile applications, Gamma Alumina is set to play a significant role in enhancing various sectors, ranging from petrochemicals and catalysis to energy production and wastewater treatment.The Versatility of Gamma Alumina:Gamma Alumina, a high-purity form of alumina, possesses remarkable thermal stability, high specific surface area, and excellent mechanical strength. These properties make it an ideal catalyst for multiple industrial applications.1. Petrochemical Industry:The petrochemical industry heavily relies on catalysts to facilitate crucial chemical reactions. Gamma Alumina proves to be a game-changer here by providing superior activity and efficiency for processes such as cracking, reforming, and isomerization. This catalyst enables enhanced conversion rates, reduced energy consumption, and improved product yields, thereby contributing to the overall sustainability of the industry.2. Catalysis:In the field of catalysis, Gamma Alumina offers valuable advantages. Its large surface area and unique pore structure enable efficient dispersion of active components, resulting in improved catalytic activity and selectivity. This catalyst enhances various catalytic reactions, including hydrogenation, oxidation, and dehydration, leading to increased process efficiency and reduced environmental impact.3. Energy Production:Gamma Alumina's exceptional thermal stability makes it an ideal choice for energy production applications. In the production of clean energy sources like biodiesel or hydrogen, Gamma Alumina catalysts significantly improve reaction kinetics and stability, ensuring higher yield and minimizing waste. By facilitating cleaner, more efficient energy production processes, Gamma Alumina contributes to the global transition towards sustainable energy sources.4. Environmental Applications:Wastewater treatment and emission control are critical issues that require innovative solutions. Gamma Alumina exhibits exceptional adsorption properties, enabling efficient removal of pollutants and contaminants from wastewater. Its large surface area and controlled porosity enable the removal of heavy metals, organic pollutants, and nitrogen compounds, resulting in cleaner effluents and a reduced environmental footprint.Sustainability at the Core:Beyond their applications, Gamma Alumina catalysts align perfectly with the global sustainability agenda. The production process of this catalyst significantly reduces energy consumption and waste production, contributing to a more sustainable and environmentally friendly manufacturing process. Additionally, the long lifespan and recyclability of Gamma Alumina make it an economically viable and environmentally conscious option for various industries.Conclusion:The introduction of Gamma Alumina catalysts marks a significant milestone in the quest for sustainable and efficient industrial processes. With their exceptional properties and versatility, these catalysts have the potential to revolutionize various sectors, including petrochemicals, catalysis, energy production, and waste management. The continual research and development of novel applications for Gamma Alumina further underline its central role in promoting sustainability and advancing industrial processes. As industries strive to operate in a more sustainable manner, Gamma Alumina catalysts provide a roadmap towards a greener and more efficient future.
New Study Reveals Surprising Findings about ZSM-5
Zsm 5, a leading company known for its innovative solutions in the field of chemical catalysis, has recently announced a major breakthrough in the development of a new generation of catalysts with potential applications in the petrochemical industry. This development marks a significant advancement in the company’s efforts to drive sustainable and efficient processes for the production of key chemical compounds.Founded in 1996, Zsm 5 has steadily established itself as a key player in the field of chemical catalysis, specializing in the research, development, and commercialization of catalysts for various industrial applications. With a strong focus on innovation and sustainability, the company has continuously pushed the boundaries of catalysis technology to address evolving industry needs.The latest development from Zsm 5 comes in the form of a novel catalyst with enhanced performance characteristics, specifically designed for the production of key petrochemical compounds. Leveraging its expertise in molecular design and materials science, the company has successfully engineered a catalyst that exhibits superior activity, selectivity, and stability, offering a more efficient and sustainable solution for petrochemical processes.This new catalyst has the potential to significantly impact the petrochemical industry, offering improved efficiency and cost-effectiveness in the production of a wide range of chemical compounds. The enhanced performance characteristics of the catalyst have been demonstrated through rigorous testing and evaluation, showcasing its ability to deliver higher yields and purity levels while minimizing energy consumption and environmental impact.In addition to its technical advancements, the new catalyst from Zsm 5 is also poised to address key sustainability challenges facing the petrochemical industry. By promoting more efficient and sustainable production processes, the catalyst aligns with the company’s commitment to driving environmental responsibility and resource conservation within the chemical manufacturing sector.“We are excited to introduce this groundbreaking catalyst, which represents a significant leap forward in our ongoing efforts to advance the field of chemical catalysis,” said [spokesperson], [title] at Zsm 5. “Our team of researchers and engineers have worked tirelessly to develop a catalyst that not only delivers exceptional performance, but also supports our vision for a more sustainable and efficient chemical industry.”The introduction of this new catalyst underscores Zsm 5’s dedication to pioneering innovative solutions that address the evolving needs of the chemical manufacturing sector. With a proven track record of delivering high-performance catalysts for a variety of industrial applications, the company continues to be at the forefront of catalysis technology, driving advancements that enable more sustainable and efficient chemical processes.As Zsm 5 prepares to bring its latest catalyst to market, industry professionals and stakeholders can look forward to the potential benefits it offers in terms of improved productivity, cost savings, and environmental stewardship. With its unwavering commitment to innovation and sustainability, Zsm 5 is well-positioned to shape the future of chemical catalysis and contribute to the ongoing evolution of the petrochemical industry.
Sulfur Tolerant Shift Catalyst: The Key to Improved Air Quality
Sulfur Tolerant Shift Catalyst Technology: A Game-changer in the Petroleum IndustryThe petroleum industry plays a critical role in meeting the growing energy needs of the world. As the global demand for petroleum products continues to rise, the industry is constantly seeking innovative technologies to enhance the efficiency of production processes and reduce environmental impact. One such groundbreaking technology is the Sulfur Tolerant Shift Catalyst, developed by a leading chemical engineering company.The Sulfur Tolerant Shift Catalyst is a catalyst used in the production of hydrogen through the water-gas shift reaction. This reaction is a key step in the production of hydrogen from natural gas or other hydrocarbons. Traditionally, catalysts used in this process are highly sensitive to sulfur compounds, which can deactivate the catalyst and reduce its efficiency over time. However, the Sulfur Tolerant Shift Catalyst has been engineered to withstand the presence of sulfur, thereby offering significant advantages in terms of longevity and performance.This innovative catalyst technology has the potential to revolutionize the way hydrogen is produced, offering a more robust and cost-effective solution for the petroleum industry. The company behind this groundbreaking technology has a strong track record of developing high-performance catalysts and chemical products for various industrial applications. With a team of experienced chemists, engineers, and researchers, the company is dedicated to pushing the boundaries of chemical innovation and addressing the evolving needs of the industry.The Sulfur Tolerant Shift Catalyst has undergone rigorous testing and validation to demonstrate its superior performance in real-world operating conditions. The catalyst has shown remarkable resistance to sulfur poisoning, maintaining its activity and selectivity over extended periods of operation. This breakthrough technology not only offers operational benefits such as increased catalyst life and reduced maintenance costs, but also contributes to a more sustainable and environmentally friendly production process.In addition to its technical prowess, the company is committed to providing exceptional customer support and value-added services. With a global network of technical experts and customer service professionals, the company offers comprehensive support to ensure the successful implementation and ongoing optimization of its catalyst products. This customer-centric approach has earned the company a reputation for reliability and excellence, further solidifying its position as a trusted partner in the petroleum industry.The Sulfur Tolerant Shift Catalyst technology is set to have a profound impact on the petroleum industry, offering a game-changing solution to the challenges associated with hydrogen production. As the industry continues to prioritize efficiency, cost-effectiveness, and environmental responsibility, this innovative catalyst technology presents a compelling value proposition for producers and refiners around the world. With its cutting-edge capabilities and unwavering commitment to customer satisfaction, the company is poised to lead the way in shaping the future of hydrogen production and advancing the global energy landscape.In conclusion, the Sulfur Tolerant Shift Catalyst technology represents a significant advancement in catalyst innovation, with the potential to revolutionize the petroleum industry. Backed by a company with a strong legacy of excellence and a customer-centric approach, this groundbreaking technology is poised to set new standards for performance, sustainability, and operational efficiency. As the industry embraces the need for cleaner and more efficient energy solutions, the Sulfur Tolerant Shift Catalyst stands out as a true game-changer that will shape the future of hydrogen production and propel the industry towards a more sustainable and prosperous future.
Sulfur Tolerant Shift Catalyst: What You Need to Know
Introducing a Breakthrough Sulfur Tolerant Shift Catalyst Revolutionizing the Chemical IndustryThe global chemical industry is constantly evolving, with companies seeking innovative solutions to improve efficiency and reduce environmental impact. One company at the forefront of this innovation is [company name], a leading global provider of catalysts and advanced chemical solutions. With a commitment to sustainability and technological advancement, [company name] has recently introduced a groundbreaking sulfur tolerant shift catalyst that is set to revolutionize the chemical industry.The sulfur tolerant shift catalyst, developed by [company name], is a game changer for the industry, providing a powerful solution to the persistent challenge of sulfur impurities in chemical processes. Sulfur impurities, commonly found in natural gas and other feedstocks, can pose significant operational and environmental challenges for chemical manufacturers. Traditional shift catalysts are sensitive to sulfur, leading to frequent catalyst replacement and reduced process efficiency. However, [company name]'s sulfur tolerant shift catalyst is engineered to withstand sulfur contaminants, ensuring consistent performance and prolonged catalyst life.This breakthrough catalyst is a result of [company name]'s extensive research and development efforts, leveraging years of expertise in catalysis and chemical engineering. The company's state-of-the-art R&D facilities and advanced testing capabilities have enabled the development of a catalyst that offers superior resistance to sulfur poisoning, without compromising on catalytic activity and selectivity. This represents a significant advancement in catalyst technology, addressing a long-standing industry need and unlocking new possibilities for chemical producers worldwide.The sulfur tolerant shift catalyst is poised to deliver a host of benefits to the chemical industry, enhancing process reliability, flexibility, and economic viability. By minimizing the impact of sulfur impurities, chemical manufacturers can optimize their operations and achieve higher levels of productivity and profitability. Furthermore, the catalyst's enhanced durability reduces the frequency of catalyst replacement, resulting in cost savings and operational efficiency. In addition to these tangible advantages, the use of this catalyst also contributes to environmental sustainability by reducing emissions and minimizing the environmental footprint of chemical processes.[company name]'s sulfur tolerant shift catalyst has already garnered significant interest and accolades within the industry, positioning the company as a trailblazer in catalyst innovation. With a strong commitment to technological leadership and customer satisfaction, [company name] is dedicated to supporting chemical manufacturers in realizing the full potential of this groundbreaking catalyst. By partnering with [company name], chemical producers can gain access to the latest advancements in catalyst technology, along with comprehensive technical support and expertise to optimize their catalytic processes.As the chemical industry continues to evolve and face new challenges, [company name] remains steadfast in its commitment to driving innovation and delivering sustainable solutions that create value for its customers. The introduction of the sulfur tolerant shift catalyst underscores the company's vision and capabilities in developing advanced catalysts that address critical industry needs and propel the chemical industry towards a more sustainable and efficient future.In conclusion, [company name]'s sulfur tolerant shift catalyst represents a significant milestone in catalyst technology, offering a groundbreaking solution to the long-standing challenge of sulfur impurities in chemical processes. With its exceptional resistance to sulfur poisoning and superior performance, this catalyst is set to redefine the standards of catalytic processes in the chemical industry. As [company name] continues to lead the way in catalyst innovation, it sets the stage for a new era of sustainable and efficient chemical production.Overall, the introduction of this breakthrough catalyst reinforces [company name]'s position as a trusted partner and innovator in the chemical industry, and underscores its unwavering commitment to delivering excellence and sustainability in all aspects of its business.
Efficient Tail Gas Hydrogenation Catalyst for Industrial Applications
Tail Gas Hydrogenation Catalyst is a crucial component in the process of removing sulfur from natural gas and refining crude oil. It is responsible for the conversion of harmful sulfur compounds into hydrogen sulfide, which is then easily removed from the gas stream. The latest innovation in this field comes from a leading chemical company, renowned for its expertise in developing cutting-edge catalysts for various industrial processes. This newly developed catalyst offers improved performance and efficiency, making it an ideal choice for companies looking to enhance their refining processes. This innovative catalyst is designed to effectively remove sulfur compounds from the tail gas, ensuring compliance with environmental regulations and producing cleaner fuel products. It also offers a longer lifespan and improved stability, allowing for continuous operation without the need for frequent replacements.In addition to its superior performance, this catalyst is also designed to minimize energy consumption, thereby reducing the overall operational costs for companies utilizing it in their refining processes. This is a significant advantage in today's competitive market, where companies are constantly seeking ways to improve their processes and reduce operating expenses.The company's commitment to research and development has been a driving force behind the success of this new catalyst. Their team of experienced chemists and engineers have worked tirelessly to develop a product that meets the evolving needs of the industry. By investing in state-of-the-art facilities and cutting-edge technology, the company has been able to stay at the forefront of catalyst innovation.Furthermore, the company's dedication to sustainability is evident in the design of this new catalyst. By enabling the production of cleaner fuel products, the catalyst contributes to reducing emissions and mitigating the impact of industrial processes on the environment. This aligns with the company's broader mission to develop products and solutions that promote sustainability and environmental responsibility.The launch of this new tail gas hydrogenation catalyst has been eagerly anticipated by industry experts and customers alike. Its advanced features and performance improvements are expected to set a new standard in the field of sulfur removal and refining processes. The company's extensive testing and validation processes have ensured that the catalyst meets the highest quality and performance standards, offering customers peace of mind and confidence in its reliability.In conclusion, the introduction of this new tail gas hydrogenation catalyst represents a significant advancement in the field of sulfur removal and refining processes. Its superior performance, enhanced efficiency, and focus on sustainability make it a standout choice for companies looking to improve their operations and reduce their environmental impact. With a strong track record of innovation and a commitment to excellence, the company behind this catalyst is poised to make a lasting impact on the industry.
Groundbreaking Discovery: New ZSM-5 Compound Discovered with Game-Changing Potential
Title: Zeolite Catalyst ZSM-5 Revolutionizes Petrochemical IndustryIntroduction:[Pseudonym] Industries, a highly renowned player in the chemical manufacturing industry, has recently unveiled a groundbreaking innovation that is set to revolutionize the petrochemical sector. Their latest catalyst, known as Zeolite Catalyst ZSM-5 (name changed for confidentiality reasons), promises to enhance the efficiency and effectiveness of various processes in the industry. With its unique properties and manifold advantages, ZSM-5 is expected to play a pivotal role in shaping the future of petrochemical manufacturing.1. Superior Catalytic Activity and Selectivity:ZSM-5, a next-generation zeolite catalyst, exhibits exceptional catalytic activity and selectivity. With its well-defined and highly uniform structure, ZSM-5 possesses a higher number of active sites, allowing for increased efficiency in the conversion of raw materials. Moreover, its unique molecular sieving effect results in enhanced selectivity, leading to higher yields of valuable petrochemical products. This technological breakthrough sets ZSM-5 apart from conventional catalysts and positions it as a game-changer in the field.2. Versatile Applications:One of the key strengths of ZSM-5 lies in its versatility, enabling it to be employed in a wide range of petrochemical manufacturing processes. The catalyst exhibits remarkable performance in key processes such as catalytic cracking, alkylation, isomerization, and aromatization. Its ability to promote various chemical reactions simultaneously makes it an indispensable tool for petrochemical industries seeking to optimize production and achieve cost-efficiency.3. Enhanced Product Quality:By leveraging ZSM-5's exceptional catalytic properties, manufacturers can enhance the quality of their products. The catalyst facilitates the selective conversion of undesired by-products, minimizing impurities and enhancing the purity and effectiveness of the final petrochemical outputs. The improved product quality achieved through the utilization of ZSM-5 ensures a competitive edge for manufacturers, as it meets and surpasses stringent quality standards.4. Improved Energy Efficiency:A significant advantage of ZSM-5 is its ability to enhance the energy efficiency of petrochemical processes. By enabling greater conversion rates and reducing the amount of energy-intensive steps involved, ZSM-5 minimizes the energy requirements for various manufacturing processes. This not only positively impacts the bottom line for manufacturers but also contributes to a more sustainable and environmentally friendly petrochemical industry.5. Cost Optimization:Petrochemical manufacturers worldwide constantly seek ways to optimize their production costs without compromising quality. ZSM-5 presents an excellent opportunity for achieving this goal. Its exceptional performance translates into higher yields, reduced waste, and increased operational efficiency. By implementing ZSM-5, companies can streamline their processes, reduce raw material consumption, and lower overall production costs, thereby boosting their profitability.6. Environmental Sustainability:In an era of growing environmental concerns, ZSM-5 emerges as a catalyst that aligns with sustainable practices. The reduced energy consumption and improved efficiency brought about by utilizing ZSM-5 directly contribute to a lower carbon footprint. Additionally, the enhanced selectivity of ZSM-5 facilitates the production of fewer harmful by-products and the conversion of waste materials, further reducing environmental impact. By adopting ZSM-5, petrochemical industries can actively contribute to a greener and more sustainable future.Conclusion:Zeolite Catalyst ZSM-5 by [Pseudonym] Industries represents a paradigm shift in the petrochemical industry. With its superior catalytic activity, versatility, and environmentally friendly attributes, ZSM-5 enables manufacturers to enhance product quality, efficiency, and cost-effectiveness. This revolutionary catalyst ensures manufacturers continue to meet ever-increasing demands for petrochemical products while simultaneously reducing their environmental footprint. As the industry evolves, ZSM-5 is poised to play a pivotal role in shaping a sustainable and innovative future for petrochemical manufacturing.