Tail Gas Hydrogenation Catalyst: The Solution to Carbon Emission
By:Admin
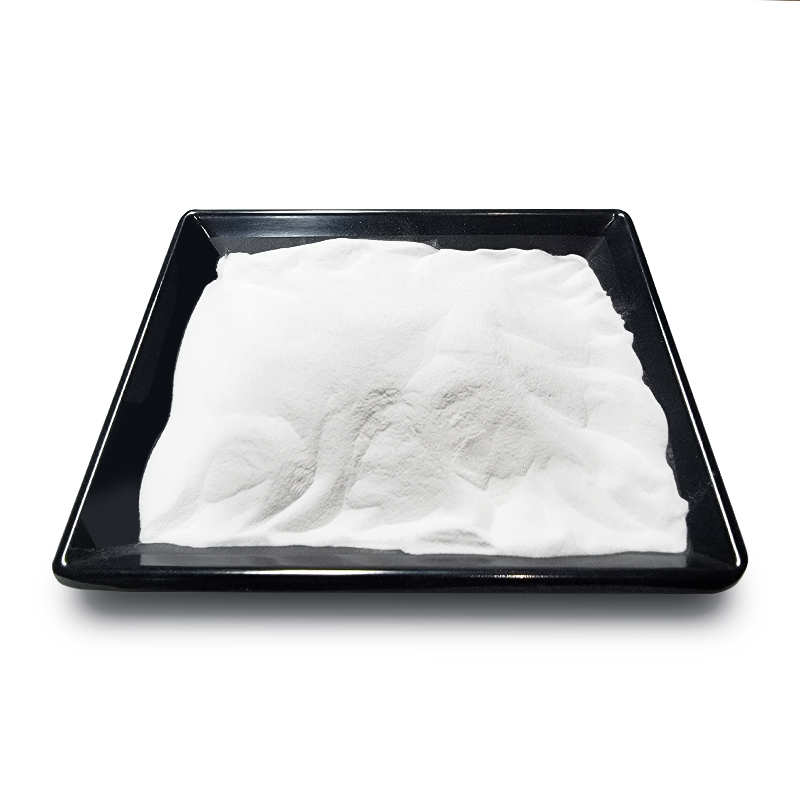
Tail gas is commonly produced during various refining processes in the petroleum industry. It consists of the unreacted hydrogen and sulfur compounds that are typically found in fuel gas and light gas oil. These compounds are harmful to the environment and need to be removed before the gas can be utilized or released safely. To address this issue, a groundbreaking catalyst has emerged - the Tail Gas Hydrogenation Catalyst, which has revolutionized the petroleum refining industry.
This catalyst, developed by a leading chemical company, has proven to be highly efficient in removing sulfur compounds and other harmful impurities from tail gas. Its effectiveness lies in its ability to promote the hydrogenation reactions responsible for converting sulfur compounds into hydrogen sulfide, a less harmful compound. The catalyst provides a surface for the reactions to occur, thus increasing their rate and efficiency.
The Tail Gas Hydrogenation Catalyst is composed of various active components, such as metal oxides and promoters, which play a vital role in the catalytic process. The careful selection and combination of these components ensure that the catalyst is both highly reactive and long-lasting. Additionally, the company has implemented proprietary manufacturing techniques to ensure consistent catalyst quality and performance.
What sets this catalyst apart from previous iterations in the market is its high selectivity towards sulfur compounds, leading to a remarkable reduction in sulfur content in tail gas. This selectivity ensures that only the harmful impurities are removed, while other valuable components of the gas are left intact. The result is cleaner gas that can be utilized more efficiently or released with significantly reduced environmental impact.
Furthermore, the Tail Gas Hydrogenation Catalyst boasts exceptional thermal stability, enabling it to operate at high temperatures encountered in petroleum refining processes. This characteristic is crucial in maintaining catalyst activity and prolonging its lifespan. By withstanding these extreme conditions, the catalyst can continue to deliver exceptional performance, reducing the frequency of catalyst replacement and consequently decreasing overall operational costs.
The company behind this innovative catalyst has a long-standing reputation in the chemical industry for its commitment to research and development. It employs a team of renowned scientists and engineers who continuously strive to improve their products and develop cutting-edge solutions for various industries. Their expertise and dedication have led to the development of groundbreaking catalysts like the Tail Gas Hydrogenation Catalyst.
In addition to its technical excellence, the company values sustainability and seeks to implement environmentally friendly practices throughout its operations. This commitment is reflected in the design and manufacturing of the catalyst, which focuses on reducing emissions and minimizing waste generation. By incorporating sustainability into their core principles, the company aims to contribute to a cleaner, greener future for the refining industry.
The introduction of the Tail Gas Hydrogenation Catalyst marks a significant milestone in the petroleum refining industry. Its unmatched selectivity, thermal stability, and sustainability features have positioned it as a game-changer in the field. By effectively removing harmful sulfur compounds from tail gas, the catalyst improves overall efficiency, reduces environmental impact, and ensures compliance with stringent regulations.
As the petroleum industry continues to evolve and face growing sustainability demands, the Tail Gas Hydrogenation Catalyst serves as a shining example of how innovative technologies can pave the way for a cleaner, more efficient future. With its exceptional performance and the company's commitment to continuous improvement, the catalyst is set to revolutionize the refining industry, driving it towards a greener tomorrow.
Company News & Blog
New Hydrogenation Catalyst for Tail Gas Emissions Shows Promising Results
Tail Gas Hydrogenation Catalyst is a crucial component in the process of removing sulfur and other contaminants from industrial tail gases. It plays a vital role in ensuring compliance with environmental regulations and maintaining the integrity of equipment and infrastructure in the oil and gas industry.The development and production of Tail Gas Hydrogenation Catalyst is a complex and specialized process that requires advanced technology and expertise. One company that excels in this field is {Company Name}. With years of experience and a commitment to innovation, {Company Name} has established itself as a leading provider of Tail Gas Hydrogenation Catalyst solutions.{Company Name} was founded in [year] and has since grown to become a global leader in the production of catalysts and other specialty chemicals for the energy industry. The company's state-of-the-art manufacturing facilities and research laboratories are equipped with the latest technology and staffed by a team of highly skilled engineers and scientists. This allows {Company Name} to develop and produce high-performance catalysts that meet the specific needs of its clients.One of {Company Name}'s flagship products is its Tail Gas Hydrogenation Catalyst, which is designed to effectively remove sulfur compounds from tail gases. Sulfur removal is a critical step in the production of clean fuels, as sulfur oxides are a major contributor to air pollution and can cause severe damage to processing equipment. By using {Company Name}'s Tail Gas Hydrogenation Catalyst, oil and gas companies can significantly reduce their environmental footprint and improve the performance and longevity of their plant assets.In addition to its superior performance, {Company Name}'s Tail Gas Hydrogenation Catalyst is also known for its reliability and cost-effectiveness. The company has invested heavily in research and development to ensure that its catalysts deliver consistent results and require minimal maintenance. This, in turn, helps its clients to achieve higher operational efficiency and lower overall operating costs.Furthermore, {Company Name} provides comprehensive technical support and customer service to help its clients optimize the performance of its catalysts. Its team of experts works closely with customers to understand their specific requirements and provide tailored solutions that meet their unique needs. This level of dedication and support has earned {Company Name} a reputation as a trusted partner in the oil and gas industry.With a strong focus on sustainability and innovation, {Company Name} continues to push the boundaries of catalyst technology. It is constantly exploring new ways to improve the performance and environmental impact of its products, and to expand its range of solutions for the energy industry.The market for Tail Gas Hydrogenation Catalyst is projected to grow significantly in the coming years, driven by the increasing demand for cleaner fuels and stricter environmental regulations. As such, {Company Name} is well-positioned to capitalize on these opportunities and further solidify its position as a leader in this space.In conclusion, {Company Name} is a powerhouse in the production of Tail Gas Hydrogenation Catalyst, offering a combination of cutting-edge technology, industry expertise, and unwavering commitment to customer satisfaction. Its innovative solutions have made a positive impact on the energy industry, and its continued dedication to excellence ensures a promising future for the company and its clients alike.
Newly Discovered ZSM-48 Mineral Holds Great Promise
Oil and gas exploration and processing have always been challenging and complex tasks. In order to help the industry achieve consistent success, scientists, and engineers have continuously endeavored to develop new materials and better technologies. One of the most promising advances in this area in recent years is the development of Zsm-48. The material is now being used in various applications within the oil and gas industry which has resulted in improved efficiency and profitability.Zsm-48 is a type of zeolite that has shown to have excellent properties for catalysis applications. The material has a unique structure with a high silica to alumina ratio which makes it ideal for selective conversion of hydrocarbons. The increased selectivity and activity of Zsm-48 are due to its unique pore system which creates an ideal environment for chemical reaction. Efficient and effective use of this material is beneficial for the oil and gas industry since it can enhance processing efficiency, increase yield, and significantly reduce the production cost.This innovative material is being employed in various applications in the oil and gas industry. One of the most notable is in crude oil refining, where Zsm-48 is used to remove sulfur compounds. This is a crucial step in the refining process, as sulfur compounds left in crude oil can cause corrosion in downstream equipment and release pollutants into the environment. By using Zsm-48, oil refineries can achieve better-quality fuels while reducing their carbon footprint.Another application of Zsm-48 is in the conversion of heavy oils. Heavy oils are cheaper than light oils, but due to their high viscosity, they are harder to process and refine. To increase the value of heavy oils, they need to be converted into lighter, more valuable products. Zsm-48 has been found to be highly effective in converting heavy oils into high-value products such as gasoline and diesel, making this innovative material an essential part of modern petroleum processing.Zsm-48 has also been used in the development of new catalyst technology for petrochemical processes. The catalysts developed using Zsm-48 are more selective and efficient, leading to higher yields and reduced costs in the production of various chemical products, including plastics, polymers, and fertilizers. Cracking heavy feedstock into lighter gas products using Zsm-48 catalysts are among the most groundbreaking achievements of this material.The use of Zsm-48 is not limited to the oil and gas industry. This innovative material has also been employed in the growing field of environmental remediation. Zsm-48 can effectively remove pollutants and other contaminants from water sources, including heavy metals, pesticides, and pharmaceutical products. Its selectivity and high adsorption capacity make it an ideal choice for water purification.The importance and relevance of Zsm-48 cannot be overstated, as the oil and gas industry continues its search for innovative solutions to improve efficiency and reduce the environmental impact of hydrocarbon operations. The development and application of this innovative material can lead to substantial benefits in various fields related to petroleum processing, leading to increased value and competitive advantage for companies and improving the lives of individuals all over the world.Companies like {Company Name} have become the preferred choice for businesses in the oil and gas industry looking for quality materials like Zsm-48. The company has been providing innovative products and solutions for the oil and gas, petrochemical, and water treatment industries for years. The company specializes in delivering products to customers in over 30 countries worldwide, and they work closely with customers to provide customized solutions that are tailored to meet the specific requirements of each project and application.With their expert knowledge of materials sciences and engineering, {Company Name} is committed to supporting the industry through continuous research and development, innovation, and strategic alliances with other industry leaders and partners. Their team of experts ensures that clients receive quality products and excellent service that reflects the company's values of sustainability, integrity, and excellence.In conclusion, as the oil and gas industry continues its search for innovative solutions that can improve efficiency and reduce environmental impact, Zsm-48 presents a breakthrough material. The application of this innovative zeolite has revolutionized petroleum processing and opened up new avenues for water treatment and environmental remediation. Companies like {Company Name} have been instrumental in providing access to quality Zsm-48 materials and expertise, which are essential for the success of new and existing projects.
Catalyst Carrier Unveils Revolutionary New Technology for Improved Performance
Catalyst Carrier, a leading provider of cutting-edge solutions for the chemical industry, has recently announced a major breakthrough in catalyst technology that is set to revolutionize the way chemical processes are conducted. The company, known for its innovative approach to catalysis, has developed a new carrier material that promises to significantly enhance the performance and efficiency of catalysts used in a wide range of chemical reactions.The new carrier material, which is a proprietary blend of advanced ceramics and metals, has been designed to address the limitations of traditional catalyst carriers. It offers superior thermal stability, mechanical strength, and surface area, making it an ideal platform for catalyst deposition and dispersion. This breakthrough is expected to have a profound impact on the chemical industry, enabling manufacturers to develop more sustainable and cost-effective processes for the production of various chemicals, polymers, and specialty materials.In a recent statement, the company's CEO expressed excitement about the potential of the new carrier material, stating that it represents a major milestone in the company's ongoing commitment to innovation and excellence. "We believe that this breakthrough has the potential to transform the way catalysts are utilized in the chemical industry," the CEO said. "Our new carrier material offers unprecedented performance and durability, opening up new possibilities for a wide range of chemical processes. We are proud to be at the forefront of this exciting development and look forward to working with our partners to unlock its full potential."The development of the new carrier material is a result of extensive research and development efforts at Catalyst Carrier. The company has a long history of innovation in catalyst technology, leveraging its expertise in materials science, chemical engineering, and process design to create novel solutions for the industry. The new carrier material is the latest in a series of successful advancements by the company, which has consistently demonstrated its ability to push the boundaries of what is possible in catalysis.The potential applications of the new carrier material are vast and diverse. It is expected to find use in a wide range of chemical processes, including those related to petrochemicals, pharmaceuticals, fine chemicals, and environmental remediation. The material's high thermal stability and mechanical strength make it well-suited for high-temperature reactions and harsh operating conditions, while its large surface area and optimized pore structure enable efficient catalyst loading and utilization.One of the key benefits of the new carrier material is its potential to improve the sustainability of chemical processes. By enabling more efficient catalyst utilization, it can help reduce the consumption of raw materials and energy, lower the generation of waste and emissions, and ultimately contribute to a more environmentally friendly and economically viable chemical industry. This aligns with Catalyst Carrier's commitment to driving positive change through its innovative solutions, and the company is eager to work with its partners to explore the possibilities of the new material.As the chemical industry continues to evolve, with a growing emphasis on sustainability and efficiency, the development of new catalyst technologies will be crucial. Catalyst Carrier's breakthrough in carrier material represents a significant step forward in this regard, offering a promising avenue for the development of next-generation chemical processes. The company is poised to play a leading role in the commercialization of the new material, collaborating with industry partners to bring its benefits to fruition.In conclusion, Catalyst Carrier's development of a new carrier material for catalysts is a major advancement that holds great promise for the chemical industry. The material's superior performance and versatility position it as a game-changer for a wide range of chemical processes, with far-reaching benefits in terms of sustainability, efficiency, and economics. As the company continues to leverage its expertise and innovation, it is well-positioned to drive positive change in the industry and create lasting value for its partners and customers.
What is Dechlorination? Definition and Meaning in Medical Dictionary
Dechlorination: A Vital Step in Water TreatmentDo you know that almost all tap water has a small amount of chlorine in it? Chlorine is necessary to kill harmful bacteria and other contaminants that may be present in water. However, while chlorine is an effective disinfectant, it can also have undesired effects, such as the unpleasant taste and odor of water. This is where dechlorination comes in.Dechlorination is the process of removing chlorine from water. It is typically done by using a dechlorination agent, which neutralizes the chlorine and converts it into chloride. Dechlorination is a crucial step in water treatment, especially for processes that follow disinfection, such as fish farming and aquariums.Dechlorination agents are typically made up of sodium bisulfite or sodium sulfite. These chemicals are added to the water to neutralize excess chlorine, rendering it safe for use. Dechlorination agents are commonly available in liquid and powder form. They are easy to use and very effective in removing chlorine from water.One of the most common uses of dechlorination agents is in swimming pools. Chlorine is used in swimming pools to kill off bacteria and other unwanted contaminants. However, chlorinated water can be harsh on the skin and can cause irritation to swimmers. This is where dechlorination comes in. By using a dechlorination agent, pool water can be converted into safe, non-irritating, and odorless water.Dechlorination agents are also commonly used in the food and beverage industry. Chlorine is often used to disinfect equipment and surfaces where food and beverages are processed and prepared. However, excess chlorine can lead to off-tastes and odors in the final product. Dechlorination agents are used to ensure that the water used in the production process is safe and of high quality.In conclusion, dechlorination is an essential step in the water treatment process. It helps to remove excess chlorine from water, making it safe and pleasant to use. Dechlorination agents are effective, safe, and readily available, and can be used for a wide range of applications, including swimming pools, food and beverage production, and aquariums. If you're looking for a way to make your water safer and better-tasting, consider using a dechlorination agent.
Innovative Catalyst Carrier Spheralite Revolutionizing Industry Technology
Catalyst Carrier Spheralite (need remove brand name), a high-performance catalyst carrier product, has been making waves in the industry as one of the most innovative and effective solutions for a wide range of catalytic processes. With its unique spherical shape and high surface area, Spheralite has proven to be a game-changer for many companies looking to improve the efficiency and effectiveness of their catalyst systems.Spheralite is a product of a leading chemical company with a strong focus on innovation and sustainability. With decades of experience in the development and manufacturing of specialty chemicals, the company has established itself as a trusted partner for businesses across various industries, including oil and gas, petrochemicals, and environmental technology.The introduction of Spheralite has further solidified the company's position as a pioneer in the chemical industry, offering cutting-edge solutions that address the evolving needs of its customers. The unique properties of Spheralite make it an ideal choice for a wide range of catalytic applications, including refining, emissions control, and chemical production.One of the key advantages of Spheralite is its spherical shape, which provides a higher density and packing efficiency compared to traditional catalyst carriers. This allows for a greater surface area and improved mass transfer, resulting in enhanced catalytic performance and overall process efficiency. Furthermore, Spheralite's high crush strength and thermal stability make it a reliable choice for demanding operating conditions, ensuring long-term durability and performance.The company's commitment to sustainability is also reflected in the production of Spheralite. By utilizing advanced manufacturing processes and sustainable raw materials, the company ensures that Spheralite is not only high-performing but also environmentally friendly. This aligns with the company's broader mission to develop products that contribute to the reduction of environmental impact and promote sustainable practices within the industry.In addition to its technical advantages, Spheralite also offers operational benefits for companies utilizing catalyst systems. Its uniform and consistent shape allows for easy handling and filling of catalyst beds, reducing the risk of dust formation and minimizing potential health and safety hazards for operators. This contributes to a safer and more efficient working environment, further enhancing the overall value proposition of Spheralite for businesses.The versatility of Spheralite also makes it suitable for a wide range of catalysts, including precious metals and zeolites, providing companies with the flexibility to optimize their catalytic processes based on specific requirements and performance goals. Its compatibility with various catalytic formulations and applications makes Spheralite a versatile and cost-effective solution for companies seeking to improve their catalytic performance.The introduction of Spheralite has already generated significant interest and positive feedback from companies across the industry. Many have recognized the potential of Spheralite to unlock new opportunities for performance improvement and operational efficiency within their catalytic processes. With its proven track record and strong technical support from the company, Spheralite is poised to become a key player in the catalyst carrier market.Looking ahead, the company remains committed to further advancing the development of Spheralite and expanding its applications to address the evolving needs of the industry. By harnessing its expertise in chemical innovation and sustainable practices, the company is well-positioned to continue delivering cutting-edge solutions that drive value for its customers and contribute to a more sustainable future.In conclusion, Catalyst Carrier Spheralite is a testament to the company's dedication to innovation, sustainability, and customer-centric solutions. Its unique properties and operational benefits make it a compelling choice for companies seeking to enhance the performance and sustainability of their catalytic processes. With a strong foundation and a clear vision for the future, Spheralite is set to reshape the landscape of catalyst carriers and drive positive change within the industry.
High-Quality Activated Alumina for Catalyst Carriers at Low Prices
Activated Alumina for Catalyst Carrier: What You Need to KnowCatalysts are substances that increase the rate of a chemical reaction without being consumed in the process. They play a crucial role in various industries, including petrochemicals, pharmaceuticals, and automotive. Activated alumina has been recognized as an effective carrier for catalysts due to its high surface area, porosity, and thermal stability. In this blog, we will discuss activated alumina for catalyst carrier and its benefits.What is Activated Alumina?Activated alumina is a highly porous material made from aluminum hydroxide. It has a large internal surface area, typically around 350-400 m²/g, and a high pore volume of around 0.5-0.8 ml/g. Activated alumina is widely used in various applications such as gas drying, water purification, and catalyst carrier due to its excellent adsorption capacity and thermal stability.Activated Alumina for Catalyst CarrierCatalyst carrier plays a vital role in heterogeneous catalysis. It serves as a support for the active catalyst material and provides a high surface area for the reactant to interact with the active sites. Activated alumina has been extensively used as a catalyst carrier due to its unique characteristics. The high surface area and porosity of activated alumina allow for enhanced mass transfer and diffusion of reactants, improving the catalytic efficiency.Benefits of Activated Alumina for Catalyst Carrier1. High Surface Area: The high surface area of activated alumina provides a large contact area for the reactants, thus increasing the efficiency of the catalyst.2. Thermal Stability: Activated alumina can withstand high temperatures, making it ideal for high-temperature catalytic reactions.3. Porosity: The porosity of activated alumina allows for the easy diffusion of reactants, thus enhancing the catalytic activity.4. Stability: Activated alumina has excellent stability and does not react with most chemicals, making it ideal for various catalytic applications.5. Cost-effective: Activated alumina is cost-effective compared to other catalyst carriers like zeolites.Applications of Activated Alumina Catalyst CarrierActivated alumina has been widely used in various catalytic applications such as:1. Petrochemicals: Activated alumina has been used as a catalyst carrier in the production of linear alkylbenzenes, isomerization, and hydrogenation reactions.2. Pharmaceuticals: Activated alumina has been used in the production of various pharmaceuticals such as penicillin, vitamin C, and anti-inflammatory drugs.3. Automotive: Activated alumina has been used in catalytic converters for the removal of harmful gases like carbon monoxide, nitrogen oxides, and hydrocarbons from exhaust gases.ConclusionActivated alumina is an excellent catalyst carrier due to its high surface area, porosity, and thermal stability. It has been extensively used in various industries such as petrochemicals, pharmaceuticals, and automotive for various catalytic applications. As a leading manufacturer of activated alumina for catalyst carrier, we at CHEMXIN provide high-quality products at affordable prices. Contact us for more information.
Highly Effective Alumina Catalyst for Various Applications
Gamma Alumina Catalyst, a revolutionary new product in the field of catalysis, has been making waves in the industry with its unique and innovative features. Developed by a leading chemical company, this catalyst has the potential to transform the way chemical reactions are carried out, offering improved efficiency and performance compared to traditional catalysts.The company behind Gamma Alumina Catalyst is renowned for its expertise in chemical engineering and innovation. With a strong focus on research and development, the company has a track record of introducing groundbreaking products that have been instrumental in advancing various industries. The launch of Gamma Alumina Catalyst is yet another testament to the company's commitment to excellence and innovation.Gamma Alumina Catalyst is a high-performance catalyst that is designed to facilitate a wide range of chemical reactions. Its unique composition and structure make it suitable for use in various processes, including petroleum refining, petrochemicals production, and environmental applications. The catalyst is known for its exceptional activity, selectivity, and stability, making it a preferred choice for many industrial applications.One of the key features of Gamma Alumina Catalyst is its high surface area, which provides enhanced accessibility for reactant molecules. This results in improved conversion rates and reduced energy consumption, leading to significant cost savings for end users. Additionally, the catalyst's robust structure allows for extended operational lifespans, minimizing the frequency of catalyst replacement and downtime for maintenance.Furthermore, Gamma Alumina Catalyst exhibits excellent thermal stability, enabling it to maintain its performance under high-temperature operating conditions. This makes it particularly well-suited for use in processes that involve elevated temperatures, such as hydrocracking and hydrotreating. The catalyst's superior thermal resistance ensures consistent and reliable performance, even in the most demanding industrial environments.In addition to its exceptional physical and chemical properties, Gamma Alumina Catalyst is also characterized by its environmental sustainability. The catalyst is designed to minimize the generation of undesirable by-products and waste, contributing to a greener and more environmentally friendly manufacturing process. With a growing emphasis on sustainable practices, the use of Gamma Alumina Catalyst aligns with the industry's increasing focus on eco-friendly solutions.The launch of Gamma Alumina Catalyst has generated widespread interest and excitement within the chemical industry. Its innovative features and potential benefits have captured the attention of companies and organizations seeking to improve their production processes and enhance overall efficiency. The catalyst's versatility and adaptability make it a valuable asset for a diverse range of applications, offering a compelling solution for various industrial challenges.With the introduction of Gamma Alumina Catalyst, the company has once again reaffirmed its position as a leading innovator in the field of chemical engineering. The catalyst's advanced technology and performance capabilities underscore the company's dedication to delivering cutting-edge solutions that address the evolving needs of its customers. By leveraging its expertise and resources, the company has succeeded in developing a product that has the potential to drive positive change and innovation across the industry.Looking ahead, the company is poised to continue its focus on research and development, exploring new opportunities to advance the capabilities of Gamma Alumina Catalyst and expand its applicability across different sectors. With a commitment to excellence and a forward-thinking approach, the company remains dedicated to pushing the boundaries of what is possible in catalysis, paving the way for a future shaped by innovation and progress.
New Methanation Catalyst Technology: A Breakthrough in Methane Conversion
Methanation Catalyst Technology Revolutionizes Green Energy ProductionWith the increasing global emphasis on reducing greenhouse gas emissions and transitioning to renewable energy sources, the demand for innovative solutions that can efficiently convert carbon dioxide into valuable resources has been rapidly growing. Among the forefront of this revolution is [company name], a leading provider of advanced catalysts, who has recently developed a groundbreaking Methanation Catalyst that has the potential to transform the way renewable energy is produced.[Company name] has been at the forefront of catalyst innovation since its inception, with a commitment to developing sustainable technologies that address the challenges of climate change and contribute to a greener future. The company’s team of dedicated researchers and engineers have been working tirelessly to develop a Methanation Catalyst that exceeds the performance of conventional catalysts, enabling a more cost-effective and energy-efficient conversion of carbon dioxide into methane gas.The Methanation Catalyst developed by [company name] leverages cutting-edge materials and proprietary manufacturing processes to deliver superior performance in carbon dioxide methanation reactions. The catalyst’s unique composition and structure provide an unparalleled level of activity and selectivity, allowing for the efficient conversion of carbon dioxide into high-purity methane gas. This breakthrough technology has the potential to significantly reduce the carbon footprint of various industries, such as power generation, chemical processing, and transportation, by enabling the production of renewable natural gas from waste carbon dioxide streams.The implementation of [company name]’s Methanation Catalyst holds immense potential for mitigating climate change and advancing the transition towards a low-carbon economy. By providing a viable pathway for recycling carbon dioxide emissions into valuable energy resources, this innovative catalyst aligns with the global efforts to combat climate change and promote sustainable development. Furthermore, the enhanced efficiency and performance of the Methanation Catalyst can also contribute to the economic viability of renewable energy production, offering a compelling solution for businesses seeking to reduce their environmental impact while maintaining operational competitiveness.In addition to its environmental and economic benefits, [company name]’s Methanation Catalyst also presents a valuable opportunity for fostering collaborative partnerships within the energy and environmental sectors. With its demonstrated potential to enable a more sustainable and efficient utilization of carbon dioxide, the catalyst technology can serve as a catalyst for driving cross-industry collaborations and accelerating the adoption of renewable energy solutions. Whether through joint research initiatives, technology licensing agreements, or supply partnerships, the Methanation Catalyst has the capacity to facilitate synergistic engagements that further the advancement of sustainable energy production and environmental stewardship.As the global community continues to prioritize the transition towards a low-carbon economy, [company name] remains committed to driving innovation and shaping the future of sustainable energy technologies. The introduction of the Methanation Catalyst stands as a testament to the company’s unwavering dedication to developing impactful solutions that address the pressing challenges of climate change and contribute to the advancement of a greener, more sustainable world. With its transformative potential in converting carbon dioxide into renewable natural gas, the Methanation Catalyst epitomizes the pivotal role that innovative catalyst technologies play in driving the evolution of green energy production.In conclusion, the development of [company name]’s Methanation Catalyst marks a significant milestone in the journey towards a more sustainable and carbon-neutral future. The technological advancements and environmental benefits of the catalyst position it as a game-changer in renewable energy production, offering a compelling solution for reducing carbon emissions and harnessing the potential of carbon dioxide as a valuable resource. As [company name] continues to push the boundaries of catalyst innovation, the Methanation Catalyst represents a beacon of hope in the quest for a cleaner and more sustainable energy landscape.
Key Benefits of Residue Hydrogenation Catalysts for Industrial Applications
[Company Name], a leading provider of innovative catalyst solutions, has recently introduced a highly efficient Residue Hydrogenation Catalyst to meet the evolving needs of the petrochemical industry. This new catalyst offers enhanced performance and reliability, enabling refineries to optimize their residue conversion process and improve overall operational efficiency.The Residue Hydrogenation Catalyst is designed to facilitate the conversion of heavy hydrocarbon residues into valuable products such as gasoline and diesel. By effectively removing impurities and upgrading low-quality feedstocks, this catalyst helps refineries maximize their output and enhance the quality of their end products. With its advanced formulation and superior activity, [Company Name]'s Residue Hydrogenation Catalyst offers a cost-effective solution for addressing the challenges associated with residue processing."We are proud to introduce our latest innovation in catalyst technology, the Residue Hydrogenation Catalyst," said [Spokesperson Name], CEO of [Company Name]. "This cutting-edge catalyst exemplifies our commitment to delivering high-performance solutions that enable our customers to achieve greater operational efficiency and competitiveness in the market. By leveraging our expertise in catalyst development, we continue to drive advancements in the petrochemical industry and support the sustainable growth of our partners."The Residue Hydrogenation Catalyst is a testament to [Company Name]'s extensive research and development capabilities, which are backed by a team of experienced chemists and engineers. Through rigorous testing and validation, this catalyst has demonstrated exceptional stability and selectivity, making it an ideal choice for refineries looking to enhance their residue conversion processes. Its robust performance can withstand the challenging operating conditions commonly encountered in hydroprocessing units, providing operators with peace of mind and confidence in their operations.In addition to its technical advantages, [Company Name]'s Residue Hydrogenation Catalyst is supported by a comprehensive technical service offering. The company's dedicated team of experts provides on-site support, process optimization, and troubleshooting to ensure that customers derive maximum value from their catalyst investment. By fostering a collaborative partnership with clients, [Company Name] aims to deliver tailored solutions that address their specific needs and drive long-term success.The introduction of the Residue Hydrogenation Catalyst underscores [Company Name]'s ongoing commitment to innovation and customer-centricity. By investing in research and development, the company continues to expand its portfolio of advanced catalyst solutions, offering a diverse range of products tailored to different refining processes. Its relentless pursuit of excellence enables [Company Name] to stay ahead of industry trends and anticipate the evolving needs of its customers, positioning the company as a trusted partner in the global petrochemical sector.As the petrochemical industry faces increasing pressure to improve efficiency and sustainability, [Company Name]'s Residue Hydrogenation Catalyst represents a valuable contribution to the industry. By enabling refineries to maximize their resource utilization and minimize environmental impact, this catalyst aligns with the broader industry goals of reducing carbon emissions and enhancing operational performance. Its introduction heralds a new era of innovation and progress in residue processing, paving the way for a more optimized and sustainable refining landscape.In conclusion, [Company Name]'s Residue Hydrogenation Catalyst is a testament to the company's dedication to advancing catalyst technology and supporting the success of its customers. With its superior performance, technical support, and commitment to sustainability, this catalyst embodies [Company Name]'s vision of empowering refineries to achieve operational excellence and drive industry-leading performance. As the petrochemical landscape continues to evolve, [Company Name] remains at the forefront of catalyst innovation, shaping the future of the industry and driving positive change for its partners and stakeholders.
Addressing Water Quality Issues in Domestic Wells: California State Water Resources Control Board Provides Updates
Water is a critical resource that is essential for human survival. Maintaining its quality is equally important. However, water quality continues to be a significant concern, especially in California. Groundwater is the primary source of drinking water in the state, and it supplies nearly 40% of the state's total water consumption. Addressing this issue, the California State Water Resources Control Board and Gama Alumina have recently come together to launch the GAMA Domestic Well program. Groundwater quality in California is affected by various factors, including natural sources, human activities, and industrial activities. The most prevalent contaminants found in groundwater include nitrates, arsenic, lead, and salts. These contaminants affect the water quality and pose a significant health risk to the people consuming it. The GAMA Domestic Well program aims to address these issues by providing free testing and treatment to domestic well owners across the state.The GAMA Domestic Well program is a joint venture between the California State Water Resources Control Board and Gama Alumina, a global provider of solutions for the aluminum industry. Gama Alumina has over sixty years of experience in the water treatment industry, offering a range of products and services to customers worldwide. The company is known for its expertise in water treatment technologies, specifically in the areas of filtration, ion exchange, and reverse osmosis.The Gama Alumina has committed to offer its technological support to the GAMA Domestic Well program across California. This collaboration with the State Water Board will help to supplement and improve water quality to communities located near the company's manufacturing facility. Gama's mission is to provide sustainable water solutions to contribute to the enrichment of quality of life and protecting the environment.The GAMA Domestic Well program's primary objective is to provide free testing for private domestic wells and to track changes in groundwater quality across California. The program will allow participants to access the latest water testing technologies, including the isotope and geochemical analyses, to identify the sources of contamination. Gama Alumina will also provide technical support for water treatment systems interventions, including filtration, desalination, and ion exchange.The program will prioritize vulnerable communities that are most affected by water quality issues, including low-income households, rural communities, indigenous people, and communities of color. Many of these communities face unique challenges through ongoing drought, water scarcity, and aquifer depletion. Addressing their specific needs and challenges is vital to the success of the GAMA program, as it aims to deliver equitable access to clean water for all Californians.The GAMA program will collect and compile data from the groundwater monitoring wells drilled across the state and provide public access to the data. This information will be valuable to state and regional stakeholders and informed communities to better understand groundwater quality changes and take preservation measures. Gama Alumina is committed to sustainable industrial growth and strives to preserve the environment. The company invests in innovation and technology to develop highly efficient processes to produce aluminum and provide long-term solutions to reduce waste and enhance industrial practices. The firm believes that collective action is vital to creating lasting positive impact and recovery.The Gama Alumina has a proven track record of delivering sustainable solutions to the aluminum industry. By providing technical support to the GAMA Domestic Well program, the company aims to ensure that communities have access to clean and safe drinking water. The company will employ its proprietary technology to boost the program's efforts to improve groundwater quality throughout the state.To sum up, the GAMA Domestic Well Program, in conjunction with Gama Alumina, creates a platform that ensures continued access to clean water across the State of California. With Gama's technical support, this project will offer a range of solutions that will provide free domestic well testing and water treatment systems interventions. The GAMA Domestic Well Program offers a reliable data source and will boost the state's efforts to ensure water quality safety and enhance clean water accessibility for all communities. Overall, Gama Alumina is committed to providing solutions that enhance the water industry and the quality of life to customers by embracing innovation, community, and sustainability.