- Home
- Blog
- All-New Catalyst Material Discovered to Help Reduce Emissions and Increase Efficiency in Various Industries
All-New Catalyst Material Discovered to Help Reduce Emissions and Increase Efficiency in Various Industries
By:Admin
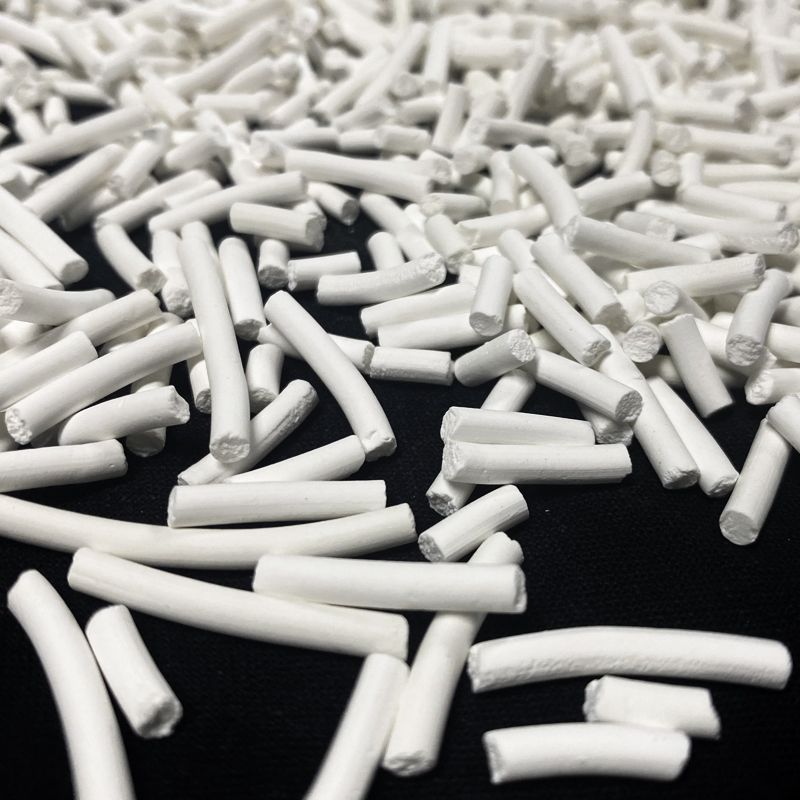
Introduction:
Zeolite catalysts have emerged as a crucial component in various industries, ranging from petroleum refining to environmental protection. One particular catalyst that has gained significant attention is ZSM-5, a zeolite with exceptional catalytic properties and zeolite structure. This groundbreaking catalyst, devoid of its brand name, has the potential to revolutionize several industrial processes while promoting a more sustainable future. This article aims to shed light on the remarkable applications and accomplishments of ZSM-5, unraveling its immense potential for driving environmental solutions.
Understanding ZSM-5:
ZSM-5 is a crystalline zeolite catalyst characterized by its unique combination of micropores and larger cavities, enabling efficient molecular sieving. With a three-dimensional connected channel system, ZSM-5 provides a strong framework for facilitating chemical reactions. This powerful catalyst exhibits high selectivity and activity, making it desirable for various industrial applications.
Driving Innovation in Petroleum Refining:
The implementation of ZSM-5 catalyst in petroleum refining processes has proven to be a game-changer. By promoting the conversion of heavy hydrocarbons into lighter molecules, ZSM-5 enables the production of valuable fuels and petrochemicals. This not only boosts production efficiency but also reduces dependence on conventional crude oil sources. Additionally, the use of ZSM-5 in fluid catalytic cracking demonstrates improved gasoline octane levels while reducing toxic emissions.
Revolutionizing Petrochemical Industry:
In the petrochemical industry, ZSM-5 has become instrumental in the conversion of methanol to light olefins. This process, known as methanol-to-olefins (MTO), offers a breakthrough pathway for producing ethylene and propylene, the building blocks of various plastics and synthetic materials. By utilizing ZSM-5, the MTO process circumvents the need for traditional crude oil-based feedstocks, thereby reducing carbon emissions and promoting a transition towards sustainable feedstock alternatives.
Environmental Applications:
One of the most remarkable aspects of ZSM-5 lies in its potential for environmental remediation. ZSM-5's unique morphology and catalytic properties make it ideal for the abatement of harmful pollutants. Research suggests that ZSM-5 can effectively adsorb and decompose volatile organic compounds (VOCs) responsible for air pollution. Moreover, this versatile catalyst shows promise in removing heavy metals and organic contaminants from wastewater, providing a cost-effective and sustainable solution for water treatment.
Greenhouse Gas Management:
As the world grapples with the challenges posed by climate change, ZSM-5 presents itself as a valuable tool for greenhouse gas management. By utilizing ZSM-5 catalysts, carbon capture and conversion technologies can be enhanced, trapping and transforming carbon dioxide (CO2) into valuable products such as methanol and other commodity chemicals. This innovative approach not only reduces CO2 emissions but also creates a potential market for renewable energy sources, thereby promoting a circular economy.
Future Prospects and Collaborations:
The growing interest in ZSM-5 has spurred collaborations between research institutes, universities, and industries worldwide. Scientists are actively exploring the synthesis of modified ZSM-5 variations to optimize catalytic performance and expand its range of applications. Furthermore, efforts are being made to develop ZSM-5-based catalysts that can effectively convert biomass into biofuels, upholding sustainability in the energy sector.
Conclusion:
Zeolite catalyst ZSM-5 has emerged as a robust resource for various industries, offering innovative solutions to environmental challenges and promoting sustainable practices. Its unique structure, combined with exceptional catalytic properties, drives advancements in petroleum refining, petrochemical production, environmental remediation, and greenhouse gas management. As research and development efforts continue to unfold, the widespread adoption of ZSM-5 catalysts holds immense potential to reshape existing industries and pave the way for a greener and more sustainable future.
Company News & Blog
Newly Developed Zsm-5 Shows Promising Results for Advanced Materials
ZSM-5 is a zeolite material used in the catalytic cracking of petroleum for the production of gasoline. It is a highly-effective catalyst due to its uniform pore structure, high surface area, and strong acidity. The use of ZSM-5 has enabled the petroleum industry to produce gasoline with higher octane numbers and better fuel efficiency.In recent years, the demand for ZSM-5 has been steadily increasing as the automotive industry continues to grow. As a result, the production and supply of ZSM-5 have become vital for the petrochemical industry. This has led to the development of new and more efficient methods for producing ZSM-5, such as the innovative process developed by {company name}.{Company name} is a leading manufacturer of zeolite materials and has been at the forefront of ZSM-5 production for many years. The company has developed a proprietary method for producing ZSM-5 that is more cost-effective and environmentally friendly than traditional methods. This has allowed {company name} to become a key supplier of ZSM-5 to the petrochemical industry.The unique production method developed by {company name} involves the use of advanced catalyst synthesis technology and precise control of reaction conditions. This results in the production of ZSM-5 with higher purity and improved performance compared to traditional methods. Furthermore, the process developed by {company name} has significantly reduced energy consumption and waste generation, making it a more sustainable option for ZSM-5 production.The success of {company name} in the production of ZSM-5 has not gone unnoticed. The company has received accolades for its innovative production process and has become a trusted supplier to major petrochemical companies around the world. This has helped {company name} to expand its market share and establish itself as a leader in the zeolite materials industry.In addition to ZSM-5, {company name} also manufactures a wide range of other zeolite materials for various applications, including catalytic cracking, adsorption, and ion exchange. The company's expertise in zeolite materials has allowed it to provide tailored solutions to its customers, addressing their specific needs and requirements.Looking ahead, {company name} is committed to further advancing its production technology and expanding its product offerings. The company continues to invest in research and development to improve the performance and cost-effectiveness of its zeolite materials. Additionally, {company name} is exploring new applications for its zeolite materials, seeking to diversify its product portfolio and capture new market opportunities.As the global demand for gasoline and petrochemical products continues to grow, the need for high-quality zeolite materials such as ZSM-5 will remain crucial. With its innovative production methods and extensive expertise, {company name} is well-positioned to meet this demand and continue to be a leading supplier to the petrochemical industry.In conclusion, ZSM-5 is an essential catalyst for the production of high-quality gasoline, and {company name} is at the forefront of its production. With its innovative production methods and commitment to excellence, {company name} is a trusted supplier of zeolite materials to the petrochemical industry, and is poised for continued success in the years to come.
Tail Gas Hydrogenation Catalyst: The Solution to Carbon Emission
Tail Gas Hydrogenation Catalyst: Revolutionizing the Petroleum Refining IndustryTail gas is commonly produced during various refining processes in the petroleum industry. It consists of the unreacted hydrogen and sulfur compounds that are typically found in fuel gas and light gas oil. These compounds are harmful to the environment and need to be removed before the gas can be utilized or released safely. To address this issue, a groundbreaking catalyst has emerged - the Tail Gas Hydrogenation Catalyst, which has revolutionized the petroleum refining industry. This catalyst, developed by a leading chemical company, has proven to be highly efficient in removing sulfur compounds and other harmful impurities from tail gas. Its effectiveness lies in its ability to promote the hydrogenation reactions responsible for converting sulfur compounds into hydrogen sulfide, a less harmful compound. The catalyst provides a surface for the reactions to occur, thus increasing their rate and efficiency.The Tail Gas Hydrogenation Catalyst is composed of various active components, such as metal oxides and promoters, which play a vital role in the catalytic process. The careful selection and combination of these components ensure that the catalyst is both highly reactive and long-lasting. Additionally, the company has implemented proprietary manufacturing techniques to ensure consistent catalyst quality and performance.What sets this catalyst apart from previous iterations in the market is its high selectivity towards sulfur compounds, leading to a remarkable reduction in sulfur content in tail gas. This selectivity ensures that only the harmful impurities are removed, while other valuable components of the gas are left intact. The result is cleaner gas that can be utilized more efficiently or released with significantly reduced environmental impact.Furthermore, the Tail Gas Hydrogenation Catalyst boasts exceptional thermal stability, enabling it to operate at high temperatures encountered in petroleum refining processes. This characteristic is crucial in maintaining catalyst activity and prolonging its lifespan. By withstanding these extreme conditions, the catalyst can continue to deliver exceptional performance, reducing the frequency of catalyst replacement and consequently decreasing overall operational costs.The company behind this innovative catalyst has a long-standing reputation in the chemical industry for its commitment to research and development. It employs a team of renowned scientists and engineers who continuously strive to improve their products and develop cutting-edge solutions for various industries. Their expertise and dedication have led to the development of groundbreaking catalysts like the Tail Gas Hydrogenation Catalyst.In addition to its technical excellence, the company values sustainability and seeks to implement environmentally friendly practices throughout its operations. This commitment is reflected in the design and manufacturing of the catalyst, which focuses on reducing emissions and minimizing waste generation. By incorporating sustainability into their core principles, the company aims to contribute to a cleaner, greener future for the refining industry.The introduction of the Tail Gas Hydrogenation Catalyst marks a significant milestone in the petroleum refining industry. Its unmatched selectivity, thermal stability, and sustainability features have positioned it as a game-changer in the field. By effectively removing harmful sulfur compounds from tail gas, the catalyst improves overall efficiency, reduces environmental impact, and ensures compliance with stringent regulations.As the petroleum industry continues to evolve and face growing sustainability demands, the Tail Gas Hydrogenation Catalyst serves as a shining example of how innovative technologies can pave the way for a cleaner, more efficient future. With its exceptional performance and the company's commitment to continuous improvement, the catalyst is set to revolutionize the refining industry, driving it towards a greener tomorrow.
Major Alumina Company Makes Groundbreaking Announcement in the Industry
Gamma Alumina, a leading provider of advanced materials solutions, is poised to revolutionize the industry with its groundbreaking innovations. The company’s unwavering commitment to research and development has paved the way for the creation of cutting-edge products that promise to drive progress across various sectors.With a diverse range of applications, Gamma Alumina’s materials have been the catalyst for breakthrough technological advancements in fields as wide-ranging as transportation, energy, and electronics. From superior automotive components that enhance fuel efficiency to energy-efficient building materials that transform traditional construction practices, the company's portfolio is characterized by versatility and performance.Gamma Alumina’s success can be attributed to its relentless pursuit of excellence in all areas of its operations. Guided by a team of world-class scientists and engineers, the company stays at the forefront of material science research, anticipating future needs and developing innovative solutions ahead of the curve. This focus on innovation allows the company to consistently outperform competitors and meet the ever-evolving demands of industries worldwide.One of the company’s most noteworthy advancements is the development of a high-performance ceramic material. By harnessing the unique properties of gamma alumina, Gamma Alumina has created a material that is incredibly resistant to wear and tear, while also possessing excellent thermal and chemical stability. This revolutionary product has the potential to disrupt numerous industries, from aerospace to medical technology, by offering improved performance, durability, and longevity compared to traditional materials.The advantages of Gamma Alumina’s high-performance ceramic material are particularly evident in the transportation industry. Traditional metal components in engines and transmissions are subject to wear and corrosion over time, leading to increased maintenance costs and reduced efficiency. By introducing gamma alumina-based ceramic parts, manufacturers can significantly enhance the lifespan of critical engine components, resulting in longer-lasting and more efficient vehicles. Moreover, the reduced weight of these ceramic parts contributes to improved fuel efficiency, positioning Gamma Alumina as a key player in the drive towards sustainable transportation.In the energy sector, Gamma Alumina’s innovations are revolutionizing the way power is harnessed and transmitted. The company’s ceramic materials offer superior resistance to high temperatures and chemical corrosion, making them ideal for use in high-performance batteries and fuel cells. By leveraging these advanced materials, energy storage systems become more durable, efficient, and capable of meeting the growing demands of renewable energy sources. As a result, Gamma Alumina is playing a vital role in the global transition towards a greener and more sustainable future.It is also worth noting that Gamma Alumina actively collaborates with leading researchers, industry experts, and government agencies to further advance the potential applications of their high-performance ceramic materials. By combining their internal expertise with external insights, the company ensures that its products meet the highest standards of performance and reliability in a rapidly changing world.With an unwavering commitment to research and development, Gamma Alumina continues to position itself as a market leader in the advanced materials industry. Through its groundbreaking innovations, the company envisions a future where traditional materials are replaced with sustainable alternatives that offer unparalleled durability, performance, and efficiency. As industries across the globe embrace the transformational potential of Gamma Alumina’s materials, the world is inching closer to a more sustainable and technologically advanced future.
Discover the Benefits of Residue Hydrogenation Catalysts for Chemical Processing
Residue Hydrogenation Catalyst Catalyst Technology Inc. (CTI) is a leading provider of advanced catalysts and process technologies for a range of industries, including oil and gas, petrochemical, and environmental industries. With a strong focus on innovation and sustainability, CTI has developed a wide range of catalysts that are designed to improve process efficiency, reduce emissions, and lower overall operating costs for its customers.In its latest breakthrough, CTI has developed a highly effective Residue Hydrogenation Catalyst that is set to revolutionize the refining industry. This new catalyst offers superior performance in residue hydroprocessing applications, enabling refiners to produce higher quality products while significantly reducing operating costs.Residue hydroprocessing is a critical step in the refining process, where heavy, high-sulfur residues are converted into lighter, lower-sulfur products. This process is essential for meeting environmental regulations and producing high-quality fuels and petrochemicals. However, traditional catalysts used in residue hydroprocessing often suffer from deactivation and require frequent regeneration, leading to increased downtime and operational expenses.The new Residue Hydrogenation Catalyst from CTI addresses these challenges by delivering outstanding activity, selectivity, and stability. This innovative catalyst is specifically engineered to withstand the harsh operating conditions of residue hydroprocessing, resulting in longer catalyst life and reduced maintenance requirements. As a result, refiners can achieve higher run lengths, lower catalyst consumption, and improved product yields.CTI’s Residue Hydrogenation Catalyst also offers superior sulfur and nitrogen removal capabilities, resulting in cleaner products and compliance with stringent environmental regulations. Additionally, the catalyst’s high conversion efficiency allows refiners to maximize their process yields and optimize their production economics."We are excited to introduce our latest Residue Hydrogenation Catalyst to the market," said Dr. Michael Chen, Chief Technology Officer at CTI. "This innovative catalyst represents a significant advancement in residue hydroprocessing technology, and we believe it will make a substantial impact on our customers' bottom line."In addition to its exceptional performance, CTI’s Residue Hydrogenation Catalyst is also designed to be compatible with existing process equipment, making it easy for refiners to adopt the new catalyst without major modifications to their facilities. This seamless integration ensures a smooth transition and minimizes downtime during catalyst replacement.CTI’s dedication to sustainability is evident in the development of this new catalyst, which is engineered to maximize resource utilization and minimize waste generation. By enabling refiners to produce higher quality, cleaner products with fewer resources, CTI’s Residue Hydrogenation Catalyst contributes to the industry’s efforts to reduce environmental impact and promote sustainable practices.With its proven track record of delivering innovative, high-performance catalysts, CTI is well-positioned to lead the market in residue hydroprocessing technology. The company’s extensive expertise in catalyst design, testing, and optimization, combined with its strong commitment to customer satisfaction, makes CTI a trusted partner for refiners seeking to improve their operations and stay ahead of the competition.As the demand for cleaner, higher-quality fuels and petrochemicals continues to grow, CTI’s Residue Hydrogenation Catalyst offers a compelling solution for refiners looking to enhance their performance and achieve their sustainability goals. With its unmatched performance, stability, and environmental benefits, this new catalyst is set to become a game-changer in the refining industry, solidifying CTI’s position as a leader in advanced catalyst technologies.
Innovative new technology revolutionizes the industry
ZSM-48 is a revolutionary new technology that has the potential to change the way we think about energy production. This innovative product, developed by the leading company in the field of energy solutions, combines cutting-edge technology with sustainable practices to create a cleaner and more efficient energy source.The ZSM-48 is a compact and efficient energy storage system that can be used to power everything from homes to large industrial facilities. It harnesses the power of renewable energy sources such as solar and wind, and stores it for use when it is needed most. This means that energy can be generated and stored during times of low demand, and then used when demand is at its peak, reducing the need for fossil fuels and lowering overall energy costs.In addition to its innovative energy storage capabilities, ZSM-48 is also environmentally friendly. It is designed to have minimal impact on the environment and is made from sustainable materials, ensuring that it is as eco-friendly as possible. This makes it an attractive option for businesses and individuals looking to reduce their carbon footprint while still meeting their energy needs.The company behind ZSM-48 is a leader in the field of energy solutions, with a strong reputation for developing cutting-edge technology that is both effective and reliable. They have a long history of providing innovative solutions to the energy challenges of today, and ZSM-48 is just the latest example of their commitment to finding sustainable and efficient energy solutions.The company is dedicated to creating technology that not only meets the needs of today, but also anticipates the needs of tomorrow. They are constantly researching and developing new ways to harness renewable energy sources and create sustainable energy solutions that are both effective and affordable. With ZSM-48, they have once again demonstrated their ability to bring game-changing technology to the market.The introduction of ZSM-48 has the potential to have a significant impact on the energy industry. Its innovative design and sustainable practices make it an attractive option for businesses and individuals looking to reduce their reliance on fossil fuels and transition to cleaner and more sustainable energy sources. As the demand for renewable energy continues to grow, products like ZSM-48 will play a crucial role in meeting that demand and paving the way for a greener and more sustainable future.The company is excited about the potential of ZSM-48 and is confident that it will be a game-changer in the energy industry. They believe that this revolutionary new technology will help to usher in a new era of clean and efficient energy production, and they are committed to continuing to develop and innovate in this field. With ZSM-48, they have once again proven that they are at the forefront of the energy solutions industry, and are dedicated to driving positive change for the environment and for the future of energy production.In conclusion, ZSM-48 is a groundbreaking new technology that has the potential to revolutionize the energy industry. Its innovative design, sustainable practices, and cutting-edge technology make it a promising option for businesses and individuals looking to transition to cleaner and more efficient energy sources. With the support of the company behind it, ZSM-48 is poised to make a significant impact on the energy industry and help pave the way for a more sustainable future.
Revolutionary Zeolite Catalysts Enhance Eco-friendly Cement Manufacturing Processes
Technology, cleaner cement production, sustainable solutions, environmental impact.In the global push for sustainability, industries are looking for ways to reduce their environmental impact. One of the most polluting sectors is the cement industry, which accounts for approximately 8% of global CO2 emissions. However, thanks to innovative technologies, such as Clariant Catalyst Technology, the industry can now strive for more sustainable solutions.Clariant Catalyst Technology is a zeolite catalyst that improves the combustion process in cement production, resulting in cleaner emissions. This technology effectively reduces the environmental impact of cement production through the reduction of emissions such as NOx, CO, and particulate matter.The revolutionary technology has already been tested in several industrial cement kilns, and the results are promising. The technology has been shown to cut down NOx emissions by up to 70%, CO emissions by up to 60%, and particulate matter by up to 50%, all while maintaining the same level of cement quality. Clariant Catalyst Technology is a sustainable solution to the challenges faced by the cement industry concerning the environment. The technology ensures that the cement industry meets its obligations and makes significant strides in achieving environmental sustainability.Benefits of Clariant Catalyst Technology for Cement Production1. Cleaner EnvironmentThe use of Clariant Catalyst Technology significantly reduces emissions of NOx, CO, and particulate matter in the cement production process. This means that it helps keep the environment clean and healthy for both humans and plants.2. SustainabilityThe technology is a step towards the reduction of the carbon footprint of cement production. This makes it a sustainable solution to the environmental challenges faced by the cement industry.3. EfficiencyThe use of Clariant Catalyst Technology increases the efficiency of the cement production process, which translates to savings in energy costs and other related expenses. This makes the technology an attractive proposition for manufacturers looking to gain a competitive edge in the industry.4. User-friendlyThe technology is easy to install and operate. Cement manufacturers can easily integrate it into their existing systems without disrupting their process flow.Challenges of Implementing Clariant Catalyst Technology1. Initial InvestmentThe initial cost of implementing the technology may be a challenge for some organizations. However, the long-term benefits of the technology in terms of environmental sustainability and cost savings outweigh the initial investment.2. Resistance to ChangeThe implementation of new technology can often be met with resistance from employees who are accustomed to the existing processes. However, with proper training and effective communication, this challenge can be overcome.ConclusionThe cement industry has a significant impact on the environment, and it is therefore essential that the industry looks for sustainable solutions. Clariant Catalyst Technology is a step in the right direction, as it reduces the environmental impact of cement production while maintaining the same level of quality. The technology ensures that the cement industry meets its environmental obligations while maintaining efficiency and profitability. Overall, Clariant Catalyst Technology is a solution that can make a difference in the cement production process and contribute towards a cleaner and healthier environment for future generations. Therefore, adoption of the technology is the way forward for sustainable cement production.
Effective Catalyst for Chemical Reactions: Al2O3 Catalyst
Al2o3 Catalyst Supporting Sustainable Growth in Chemical IndustryThe chemical industry is a crucial part of the global economy, providing essential materials and products used in a wide variety of sectors, including automotive, construction, healthcare, and agriculture. However, the chemical manufacturing process often involves the use of energy-intensive and environmentally-damaging processes. To address these challenges and support sustainable growth in the chemical industry, a leading catalyst manufacturer, {company}, has developed an innovative Al2o3 catalyst that offers significant environmental benefits.{Company} is a renowned provider of catalyst solutions for the chemical industry, with a strong focus on sustainability and environmental responsibility. The company has a proven track record of developing high-performance catalysts that enable more efficient and eco-friendly production processes, helping their customers reduce their environmental footprint and achieve their sustainability goals.The newly developed Al2o3 catalyst is a testament to {company}'s commitment to innovation and sustainability. This advanced catalyst is designed to be used in a wide range of chemical manufacturing processes, where it facilitates key reactions while minimizing energy consumption and waste generation. Its unique properties make it an ideal option for companies seeking to enhance the sustainability of their operations without compromising on performance.One of the key advantages of the Al2o3 catalyst is its ability to improve the efficiency of critical chemical reactions, leading to higher yields and reduced energy consumption. By maximizing the conversion of raw materials into desired products, this catalyst helps chemical manufacturers optimize their production processes and minimize waste. Additionally, the use of Al2o3 catalyst can lead to significant cost savings for companies, as it enables them to achieve higher productivity with lower resource inputs.Furthermore, the Al2o3 catalyst plays a crucial role in reducing the environmental impact of chemical manufacturing. By promoting cleaner and more efficient production processes, it helps companies minimize their carbon footprint and decrease their overall environmental footprint. This is particularly important in light of the increasing focus on sustainability and environmental stewardship across the chemical industry.{Company} is dedicated to ensuring that its catalyst solutions not only deliver outstanding performance but also adhere to the highest environmental standards. The Al2o3 catalyst undergoes rigorous testing and quality control to ensure that it meets the strictest environmental and safety requirements, providing customers with peace of mind and confidence in their sustainable practices. By choosing {company}'s Al2o3 catalyst, chemical manufacturers can demonstrate their commitment to sustainability and environmental stewardship, while also benefiting from improved operational efficiency and cost savings.In addition to its environmental benefits, the Al2o3 catalyst offers versatility and compatibility with a wide range of chemical processes. This makes it a valuable tool for a diverse array of applications, including petrochemicals, fine chemicals, and specialty chemicals. Its flexibility and performance make it an attractive choice for companies looking to enhance the sustainability of their operations without compromising on the quality or range of their product offerings.With its cutting-edge Al2o3 catalyst, {company} is poised to make a significant impact on the chemical industry, driving sustainable growth and innovation. By providing an advanced catalyst solution that prioritizes both performance and environmental responsibility, the company is empowering its customers to achieve their sustainability goals while remaining competitive in a rapidly evolving market.As the chemical industry continues to evolve and adapt to new environmental and regulatory challenges, innovative solutions like the Al2o3 catalyst will play a crucial role in shaping its future. {Company} is proud to be at the forefront of this movement, supporting the transition towards a more sustainable and environmentally conscious chemical industry. With its unwavering commitment to excellence and sustainability, {company} is well-positioned to continue driving positive change and delivering value to its customers and the industry as a whole.In conclusion, the development of the Al2o3 catalyst represents a significant milestone for {company} and a major advancement for the chemical industry. By offering a catalyst solution that combines exceptional performance with environmental responsibility, the company is paving the way for a more sustainable and prosperous future for chemical manufacturers around the world. As the adoption of sustainable practices becomes increasingly essential, {company}'s Al2o3 catalyst stands out as a superior choice for companies seeking to enhance their environmental impact without compromising on their operational excellence.
Newly Developed ZSM-48: The Latest Breakthrough in Technology
ZSM-48 Catalyst: Revolutionizing the Petroleum IndustryThe petroleum industry plays a crucial role in the global economy, providing fuel and other products that are essential for transportation, heating, and numerous other applications. With the increasing demand for petroleum products, there is a growing need for innovative technologies to improve efficiency and sustainability in the production process. This is where the ZSM-48 catalyst comes into play, offering a groundbreaking solution that is set to revolutionize the petroleum industry.The ZSM-48 catalyst is a highly efficient zeolite catalyst that is designed to enhance the production of high-octane gasoline and other valuable petroleum products. Developed by a team of skilled researchers and engineers at a leading chemical company, this catalyst has been specifically engineered to address the challenges faced by the petroleum industry, offering improved performance and cost-effectiveness.One of the key advantages of the ZSM-48 catalyst is its ability to facilitate the conversion of low-value feedstocks into high-quality gasoline, diesel, and other products. This is achieved through the catalyst's unique molecular structure, which enables it to selectively crack larger hydrocarbons into smaller, more valuable molecules. As a result, refineries using the ZSM-48 catalyst can maximize the yield of desirable products while minimizing the production of unwanted by-products.In addition to its superior performance, the ZSM-48 catalyst also offers environmental benefits. By enabling refineries to operate more efficiently and produce higher-quality products, the catalyst helps to reduce energy consumption and greenhouse gas emissions. This aligns with the industry's ongoing efforts to enhance sustainability and minimize its environmental impact.Furthermore, the ZSM-48 catalyst is designed to be highly versatile and adaptable to different refining processes. Its robust and stable structure allows it to withstand harsh operating conditions, making it suitable for a wide range of applications. Whether used in fluid catalytic cracking units or other refining processes, the catalyst has demonstrated its ability to deliver consistent and reliable performance.The company behind the ZSM-48 catalyst has a long-standing reputation for delivering innovative solutions to the petroleum industry. With a strong focus on research and development, the company is committed to pushing the boundaries of catalyst technology and providing its customers with cutting-edge products that deliver tangible benefits. Its team of experts is dedicated to collaborating with refineries and other partners to understand their specific needs and develop tailored solutions that address their unique challenges.In line with this commitment, the company has invested significant resources in the development and commercialization of the ZSM-48 catalyst. This has involved rigorous testing and validation to ensure that the catalyst meets the highest standards of performance and reliability. As a result, refineries can have confidence in the capabilities of the ZSM-48 catalyst and its potential to drive operational improvements and cost savings.Looking ahead, the company is poised to continue its leadership in the catalyst technology space, with a strong pipeline of innovations in the works. This includes ongoing research into advanced catalysts that offer even greater performance and sustainability benefits, as well as efforts to expand the application of its existing catalysts across new markets and regions.In summary, the ZSM-48 catalyst represents a game-changer for the petroleum industry, offering a powerful tool for refineries to enhance their operations and achieve their business objectives. With its exceptional performance, environmental advantages, and versatility, the catalyst is well-positioned to drive positive change across the industry and support its evolution towards a more sustainable and efficient future. As refineries embrace the potential of the ZSM-48 catalyst, they can look forward to unlocking new opportunities and staying ahead of the curve in a rapidly evolving market.
Understanding the Properties and Uses of Gamma Alumina
Gamma alumina, a high-performance material used for a wide range of industrial applications, has gained significant attention in recent years due to its exceptional properties and versatility. As a leader in the production of gamma alumina, {Company name} has been at the forefront of developing innovative solutions for various industries, ranging from catalyst supports to electronic ceramics.{Company name} is a trusted manufacturer and supplier of gamma alumina, with a strong focus on quality, reliability, and customer satisfaction. With state-of-the-art production facilities and a dedicated team of experts, the company has been able to consistently deliver high-quality gamma alumina products that meet the stringent demands of the market.Gamma alumina, also known as γ-alumina, is a crystalline form of aluminum oxide that exhibits superior thermal stability, high surface area, and excellent catalytic properties. These characteristics make it an ideal choice for a wide range of applications, including catalyst supports for the petrochemical and chemical industries, as well as adsorbents for gas and liquid purification processes.One of the key advantages of gamma alumina is its high surface area, which provides a large number of active sites for catalytic reactions. This property makes it particularly effective in catalyzing various chemical reactions, such as the conversion of hydrocarbons in refinery processes, the production of chemicals and petrochemicals, and the treatment of emissions in environmental control systems.In addition to its use as a catalyst support, gamma alumina is also widely employed in the production of electronic ceramics, where its excellent dielectric properties and thermal stability make it an ideal material for manufacturing components such as insulators, resistors, and capacitors. Furthermore, its high surface area and pore volume make it suitable for applications in the pharmaceutical and healthcare industries, where it is used as an adsorbent for drug delivery systems and as a support material for chromatography.As a leading supplier of gamma alumina, {Company name} is committed to continuously improving and expanding its product range to meet the evolving needs of its customers. The company's research and development efforts are focused on enhancing the properties and performance of gamma alumina, as well as exploring new applications and market opportunities for this innovative material.{Company name}'s dedication to quality and innovation has earned it a strong reputation in the industry, and its gamma alumina products are trusted by customers worldwide for their reliability and performance. With a strong emphasis on sustainable and responsible manufacturing practices, the company is also committed to minimizing its environmental impact and contributing to the long-term sustainability of the industries it serves.In conclusion, gamma alumina is a versatile and high-performance material with a wide range of industrial applications, and {Company name} is a trusted partner for businesses looking for reliable and high-quality gamma alumina products. With its proven expertise and commitment to excellence, the company continues to play a key role in driving innovation and advancing the use of gamma alumina in various industries.
Sulfur Recovery Catalyst: Latest Developments and News
Claus Sulfur Recovery Catalyst is a crucial component in the oil and gas industry, as it plays a significant role in the process of recovering sulfur from hydrogen sulfide gas. This catalyst is essential for ensuring environmental compliance and maintaining operational efficiency in gas processing facilities. The company {} is a leading manufacturer and supplier of Claus Sulfur Recovery Catalyst, with a strong reputation for providing high-quality products and excellent customer service.With a focus on innovation and sustainability, {} has been at the forefront of developing advanced catalyst technologies for sulfur recovery applications. The company's Claus Sulfur Recovery Catalyst is designed to maximize sulfur recovery efficiency while minimizing operating costs and environmental impact. {}'s catalysts are tailored to meet the specific requirements of each customer, ensuring optimal performance and reliability in a wide range of operating conditions.In addition to its cutting-edge catalyst solutions, {} offers technical support and consulting services to help customers optimize their sulfur recovery processes. The company's team of experienced professionals works closely with clients to understand their unique challenges and develop customized solutions that address their specific needs. With a commitment to innovation and continuous improvement, {} is dedicated to helping its customers achieve long-term success and sustainability in their operations.As environmental regulations continue to tighten, sulfur recovery efficiency has become a top priority for gas processing facilities around the world. {}'s Claus Sulfur Recovery Catalyst is designed to help customers meet and exceed regulatory requirements, ensuring compliance with emissions standards and minimizing environmental impact. By utilizing {}'s advanced catalyst technology, customers can achieve higher sulfur recovery rates, reduce sulfur dioxide emissions, and operate their facilities in an environmentally responsible manner.With a global presence and a strong commitment to customer satisfaction, {} has established itself as a trusted partner for sulfur recovery catalyst solutions. The company's extensive network of sales and technical support professionals enables it to deliver exceptional service and support to customers in every corner of the world. Whether it's providing on-site troubleshooting and optimization support or delivering catalyst products in a timely manner, {} is dedicated to meeting the needs of its customers and helping them succeed in their operations.In conclusion, {} is a leading provider of Claus Sulfur Recovery Catalyst, offering innovative solutions and exceptional customer service to the oil and gas industry. With a focus on sustainability and environmental compliance, the company is helping customers around the world optimize their sulfur recovery processes and achieve long-term success. As the demand for sulfur recovery efficiency continues to grow, {} remains committed to driving innovation and delivering value to its customers in the global market.